Какое свойство металлов обеспечивает возможность их успешно их обработки давлением
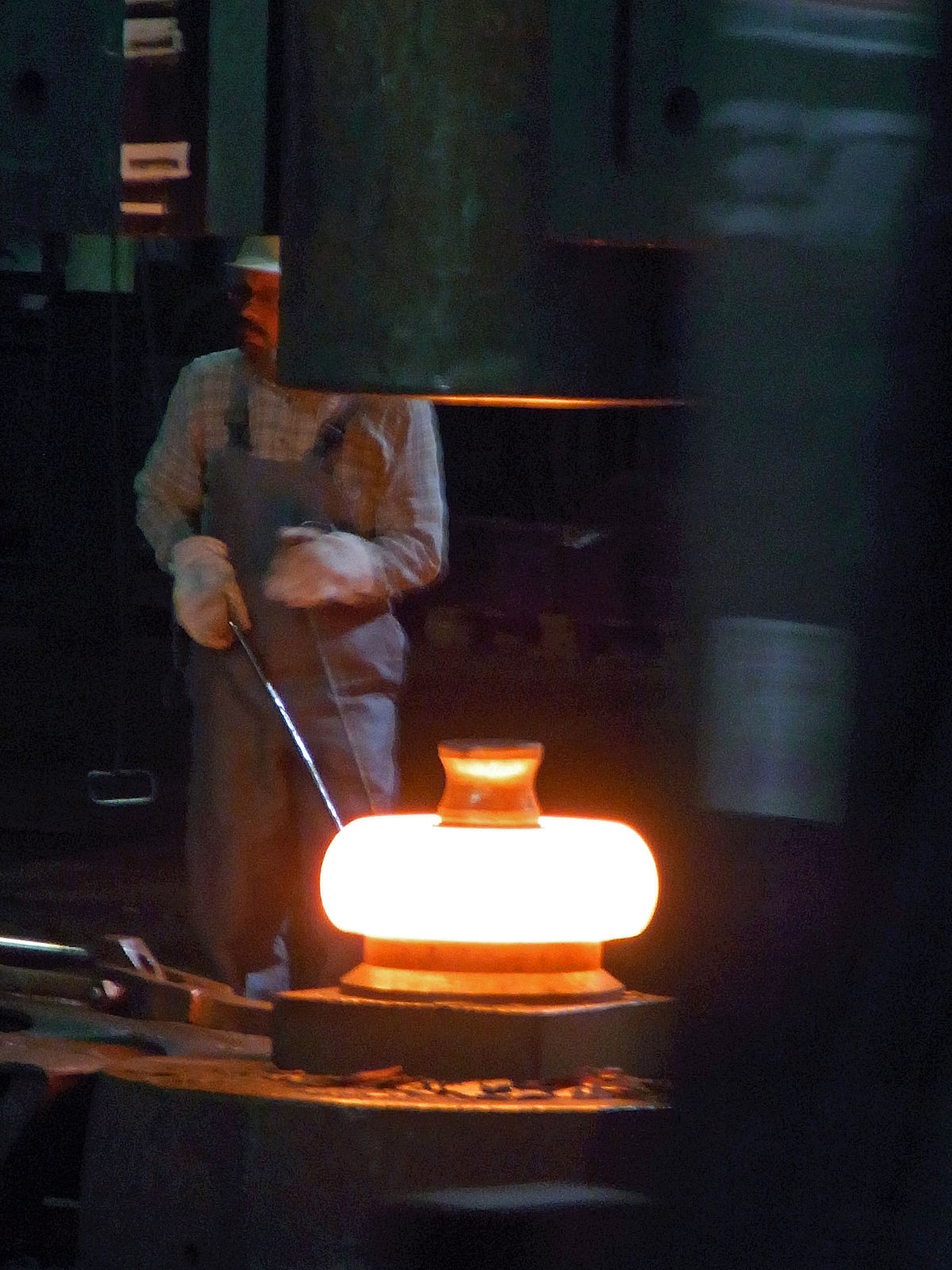
Ковка — один из видов обработки металлов давлением
Обработка металлов давлением — технологический процесс получения заготовок или деталей в результате силового воздействия инструмента на обрабатываемый материал.
Виды обработки металлов давлением[править | править код]
Процессы обработки металлов давлением по назначению подразделяют на два вида:
- для получения заготовок постоянного поперечного сечения по длине (прутков, проволоки, лент, листов), применяемых в строительных конструкциях или в качестве заготовок для последующего изготовления из них деталей только обработкой резанием или с использованием предварительного пластического формоизменения, основными разновидностями таких процессов являются прокатка, прессование и волочение;
- для получения деталей или заготовок (полуфабрикатов), имеющих формы и размеры, приближённые к формам и размерам готовых деталей, и требующих обработки резанием лишь для придания им окончательных размеров и получения поверхности заданного качества; основными разновидностями таких процессов являются ковка и штамповка.
Прокатка[править | править код]
Прокатка — процесс пластического деформирования тел между вращающимися приводными валками.
Прессование[править | править код]
Прессование заключается в продавливании заготовки, находящейся в замкнутой форме, через отверстие матрицы, причём форма и размеры поперечного сечения выдавленной части заготовки соответствуют форме и размерам отверстия матрицы.
Волочение[править | править код]
Волочение заключается в протягивании заготовки через сужающуюся полость матрицы или через межвалковое пространство образованное двумя или более валками; площадь поперечного сечения заготовки уменьшается и получает форму поперечного сечения отверстия матрицы.
Ковка[править | править код]
Ковкой изменяют форму и размеры заготовки путём последовательного воздействия универсальным инструментом на отдельные участки нагретой заготовки.
Штамповка[править | править код]
Штамповкой изменяют форму и размеры заготовки с помощью специализированного инструмента — штампа (для каждой детали изготовляют свой штамп), который состоит из матрицы, пуансона и дополнительных частей. Различают объёмную и листовую штамповку. При объёмной штамповке в качестве заготовки используют сортовой металл, разрезаемый на заготовки. На заготовку в процессе объемной штамповки воздействуют специализированным инструментом — пуансоном, при этом металл заполняет полость матрицы, приобретая её форму и размеры.
Листовая штамповка[править | править код]
Листовой штамповкой получают плоские и пространственные полые детали из заготовок, у которых толщина значительно меньше размеров в плане (лист, лента, полоса). Обычно заготовка деформируется с помощью пуансона и матрицы.
Комбинации[править | править код]
Существуют также процессы, которые являются комбинациями из нескольких методов. Например, метод прокатка-волочение, прокатка-прессование и т.п..
Сущность обработки металлов давлением[править | править код]
Обработка металлов давлением основана на их способности в определенных условиях пластически деформироваться в результате воздействия на деформируемое тело (заготовку) внешних сил.
Если при упругих деформациях деформируемое тело полностью восстанавливает исходную форму и размеры после снятия внешних сил, то при пластических деформациях изменение формы и размеров, вызванное действием внешних сил, сохраняется и после прекращения действия этих сил. Упругая деформация характеризуется смещением атомов относительно друг друга на величину, меньшую межатомных расстояний, и после снятия внешних сил атомы возвращаются в исходное положение. При пластических деформациях атомы смещаются относительно друг друга на величины, больше межатомных расстояний, и после снятия внешних сил не возвращаются в своё исходное положение, а занимают новые положения равновесия.
Холодная штамповка как технология известна достаточно давно. Ещё в конце первого тысячелетия древнерусские мастера стали применять метод холодной штамповки для производства металлической посуды. Саму холодную штамповку отличает достаточно высокое качество получаемых изделий, высокая скорость их изготовления, а также низкая цена на само изделие — разумеется, как уже было отмечено, при массовом их производстве. Холодная штамповка заключается в механическом воздействии штампа в процессе прессования листов металла, итогом которого получаются готовые изделия. Таким образом, сам штамп выступает в роли технологической насадки для прессовального механизма, его можно использовать только для одной операции. Кроме того, операции холодной штамповки легко поддаются автоматизации, в том числе могут проводиться с помощью промышленных роботов, что способно сделать производство методом холодной штамповки ещё более выгодным.
Холодная штамповка технологически подразделяется на два основных вида. Первый — это операции разделительные. Наименование операции зависит от контура разделения. Если разделение происходит по незамкнутому контуру, это операции резки, если по замкнутому контуру: операции пробивки (различные отверстия) и вырубки (различные плоские детали, например, круглой формы в плане). Второй тип операций — операции формоизменения: гибка, вытяжка, формовка, а если исходная заготовка труба — раздача и обжим. Иногда операции двух типов объединяют — например, производят одновременно вытяжку и рубку или гибку и обрезку. В таком случае применяются так называемые комбинированные штампы. Для операций холодной штамповки необходимо использовать металлы и сплавы, которые обладают гибкостью, пластичностью, а также дешевизной.
Вопросы:
1. Сущность обработки металлов давлением, ее основные виды.
2. Холодная и горячая обработка давлением. Обрабатываемые материалы.
3. Преимущества перед литейным производством и обработкой резанием.
1. Обработка давлением основана на способности металлов необратимо изменять свою форму без разрушения под действием внешних сил. Она обеспечивает получение заготовок для производства деталей, а в некоторых случаях и самих деталей требуемых форм и размеров с необходимыми механическими и физическими свойствами.
Обработка давлением – прогрессивный, экономичный и высокопроизводительный способ металлообработки, развивающийся в направлении максимального приближения форм и размеров заготовки к форме и размерам детали, что обеспечивает лучшее использование металла, сокращение трудоёмкости последующей обработки резанием и уменьшением себестоимости продукции.
При производстве металлических изделий широко применяют обработку металлов давлением как в горячем состоянии, так и в холодном. Основными способами обработки металлов давлением являются прокатка, волочение, прессование, ковка и штамповка.
Прокатка – один из важных способов обработки давлением, которым обрабатывается более 75% выплавляемой стали.
Прокатка осуществляется захватом заготовки 2 (рис. 22, а) и деформации ее между вращающимися в разные стороны валками 1 прокатного стана; при этом толщина заготовки уменьшается, а длина и ширина увеличиваются. Валки имеют гладкую поверхность для прокатки листов или вырезанные ручьи, составляющие калибры, для получения круглой или квадратной полосы, рельсов и т. д.
Волочение – процесс, при котором заготовка 2 (рис. 22, б) протягивается на волочильном стане через отверстие инструмента 1, называемого волокой; при этом поперечное сечение заготовки уменьшается; а длина ее увеличивается.
Рис. 22 Схемы основных способов обработки металлов давлением:
а – прокатка; б – волочение; в – прессование; г – ковка; д – объемная штамповка; е – листовая штамповка
Прессование представляет собой выдавливание заготовки 4 (рис. 22, в), помещенной в специальный цилиндр – контейнер 3,через отверстие матрицы 5, удерживаемой матрицедержателем 6;выдавливание производят при помощи пресс – шайбы 2 и пуансона 1. В зависимости от формы и размеров отверстия матрицы получают разнообразные изделия.
Ковка металла заключается в обжатии заготовки 2 (рис. 22, г) между верхним 1 и нижним 3 бойками молота с применением разнообразного инструмента. Свободной ковкой получают поковки различных размеров простой или сложной формы на молотах или прессах.
Штамповка – процесс деформации металла в штампах, форма и размеры внутренней полости которых определяют форму и размеры получаемой поковки. Различают объемную и листовую штамповку.
При объемной штамповке (рис. 22, д) на горячештамповочных молотах и прессах заготовка 2 деформируется в штампе 1. Листовая штамповка (рис. 22, е) осуществляется на холодноштамповочных прессах. При помощи пуансона 1, прижима 2, матрицы 3 листовая заготовка 4 превращается в изделие.
2. Различают горячую и холодную обработки металлов давлением.
Горячая обработка металлов давлением характеризуется явлениями возврата и рекристаллизации, отсутствием упрочнения (наклёпа); механические и физико-химические свойства металла изменяются сравнительно мало. Пластическая деформация не создаёт полосчатости (неравномерности) микроструктуры, но приводит к образованию полосчатости макроструктуры у литых заготовок (слитков) или к изменению направления волокон макроструктуры (прядей неметаллических включений) при обработке металлов давлением заготовок, полученных прокаткой, прессованием и волочением. Полосчатость макроструктуры создаёт анизотропию механических свойств, при которой свойства материала вдоль волокон обычно лучше его свойств в поперечном направлении.
При холодной обработке металлов давлением процесс пластической деформации сопровождается упрочнением, которое изменяет механические и физико-химические характеристики металла, создаёт полосчатость микроструктуры и также изменяет направление волокон макроструктуры. При холодной обработке металлов давлением возникает текстура, создающая анизотропию не только механических, но и физико-химических свойств металла. Используя влияние обработки металлов давлением на свойства металла, можно изготавливать детали с наилучшими свойствами при минимальной массе.
Для получения заготовок обработкой давлением используют различные деформируемые материалы: углеродистые, легированные и высоколегированные стали, жаропрочные сплавы, сплавы на основе алюминия, меди, магния, титана, никеля и др.
Исходными заготовками для обработки металлов давлением являются плоские и круглые слитки разных размеров и массы из стали и цветных сплавов.
До обработки давлением слитки подвергают механической обработке, которая заключается в отрезке прибыльной и донной частей и очистке поверхности от литейных пороков.
Размеры и масса слитков зависят от их назначения. Цилиндрические слитки предназначаются для изготовления прутков, профилей и труб. Их получают главным образом методом непрерывного литья. Плоские слитки применяют для изготовления различных поковок, листов, лент, полос и т. п.
3. Существенные преимущества обработки металлов давлением по сравнению с литейным производством и обработкой резанием – возможность значительного уменьшения отхода металла, а также повышения производительности труда, поскольку в результате однократного приложения усилия можно значительно изменить форму и размеры деформируемой заготовки. Кроме того, пластическая деформация сопровождается изменением физико-механических свойств металла заготовки, что можно использовать для получения деталей с наилучшими эксплуатационными свойствами (прочностью, жесткостью, высокой износостойкостью и т. д.) при наименьшей их массе.
Эти и другие преимущества обработки металлов давлением (отмеченные ниже) способствуют неуклонному росту ее удельного веса в металлообработке. Совершенствование технологических процессов обработки металлов давлением, а также применяемого оборудования позволяет расширять номенклатуру деталей, изготовляемых обработкой давлением, увеличивать диапазон деталей по массе и размерам, а также повышать точность размеров полуфабрикатов, получаемых обработкой металлов давлением.
Один из технологических способов обработки металла — воздействие на него давлением. Особенность данного процесса — меняется внешний вид продукта и его физические свойства. При воздействии давлением увеличивается производительность.
Разные формы пластической деформации используются на современном производстве, для получения как окончательных деталей, так и исходного материала.
Основы процесса обработки давлением металла
Процедура опирается на физические свойства металла безвозвратно изменять свою форму под давлением внешней нагрузки без разрушения. Это основано на механическом свойстве атомов менять свое стабильное состояние на новое при воздействии сил, которые превышают упругость самого металла.
Обработка проводится горячим и холодным способом. При горячем методе температура заготовки выше, чем показатель рекристаллизации.
При холодном методе давление производится при показателях температуры ниже, чем у рекристаллизации.
Применяется несколько процессов воздействия на металл давлением:
- волочение;
- воздействие прессом;
- ковочный процесс;
- прокатный станок;
- объемный вариант штамповки;
- листовой метод;
- комбинированные методы.
Каждый из них отличается многими нюансами.
Прокатка
Для прокатки используется вращательный инструмент — валка. Заготовка втягивается в зазор между валками и приобретает необходимую форму детали. Прокатка имеет несколько разновидностей:
- Продольная: один из самых распространенных методов прокатки.
- Поперечная: заготовка в таком методе не делает поступательных движений.
- Поперечно-винтовая: средний вариант обработки между двумя методами обработки.
Последняя разновидность чаще применяется для изготовления полых заготовок. Прокатка является одним из наиболее широко применяемых методов создания металлических заготовок давлением. При помощи данного процесса получают: балки, рельсы, листы, прутковый материал, трубы.
На производстве несколько валков, соединенных в станину, получается клеть. Всем известный станок проката — это несколько клетей, которые имеют соединения. На прокатных станах используется, и горячий, и холодный метод обработки металла.
В зависимости от готовой продукции, которую выпускает прокатный стан, их делян на: листопрокатные, трубопрокатные, рельсобалочные, а также специальные.
Такие станки подразделяются на то, сколько валков расположено в нем.
Важно знать: Новые и старые способы резки металла
Волочение
В данном метода обработки применяется принудительное пропускание профиля (круглого или фасонного) через фильеру. Ее еще называют волокой. Волока изготавливается из твердых сплавов, а также инструментальной стали и алмазов. Таким образом, изготавливается проволока.
При этом толщина и ширина сечения должны иметь соотношение не больше 20. В таком процессе через несколько фильер протягивается заготовка большого диаметра. Процесс волочения так же разделяется на виды.
- По типу волочения: сухое или мокрое. При мокром волочении используется мыльная эмульсия, а при сухой обработке давлением применяется емкость с мыльным раствором.
- Много- и однониточное волочение. Многониточное волочение допускает протягивание 8 одновременных заготовок.
- По обработке поверхности: чистовое или черновое. Чистовое волочение используется как оканчивающая процедура, а черновой вариант является заготовительным.
- По температурным показателям: холодный и горячий вариант.
- По числу обработки: однократное или многократное. Считается по количеству протягиваний полосы через станок.
При помощи данной технологической процедуры получается проволока до 8 мм в диаметре. Волочение полых конструкций помогает произвести тонкостенные трубы небольшого диаметра.
См.также: Токарные резцы по металлу
Прессование
Это процедура выдавливания давлением металла через отверстие матрицы. В качестве стартового материала для прессования используют заготовки, предварительно обработанные на прокатном станке. Детали получаются самого разного сечения. При помощи прессования в промышленных масштабах изготавливают:
- пруты в диаметре 0.5-20 см;
- трубы в диаметре до 80 см и толщина стенок до 8 мм.
Различия прессования только по методу: прямой и обратный.
При такой процедуре используются в качестве необходимого материала алюминий, медь, магний, титановые сплавы. При прямом варианте следует разогреть заготовку и выложить ее в углубление пресса.
На одной из сторон контейнера расположена матрица с отверстием для выхода материала, которое имеет круглое сечение. С противоположного конца расположен пуансон и пресс-шайба. При таком методе к концу прессования в контейнере остаются пресс-остатки. Они не участвуют в процессе обработки давления металлом.
Обратный вариант обработки заготовок. При таком варианте в контейнер входит полый пуансон, оканчивающийся матрицей. Пуансона давит на приготовленный список, а через матричное отверстие выходит металл.
Отходы по умолчанию меньше, чем при прямом варианте обработки — на 10%. Но из-за сложной конструкции станка, этот метод применяется реже, чем прямой.
Технология процесса имеет следующий алгоритм:
- Подготавливают начальный материал в виде слитка или заготовки. Для этого удаляют все дефекты, разрезают на определенные участки.
- Разогрев материал в электрической или плавильной печи.
- Размещение нагретого материала непосредственно в контейнер.
- Вывод материала через матрицу.
- Доработка металла — резка, избавление от дефектов, правка.
При соблюдении технологического процесса можно добиться 80% выхода готовой продукции.
Ковка
Это один из самых древних методов обработки металла. Первые известные человечеству кузнецы работали еще 6 тысяч лет назад. Сейчас ковка применяется на всех видах производства.
По сути, ковка — это обработка материала нагретого до ковочной температуры. Есть и варианты холодной ковки. На данный момент существует 3 вида ковки:
- Свободная, при которой нет ограничения по формам материала. Сюда же относятся и ручные варианты ковки.
- Машинная — используется с массовой, тяжелой промышленности. Масса механизированного молота до 5 тонн.
- Штамповка — используется для массового производства.
Кузнечный очаг на современном производстве имеет несколько вариаций:
- установленное оборудование;
- мобильные варианты;
- закрытое или открытое;
- топливные;
- с электрическим разогревом;
- жидкостные, твердотопливные и газовые;
- по месту подачи воздуха: через боковые сопла или через центральное.
Наиболее распространённые кузнечные операции:
- Осадочные — уменьшает высоту заготовки и увеличивает ее поперечное сечение.
- Неполная осадка, при которой следует сделать утолщение.
- Протяжка — операция по удлинению заготовки.
- Обкатка — придача заготовке форме цилиндра.
- Образование кольцевой заготовки.
- Выработка широкой заготовки при помощи разгонки.
При ковке важно контролировать температуру, которая напрямую устанавливается в зависимости от твердости материала. Мелкие детали производят ручной поковкой, а средние и крупные — машинной.
Объемная штамповка
Под этой процедурой используется пластическая деформация материала по перераспределению материала на первичном продукте. При этом изменяется простая геометрическая конфигурация на более сложный вариант. Рабочий инструмент — штамп, форму которого получает деталь.
Холодная объемная штамповка проводится без разогрева детали. Этим методом выпускаются надежные детали и механизмы, применяемые в ответственных агрегатах. Штамповка осуществляется без рекристаллизации металла и со значительным упрочнением исходного материала. Но есть и недостаток у данного метода: детали изнашиваются на порядок быстрее.
Горячая объемная штамповка производится при температуре +200°С -1300°С. Начальный материал разрезан на отдельные части, которые по размеру равны будущим готовым деталям. По физическим свойствам эта процедура схожа со свободной ковкой. Отличие только в использовании штампов, которые позволяют достичь сложной конфигурации.
При горячем штамповании используется штамп из матрицы и пуансонов. При этом матрицы статичны, а пуансоны — подвижные. Штампы для горячего штампования бывают:
- закрытыми, когда поверхность разъема находится по периметру поковки;
- открытая, когда поверхность располагается под прямым углом к направлению штамповки.
Открытые штампа более просты в обращении, но могут привести к образованию заусениц на детали. Если используется штамп закрытый, то заусениц не будет, но такой станок не обладает универсальностью.
Листовая штамповка
Это вторичный вариант обработки после прокатки. В качестве исходного материала используются листы, полосы, а также ленты. Процесс проходит на кривошипных или гидравлических прессах. Листовая штамповка предусматривает два вида процедур:
- создающие форму;
- разделяющие.
При использовании листовой штамповки изготавливаются детали, которые имеют высокую точность. Практически все детали микроэлектроники произведены именно таким методом обработки давлением.
Эта процедура давно автоматизирована и штампует детали на скорости до нескольких сотен в минуту. При этом расход материала очень маленький.
Комбинированные методы
Если комбинировать несколько методов обработки металла давлением, то в конечном результате можно получить конечный продукт, который лучше отвечает всем требованиям, необходимым для его эксплуатации.
Одним из комбинированных методов является применение помимо давления еще и сварки. Это позволяет процесс удешевить и упростить, а в итоге получить деталь с заданными характеристиками.
Важно! При использовании данного метода необходимо помнить, что место сварки (шов) может стать слабой частью конструкции.
При совмещении в одном штамповочном переходе обжима и вытяжки можно без проблем уменьшить диаметр конечного продукта. Можно добиться и смены толщины заготовленного продукта в процессе деформации.
Если комбинировать холодный и горячий метод обработки давлением, то легко добиться более высокой прочности за счет холодной деформации.
При влиянии на металл давления используются технологические процессы, основанные на простых законах физики. При этом значительно повышается производительность, а также конечные качества изготавливаемой детали. Есть несколько видов обработки металла давление.
Прежде всего, методы могут быть горячие и холодные, которые зависят от разницы температур между рекристаллизацией и материалом. Это помогает выпустить самые разные детали, по форме, толщине, прочности и эксплуатационным качествам.
При этом самым первым методом воздействия на металл при помощи давления является обыкновенная ковка, которая появилась вместе с выплавкой металла и позволила людям производить надежные орудия труда.