Какие существуют свойство сплавов
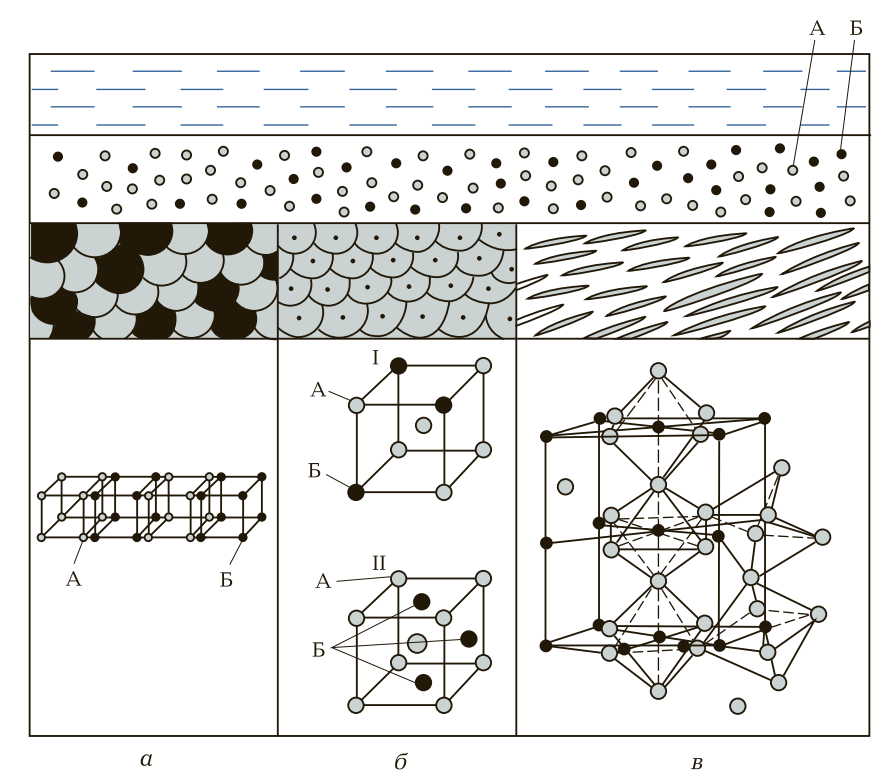
Металлы используются человеком уже много тысячелетий. По именам металлов названы определяющие эпохи развития человечества: Бронзовый Век, Железный Век, Век Чугуна и т.д. Ни одно металлическое изделие из числа окружающих нас не состоит на 100% из железа, меди, золота или другого металла. В любом присутствуют сознательно введенные человеком добавки и попавшие помимо воли человека вредные примеси.
Абсолютно чистый металл можно получить только в космической лаборатории. Все остальные металлы в реальной жизни представляют собой сплавы — твердые соединения двух или более металлов (и неметаллов), полученные целенаправленно в процессе металлургического производства.
Классификация однородности сплавов
Классификация
Металлурги классифицируют сплавы металлов по нескольким критериям:
- метод изготовления:
- литые;
- порошковые;
- технология производства:
- литейные;
- деформируемые;
- порошковые;
- однородность структуры:
- гомогенные;
- гетерогенные;
Виды сплавов по их основе
- вид металла – основы:
- черные (железо);
- цветные (цветные металлы);
- редких металлов (радиоактивные элементы);
- количество компонентов:
- двойные;
- тройные;
- и так далее;
- физико-химические свойства:
- тугоплавкие;
- легкоплавкие;
- высокопрочные;
- жаропрочные;
- твердые;
- антифрикционные;
- коррозионностойкие и др.;
- предназначение:
- конструкционные;
- инструментальные;
- специальные.
Металлы и сплавы на их основе имеют различные физико-химические характеристики.
Металл, имеющий наибольшую массовую долю, называют основой.
Свойства сплавов
Свойства, которыми обладают металлические сплавы, подразделяются на:
- Структурно — нечувствительные. Они обуславливаются свойствами компонентов, и их процентным содержанием. К ним относятся :
- плотность;
- температура плавления;
- тепловые и упругие характеристики;
- коэффициент термического расширения;
- структурно — чувствительные. Определяются свойствами элемента — основы.
- https://youtu.be/qgzo40bfL1o
- Все сплавные материалы в той или иной мере проявляют характерные металлические свойства:
- блеск;
- пластичность;
- теплопроводность;
- электропроводность.
- Кроме того, свойства подразделяют на:
- Химические, определяемые взаимоотношениями материала с химически активными веществами.
- Механические, определяемые взаимодействием с другими физическими телами.
Механические свойства
- Основными характеристиками сплавных материалов, влияющими на их пригодность для применения в той или иной инженерной конструкции, являются:
- Прочность-характеристика силы противостояния механическим нагрузкам и разрушению.
- Твердость-способность к сопротивлению внедрению в материал твердых тел.
- Упругость-возможность восстановить исходную форму тела после деформации, вызванной внешней нагрузкой.
- Пластичность — свойство, обратное упругости. Определяет способность материала к изменению формы тела без его разрушения под приложенной нагрузкой и сохранения этой новой формы.
- Вязкость — способность сопротивляться быстро возрастающим (ударным) нагрузкам
Для количественного выражения этих свойств вводят специальные физические величины и константы, такие, как предел упругости, модуль Гука, коэффициент вязкости и другие.
Основные виды сплавов
Самые многочисленные виды сплавов металлов изготавливаются на основе железа. Это стали, чугуны и ферриты.
Сталь — это вещество на основе железа, содержащее не более 2,4% углерода, применяется для изготовления деталей и корпусов промышленных установок и бытовой техники, водного, наземного и воздушного транспорта, инструментов и приспособлений. Стали отличаются широчайшим диапазоном свойств. Общие из них — прочность и упругость. Индивидуальные характеристики отдельных марок стали определяются составом легирующих присадок, вводимых при выплавке. В качестве присадок используется половина таблицы Менделеева, как металлы , так и неметаллы. Самые распространенные из них — хром, ванадий, никель, бор, марганец, фосфор.
Легированная сталь
Если содержание углерода более 2,4% , такое вещество называют чугуном. Чугуны более хрупкие, чем сталь. Они применяются там, где нужно выдерживать большие статические нагрузки при малых динамических. Чугуны используются при производстве станин больших станков и технологического оборудования, оснований для рабочих столов, при отливке оград, решеток и предметов декора. В XIX и в начале XX века чугун широко применялся в строительных конструкциях. До наших дней в Англии сохранились мосты из чугуна.
Чугунные радиаторы
Вещества с большим содержанием углерода, имеющие выраженные магнитные свойства, называют ферритами. Они используются при производстве трансформаторов и катушек индуктивности.
Сплавы металлов на основе меди, содержащие от 5 до 45% цинка, принято называть латунями. Латунь мало подвержена коррозии и широко применяется как конструкционный материал в машиностроении.
Желтая латунь
Если вместо цинка к меди добавить олово, то получится бронза. Это, пожалуй, первый сплав, сознательно полученный нашими предками несколько тысячелетий назад. Бронза намного прочнее и олова, и меди и уступает по прочности только хорошо выкованной стали.
Вещества на основе свинца широко применяются для пайки проводов и труб, а также в электрохимических изделиях, прежде всего, батарейках и аккумуляторах.
Двухкомпонентные материалы на основе алюминия, в состав которых вводят кремний, магний или медь, отличаются малым удельным весом и высокой обрабатываемостью. Они используются в двигателестроении, аэрокосмической промышленности и производстве электрокомпонентов и бытовой техники.
Цинковые сплавы
Сплавы на основе цинка отличаются низкими температурами плавления, стойкостью к коррозии и отличной обрабатываемостью. Они применяются в машиностроении, производстве вычислительной и бытовой техники, в издательском деле. Хорошие антифрикционные свойства позволяют использовать цинковые сплавы для вкладышей подшипников.
Титан не самый доступный металл, он сложен в производстве и тяжело обрабатывается. Эти недостатки искупаются его уникальными свойствами титановых сплавов: высокой прочностью, малым удельным весом, стойкостью к высоким температурам и агрессивным средам. Эти материалы плохо поддаются механической обработке, но зато их свойства можно улучшить с помощью термической обработки.
Легирование алюминием и небольшими количествами других металлов позволяет повысить прочность и жаростойкость. Для улучшения износостойкости в материал добавляют азот или цементируют его.
Область применения титановых сплавов
Металлические сплавы на основе титана используются в следующих областях:
- аэрокосмическая;
- химическая;
- атомная;
- криогенная;
- судостроительная;
- протезирование.
Алюминиевые сплавы
Если первая половина XX века была веком стали, то вторая по праву назвалась веком алюминия.
Трудно назвать отрасль человеческой жизнедеятельности, в которой бы не встречались изделия или детали из этого легкого металла.
Алюминиевые сплавы подразделяют на:
- Литейные (с кремнием). Применяются для получения обычных отливок.
- Для литья под давлением (с марганцем).
- Увеличенной прочности, обладающие способностью к самозакаливанию (с медью).
Основные преимущества соединений алюминия:
- Доступность.
- Малый удельный вес.
- Долговечность.
- Устойчивость к холоду.
- Хорошая обрабатываемость.
- Электропроводность.
Основным недостатком сплавных материалов является низкая термостойкость. При достижении 175°С происходит резкое ухудшение механических свойств.
Еще одна сфера применения — производство вооружений. Вещества на основе алюминия не искрят при сильном трении и соударениях. Их применяют для выпуска облегченной брони для колесной и летающей военной техники.
Весьма широко применяются алюминиевые сплавные материалы в электротехнике и электронике. Высокая проводимость и очень низкие показатели намагничиваемости делают их идеальными для производства корпусов различных радиотехнических устройств и средств связи, компьютеров и смартфонов.
Слитки из алюминиевых сплавов
Присутствие даже небольшой доли железа существенно повышает прочность материала, но также снижает его коррозионную устойчивость и пластичность. Компромисс по содержанию железа находят в зависимости от требований к материалу. Отрицательное влияние железа скомпенсируют добавлением в состав лигатуры таких металлов, как кобальт, марганец или хром.
Конкурентом алюминиевым сплавам выступают материалы на основе магния, но ввиду более высокой цены их применяют лишь в наиболее ответственных изделиях.
Медные сплавы
Обычно под медными сплавами понимают различные марки латуни. При содержании цинка в 5-45% латунь считается красной (томпак), а при содержании в 20-35%- желтой.
Благодаря отличной обрабатываемости резанием, литьем и штамповкой латунь — идеальный материал для изготовления мелких деталей, требующих высокой точности. Шестеренки многих знаменитых швейцарских хронометров сделаны из латуни.
Малоизвестный сплав меди и кремния называют кремнистой бронзой. Он отличается высокой прочностью. По некоторым источникам, из кремнистой бронзы ковали свои мечи легендарные спартанцы. Если вместо кремния добавить фосфор, то получится отличный материал для производства мембран и листовых пружин.
Это устойчивые к износу и обладающие высокой твердостью материалы на основе железа, к тому же сохраняющие свои свойства при высоких температурах до 1100оС.
В качестве основной присадки применяются карбиды хрома, титана, вольфрама, вспомогательными являются никель, кобальт, рубидий, рутений или молибден.
Основными сферами применения являются:
- Режущий инструмент (фрезы, сверла, метчики, плашки, резцы и т.п.).
- Измерительный инструмент и оборудование (линейки, угольники, штангенциркули рабочие поверхности особой ровности и стабильности).
- Штампы, матрицы и пуансоны.
- Валки прокатных станов и бумагоделательных машин.
- Горное оборудование (дробилки, шарошки, ковши экскаваторов).
- Детали и узлы атомных и химических реакторов.
- Высоконагруженные детали транспортных средств, промышленного оборудования и уникальных строительных конструкций, таки, например, как башня Бурж — Дубай.
Области применения твердых сплавов
Существуют и другие области применения твердосплавных веществ.
На чтение 5 мин.
Металлические изделия и детали используются в разных сферах промышленности. Существует множество видов металлов и каждый из них обладает сильными и слабыми сторонами. При изготовлении деталей для машин, самолётов или промышленного оборудования мастера обращают внимание на характеристики материала. Поэтому требуется знать свойства металлов и сплавов.
Свойства металлов и сплавов
У металлов есть признаки, которые их характеризуют:
- Высокие показатели теплопроводности. Металлические материалы хорошо проводят электричество.
- Блеск на изломе.
- Ковкость.
- Кристаллическая структура.
Не все материалы прочные и обладают высокими показателя износоустойчивости. Это же касается плавления при высоких температурах.
Классификация металлов
Металлы разделяются на две большие группы — черные и цветные. Представители обоих видов различаются не только характеристиками, но и внешним видом.
Черные
Представители этой группы считаются самыми распространёнными и недорогими. В большинстве своем имеют серый или тёмный цвет. Плавятся при высокой температуре, обладают высокой твердостью и большой плотностью. Главный представитель этой группы — железо. Эта группа разделяется на подгруппы:
- Железные — к представителям этой подгруппы относится железо, никель и кобальт.
- Тугоплавкие — сюда входят металлы температура плавления которых начинается с 1600 градусов. Их применяют при создании основ для сплавов.
- Редкоземельные — к ним относятся церий, празеодим и неодим. Обладают низкой прочностью.
Существуют урановые и щелочноземельные металлы, однако они менее популярны.
Цветные
Представители этой группы отличаются яркой окраской, меньшей прочностью, твердостью и температурой плавления (не для всех). Разделяется эта группа на следующие подгруппы:
- Лёгкие — подгруппа, включающая в себя металлы с плотностью до 5000 кг/м3. Это такие материалы, как литий, натрий, калий, магний и другие.
- Тяжёлые — сюда относится серебро, медь, свинец и другие. Плотность превышает 5000 кг/м3.
- Благородные — представили этой подгруппы имеют высокую стоимость и устойчивость к коррозийным процессам. К ним относятся золото, палладий, иридий, платина, серебро и другие.
Выделяются тугоплавкие и легкоплавкие металлы. К тугоплавким относится вольфрам, молибден и ниобий, а к легкоплавким все остальные.
Основные виды сплавов
Человечество знакомо с различными металлическими сплавами. Самыми многочисленными из них являются соединения на основе железа. К ним относятся ферриты, стали и чугун. Ферриты имеют магнитные свойства, в чугуне содержится более 2,4% углерода, а сталь — это материал с высокой прочность и твердостью.
Отдельное внимания требуют металлические сплавы из цветных металлов.
Производство стали
Цинковые сплавы
Соединения металлов, которые плавятся при низких температурах. Смеси на основе цинка устойчивы к воздействию коррозийных процессов. Легко обрабатываются.
Алюминиевые сплавы
Популярность алюминий и сплавы на его основе получили во второй половине 20 века. Этот материал обладает такими преимуществами:
- Устойчивость к низким температурам.
- Электропроводность.
- Малый вес заготовок в сравнении с другими металлами.
- Износоустойчивость.
Однако нельзя забывать про то, что алюминий плавится при низких температурах. При температуре около 200 градусов характеристики ухудшаются.
Алюминий применяется при изготовлении комплектующих к машинам, производстве деталей для самолётов, составляющих промышленного оборудования, посуды, инструментов. Не многие знают, что алюминий популярен в сфере производства оружия. Связано это с тем, что детали из алюминия не искрят при сильном трении.
Чтобы увеличить прочность детали, алюминий смешивают с медью. Чтобы заготовка выдерживала давление — с марганцем. Кремний добавляют, чтобы получить обычную отливку.
Медные сплавы
Сплавы на основе меди — марки латуни. Из этого материала изготавливаются детали высокой точности, так как латунь легко обрабатывать. В составе сплава может содержаться до 45% цинка.
Свойства сплавов
Чтобы изготавливать детали и конструкции, нужно знать основные свойства металлов и сплавов. При неправильной обработке готовая деталь может быстро выйти из строя и разрушить оборудование.
Двигатель внутреннего сгорания
Физические свойства
Сюда относятся визуальные параметры и характеристики материала, изменяющиеся при обработке:
- Теплопроводность. От этого зависит насколько поверхность будет передавать тепло при нагревании.
- Плотность. По этому параметру определяется количество материла, которое содержится в единице объёма.
- Электропроводность. Возможность металла проводить электрический ток. Этот параметр называется электрическое сопротивление.
- Цвет. Этот визуальный показатель меняется под воздействием температур.
- Прочность. Возможность материала сохранять структуру при обработке. Сюда же относится твердость. Эти показатели относятся и к механическим свойствам.
- Восприимчивость к действию магнитов. Это возможность материала проводить через себя магнитные лучи.
Физические основы позволяют определить в какой сфере будет использоваться материал.
Химические свойства
Сюда относятся возможности материала противостоять воздействию химических веществ:
- Устойчивость к коррозийным процессам. Этот показатель определяет на сколько материал защищён от воздействия воды.
- Растворимость. Устойчивость металла к воздействию растворителей — кислотам или щелочным составам.
- Окисляемость. Параметр указывает на выделение оксидов металлом при его взаимодействии с кислородом.
Обуславливаются эти характеристики химическим составом материала.
Механические свойства
Механические свойства металлов и сплавов отвечают за целостность структуры материала:
- прочность;
- твердость;
- пластичность;
- вязкость;
- хрупкость;
- устойчивость к механическим нагрузкам.
Технологические свойства
Технологические свойства определяют способность металла или сплава изменяться при обработке:
- Ковкость. Обработка заготовки давлением. Материал не разрушается. Структура изменяется.
- Свариваемость. Восприимчивость детали к работе сварочным оборудованием.
- Усадка. Происходит этот процесс при охлаждении заготовки после её разогрева.
- Обработка режущим инструментом.
- Ликвация (затвердевание жидкого металла при понижении температуры).
Основной способ обработки металлических деталей — нагревание.
Свойства металлов и сплавов отвечают за то, как себя будет вести готовое изделие при эксплуатации. При обработке материалов также важно знать его характеристики.
Из-за низких механических свойств чистые металлы как конструкционные материалы в машиностроении находят ограниченное применение по сравнению со сплавами.
Сплав — это конструкционный материал, полученный путем сплавления нескольких химических элементов (металлов и неметаллов) и обладающий свойствами, присущими основному сплавляемому элементу.
Металлический сплав может быть получен не только сплавлением химических элементов, но и такими способами, как спекание, электролиз, диффузия, плазменное напыление, возгонка и др. Конструкционный материал, полученный не сплавлением, называется псевдосплавом. Если сплав имеет в своем составе 50 % металла и более, то он называется металлическим сплавом.
Металлический сплав имеет более высокие механические и технологические свойства по сравнению с неметаллическим сплавом. Химические элементы, образующие сплав, называются компонентами.
По своему составу сплавы могут быть двухкомпонентными (металл + металл, металл + неметалл), трех- и более компонентными. Внутреннее строение сплавов определяется формой связи между компонентами.
Двухкомпонентные сплавы при нагревании (охлаждении) в силу особенностей взаимодействия друг с другом ведут себя неадекватно и, в связи с этим, имеют различное физическое строение и свойства.
К промышленным сплавам, которые находят широкое применение, относятся:
- чугун и сталь — сплавы железа с углеродом;
- латунь — сплав меди с цинком;
- бронза — сплав меди с оловом и др.
Сплавы имеют атомно-кристаллическое строение, обладают аллотропией (полиморфизмом) и, по сравнению с чистыми металлами, более высокими механическими и технологическими свойствами.
Форма металлической связи сплавляемых химических элементов влияет на образование структуры сплава, их атомно-кристаллическую решетку.
Фазы. Сплавам, так же как и чистым металлам, характерно атомно-кристаллическое строение. Сплав в твердом состоянии может иметь различную связь атомно-кристаллических решеток. Жидкое или твердое состояние химических компонентов, образующих сплав при определенной температуре и давлении, называется системой.
Однородная часть системы, отделенная от других частей условной границей (линией), называется фазой.
Жидкая фаза характеризуется тем, что атомные кристаллические решетки сплавляемых компонентов распадаются и компоненты растворяются друг в друге или не растворяются и присутствуют в сплаве самостоятельно. Эта закономерность присуща многим сплавам.
Твердая фаза — это однородная часть сплава с определенными атомно-кристаллическим строением и массовой долей сплавляемых компонентов. Атомные решетки сплавляемых компонентов взаимодействуют в строго определенном порядке. Атомные решетки химических элементов, образующих сплав в твердом состоянии, образуют мелкие кристаллы — структуры.
В зависимости от внутреннего строения сплавов и металлической или химической связи между сплавляемыми элементами сплавы подразделяются на две группы:
- однородные сплавы;
- неоднородные сплавы.
Однородные сплавы имеют общие атомные кристаллические решетки, в которые входят атомы сплавляемых компонентов.
Неоднородные сплавы имеют самостоятельные кристаллические решетки сплавляемых компонентов.
По характеру взаимодействия сплавляемых компонентов в твердой фазе различают механические смеси, твердые растворы и химические соединения.
Механическая смесь сплавляемых компонентов А и Б (рис. 1, а) образуется тогда, когда атомные кристаллические решетки сохраняются и не вступают в химическую реакцию с образованием какого-либо нового соединения. Связь между атомными решетками осуществляется за счет металлической связи. Механическая смесь сплава будет неоднородного типа, т. е. сплавляемые компоненты А и Б в сплаве будут самостоятельными и чередоваться между собой в зависимости от их соотношения.
Рис. 1. Схематическое изображение структуры сплава: а — механическая смесь; б — твердый раствор (I — раствор замещения; II — раствор внедрения); в — химическое соединение; А, Б — сплавляемые компоненты
Свойства механической смеси зависят от свойств сплавляемых компонентов А и Б. Как правило, эти микроструктуры имеют относительно высокую твердость, прочность, ударную вязкость, хорошо обрабатываются резанием.
Твердые растворы в зависимости от взаимодействия атомов подразделяются на твердые растворы внедрения и твердые растворы замещения (рис. 1, б ).
На рис. 1, б, I показана атомно-кристаллическая решетка твердого раствора замещения. Атомно-кристаллическая решетка основного компонента А в форме объемно-центрированного куба (девять атомов) сохранилась, но три атома этого компонента замещены атомами сплавляемого компонента Б.
На рис. 1, б, II показана атомно-кристаллическая решетка твердого раствора внедрения. При этом виде образования сплава атомно-кристаллическая решетка основного компонента А сохраняется. Атомно-кристаллическая решетка сплавляемого компонента Б разрушается, и его отдельные атомы внедряются в пространство атомно-кристаллической решетки основного компонента А. Таким образом, в атомно-кристаллической решетке твердого раствора внедрения девять атомов, как в основном компоненте А, плюс два-три атома компонента Б.
Твердые растворы по своим свойствам наиболее близки к свойствам основного компонента. Они имеют низкую твердость, высокую плотность, ударную вязкость, прочность, хорошо деформируются в холодном и горячем состоянии. Микроструктура большинства конструкционных и инструментальных сталей представляет собой твердые растворы внедрения и замещения.
Химические соединения сплава образуются тогда, когда атомно-кристаллические решетки сплавляемых компонентов А и Б распадаются. Отдельные атомы этих компонентов образуют новые атомные решетки, которые по своему типу, форме и числу атомов отличаются от атомно-кристаллических решеток сплавляемых компонентов.
Химические соединения в сплаве образуются при строго определенном массовом соотношении сплавляемых компонентов А и Б. Например, химическое соединение углерода с железом образуется при массовой доле углерода, равной 6,67 %.
Свойства химических соединений также резко отличаются от свойств сплавляемых компонентов. Химические соединения, как правило, очень твердые, хрупкие, тугоплавкие, имеют мелкозернистую или игольчатую микроструктуру. На рис. 1, в показана атомно-кристаллическая ячейка химического соединения углерода с железом. Это сложная ромбическая пространственная атомно-кристаллическая решетка, состоящая из атомов железа и атомов углерода (компонентов А и Б).
В практике чаще всего в сплаве наблюдается смесь нескольких соединений (микроструктур), например механическая смесь химического соединения и твердого раствора или механическая смесь двух твердых растворов.
Диаграммы состояния двухкомпонентных сплавов. Любое изменение химического состава сплава влечет за собой изменение физических параметров: температуры, давления и структуры. Изменение этих параметров на границах фаз происходит скачкообразно или замедленно.
В практике металловедения для определения температур, давления, структуры и взаимодействия сплавляемых компонентов применяют графики — диаграммы состояния сплавов. Для этого нагревают (охлаждают) сплав в закрытом тигле с помощью термопары, по прибору наблюдают поведение этого сплава и по наблюдениям строят соответствующие графики.
На диаграммах состояния отображаются только условия, когда сплав имеет постоянные параметры, — равновесие, поэтому в научной литературе диаграммы состояния также называют диаграммами равновесия. В связи с тем что сплавляемые компоненты (металлы и неметаллы) обладают аллотропией, при нагревании (охлаждении) в сплавах происходят аллотропные изменения. Аллотропные изменения можно наблюдать при лабораторных исследованиях с помощью термического метода, а иногда визуально (цвет сплава становится ярче или, наоборот, тускнеет, или длительное время остается постоянным).
Любое изменение в металле при нагревании (охлаждении) характеризуется определенной температурой, которая называется критической температурой. Критические температуры на прямой отражаются соответствующими точками, которые называются критическими точками. Если рассматривать любой металл или сплав в одном измерении (температура нагрева), то графическая характеристика будет отображена в виде вертикальной прямой, на которой указывают критические температуры (точки). Если состояние металла или сплава рассматривать в двух измерениях (температура нагрева (охлаждения) и время нагрева (охлаждения), то график будет изображен в двух координатах (ось ординат и ось абсцисс).
Для примера рассмотрим состояние чистого железа при нагревании и охлаждении. На рис. 2 приведены критические температуры чистого железа при нагревании (охлаждении). Железо имеет следующие критические точки (температуры): 768; 910; 1 392 и 1 539 °С. При температуре 910 °С Fе-α (α-железо) переходит в Fе-β (β-железо). При температуре 1 392 °С Fе-β переходит в Fe-γ (γ-железо). При температуре 1 539 °С Fe-γ начинает медленно расплавляться с поглощением энергии (температуры).
При всех критических температурах на диаграммах показаны задержки перекристаллизации (горизонтальные участки). При охлаждении железа процесс перекристаллизации происходит в обратном порядке.
Для двухкомпонентных сплавов диаграмма состояния — это графическое изображение состояния сплавов в двух измерениях: температура нагрева (охлаждения) и химический состав сплава (концентрация).
Рис. 2. Кривые нагрева и охлаждения железа: t — температура; τ — время
Температуру нагрева (охлаждения) откладывают по оси ординат, по оси абсцисс откладывают массовую долю сплавляемых компонентов (концентрация).
Для примера рассмотрим диаграмму состояния двухкомпонентного сплава свинец — сурьма (рис. 3). На оси абсцисс слева берем 100 % свинца (Pb), справа — 100 % сурьмы (Sb). Свинец и сурьма в жидком состоянии неограниченно растворяются друг в друге, в твердом состоянии — образуют механическую смесь сплавляемых компонентов.
При нагревании (охлаждении) сплава от твердого состояния до температуры плавления (а при охлаждении от жидкого состояния до температуры затвердевания) в сплаве происходит образование механических смесей (эвтектика) и расплавление при различных температурах.
Возьмем чистый свинец. При нормальной температуре и до температуры 245 °С в свинце никаких изменений внутреннего строения не происходит, и свинец будет иметь структуру Рb-α (α-свинец). При температуре 245 °С Рb-α перестраивается в Рb-β (β-свинец). Эта структура остается до температуры 327 °С.
При температуре 327 °С свинец начинает расплавляться. При расплавлении за счет поглощения энергии (температуры) температура свинца остается постоянной — 327 °С. При охлаждении свинца процесс происходит в обратном порядке.
Рис. 3. Кривые охлаждения и структуры (а, б, в, д, е), диаграмма состояния (г) сплавов свинец—сурьма: 1 — температура ликвидуса; 2 — температура солидуса; АВС — линия ликвидуса; DBE — линия солидуса; Ж — жидкость; Эвт. — эвтектика
При нагревании сурьмы до температуры 245 °С никаких изменений в металле не происходит. Структура сурьмы будет Sb-α (α-сурьма). При температуре 245 °С Sb-α переходит в Sb-β. При температуре 631°С сурьма начинает расплавляться. В связи с тем что при расплавлении происходит большое поглощение теплоты, температура расплавления сурьмы на 8 … 10 °С будет ниже. При охлаждении процесс идет в обратном порядке. Далее рассмотрим поведение типовых сплавов свинца и сурьмы: 95 % Рb + 5 % Sb; 87 % Рb + 13 % Sb; 60 % Рb + 40 % Sb. Для составления диаграммы состояния двухкомпонентного сплава свинец — сурьма строим кривые нагрева (охлаждения).
При нагревании (охлаждении) 100 % Pb (рис. 3, а) при температуре 327 °С на графике будет горизонтальный участок. При нагревании (охлаждении) сплава 95 % Рb + 5 % Sb (рис. 3, б) при температуре 245 °С на графике будет горизонтальный участок. Далее при нагревании (охлаждении) при температуре 300 °С будет перегиб кривой, при этой температуре сплав начнет расплавляться (при нагревании) или кристаллизоваться (при охлаждении). При нагревании (охлаждении) сплава 87 % Рb + 13 % Sb (рис. 3, в) при температуре 245 °С также будет горизонтальный участок. При этой температуре сплав начинает плавиться и заканчивает расплавление при температуре 245 °С.
При нагревании (охлаждении) сплава 60 % Рb + 40 % Sb (рис. 3, д) до температуры 245 °С в структуре сплава никаких изменений не происходит. При температуре 245 °С свинец начинает расплавляться — на графике будет горизонтальный участок. При дальнейшем нагревании (охлаждении) при температуре 350 °С сплав расплавляется (при нагревании) или начинает кристаллизоваться (при охлаждении).
При нагревании (охлаждении) 100 % сурьмы (рис. 3, е) до температуры 631 °С сплав будет иметь твердую фазу, и при температуре 631 °С на графике будет горизонтальный участок, сурьма начинает расплавляться. За счет поглощения энергии расплавление сурьмы происходит при температуре несколько ниже 631 °С.
Для наглядного изображения характеристики сплава свинец — сурьма строим следующий график. На оси ординат откладываем температуры нагрева (охлаждения) от нормальной температуры. На этой оси будем откладывать критические точки для 100 % свинца. На оси абсцисс откладываем массовую долю в сплаве свинца и сурьмы. Справа проводим ось температур для 100 % содержания сурьмы. Далее на оси ординат проектируем критические точки, полученные в результате нагрева рассмотренных ранее сплавов.
Как видим из графиков, первое фазовое изменение сплавов происходит при температуре 245 °С. Проводим горизонтальную прямую DE, соответствующую этой температуре. На оси температур свинца проектируем точку, соответствующую температуре 327 °С — температуре плавления чистого свинца. Полученную точку обозначим буквой А.
На оси температур сурьмы проектируем точку, соответствующую 631 °С — температуре плавления сурьмы. Полученную точку обозначим буквой С. На оси абсцисс из точки, соответствующей 87 % Рb и 13 % Sb, восстанавливаем перпендикуляр (пунктиром) до горизонтальной прямой DE (температура расплавления данного сплава). Точку А (критическую температуру 327 °С) на оси ординат соединяем с критической точкой, лежащей на горизонтальной прямой, соответствующей температуре плавления данного сплава (87 % Рb + 13 % Sb). Полученную точку обозначим буквой В.
На оси абсцисс из точки, соответствующей 95 % Рb и 5 % Sb, восстанавливаем перпендикуляр до пересечения с отрезком АВ. В данной точке имеем критическую температуру 300 °С — температуру плавления (затвердевания) сплава 95 % Pb + 5 % Sb.
На оси абсцисс из точки, соответствующей 60 % Рb и 40 % Sb, восстанавливаем перпендикуляр до пересечения с отрезком ВС, получаем точку, которая соответствует критической температуре 350 °С — плавления (затвердевания) сплава 60 % Pb + 40 % Sb.
Таким образом, мы получили диаграмму состояния двухкомпонентного сплава свинец — сурьма. Все сплавы Рb— Sb независимо от массовой доли компонентов до температуры 245 °C имеют твердую фазу — механическая смесь. Сплав по линии DВЕ начинает медленно расплавляться при нагревании и затвердевает при охлаждении. Эту линию называют линией солидуса (от лат. solidus — твердый).
По линии АВС сплавы расплавляются при нагревании, при охлаждении начинают медленно кристаллизоваться. Эта линия называется линией ликвидуса (от лат. liquidus — жидкий). Между линиями DBE и линией АВС сплавы находятся в полужидком состоянии. Сплав с 87 % Рb и 13 % Sb имеет самую низкую температуру плавления (затвердевания). Этот сплав, так же как и чистые металлы, плавится при одной температуре. Такие сплавы получили название эвтектических сплавов.
Эвтектика — мелкодисперсная механическая смесь двух компонентов, образовавшаяся при температуре плавления (кристаллизации), значительно ниже температуры плавления сплавляемых компонентов в процессе затвердевания. Левее эвтектики сплавы называются доэвтектическими, правее — заэвтектическими.
Рассмотрим фазовые состояния сплава свинец — сурьма. Выше линии АВС сплав находится в жидком состоянии (жидкая фаза), между линией АВ и DB — в полужидком (Pb + жидкость). Ниже лини DB сплав состоит из механической смеси свинца и эвтектики. Между линиями ВС и ВЕ сплав будет иметь полужидкую фазу и кристаллы сурьмы. Ниже линии ВЕ сплав будет состоять из механической смеси (эвтектика и сурьма).
Диаграмма состояния сплава Pb — Sb относится к типу диаграмм, в которых сплавляемые компоненты неограниченно растворяются в жидком состоянии и не растворяются в твердом состоянии, образуя механические смеси (эвтектика).
Анализируя диаграмму состояния сплавов, можно изучить следующие характеристики: температуру плавления (кристаллизации), виды структур сплавов, способность образовывать ликвацию, режимы термообработки и обработки давлением. При изучен