Какие химические примеси в металле сварного шва снижают его пластические свойства
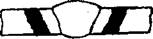
В данной статье речь пойдет о вредных примесях при сварке (вкратце).
СЕРА.
Сера-всегда вредная примесь при сварке металлов, так как она образует относительно легкоплавкие эвтектики Me-MeS, что создает возможность образования «горячих» или «кристаллизационных» трещин в металле шва (визуально на поверхности их порой довольно сложно определить, даже по наличию окалины и цветов побежалости).
Её содержание в металле шва и сварочных материалах всегда следует жестко лимитировать. Снижение вредного влияния серы достигается ее переводом из сульфидов железа в сульфиды с белее высокой температурой плавления (в сварочную ванную добавляют марганец в достаточных количествах в виде порошка, который обычно содержится в обмазке электродов, либо содержится в самой проволоке в виде соединения, либо добавляют кальций, который также содержится в обмазке электрода). Общее снижение содержания серы в металле при сварке возможно также при сильно основных шлаках (плавиковый шпат, который содержится в обмазке электрода, и мрамор).
ФОСФОР.
Фосфор-почти всегда вредная примесь в металлах, снижающая их пластичность. Так, при кристаллизации стали фосфор образует ряд соединений с железом, отличающихся своей хрупкостью, кристаллы которых могут стать «зародышами» «холодных» трещин. Содержание фосфора в металле шва при дуговой сварке понизить практически не удается, так как он удаляется в окислительных шлаках, а сварочные шлаки, в основном — восстановительные. При сварке медных сплавов фосфор не представляет собой вредную примесь, так как он способен раскислять металл, образуя летучий оксид P2O5.
КИСЛОРОД.
Кислород- вредная примесь в металле при сварке, снижающая пластические свойства металла, поэтому при всех видах сварки предусматривается процесс раскисления металла шва до допустимой нормы. При сварке металлов высокой активности (алюминий, титан и прочее) следует создавать бескислородную атмосферу — аргон, гелий, вакуум, галидные флюсы, так как раскислителей для таких металлов подобрать сложно.
АЗОТ.
Азот поглощается металлом сварочной ванны из атмосфера дугового промежутка (столб дуги), в котором он находится в основном в атомарном состоянии и частично в ионизированном. Растворимость азота в жидком металле выше, чем в твердом, и в процессе кристаллизации металла шва он может выделяться в газообразном состоянии, образуя поры. При кристаллизации металла сварочной ванны азот образует почти со всеми металлами соединения — нитриды различной степени устойчивости. Нитриды железа образуют очень хрупки игольчатые кристаллы, разрушение которых приводит к зарождению «холодных» трещин (по-другому — замедленное разрушение, не так как в случае с фосфором «НЕ ПУТАТЬ»).
ВОДОРОД.
Пожалуй самый опасный и «коварный» элемент. Водород при сварке — всегда вредная примесь (так как очень сильно охрупчивает металл). Источники водорода при сварке:
1. Водород, поглощенный металлом из атмосферы дугового разряда
2. Водород, растворенный в основном металле.
Водород, поглощенный из атмосферы дугового разряда, в которой он находится в атомарном и в ионизированном состояниях, при кристаллизации резко снижает свою растворимость и, выделяясь из металла, вызывает возникновение пор и трещин.
Водород, содержащийся в основном металле, может находиться в состоянии твердого раствора внедрения — диффузионно-подвижный водород, а также находиться в связанном состоянии — гидридный водород. Водород в молекулярном состоянии находится в микронесплошностях металла.
К основным путям снижения водорода в зоне сварки относят: частичное окисление атмосферы в сварочной зоне (сварка в СО2, использование электродов с руднокислыми покрытиями), введения во флюсы и покрытия электродов фторидов и хлоридов (плавиковый шпат и соли), просушка сварочных материалов (прокалка электродов, проволоки, флюсов, просушка защитных газов и т.д.)
Это были основные вредные примеси при сварке.
В процессе газовой сварки расплавленный металл сварочной ванны взаимодействует со сварочным пламенем. Это взаимодействие определяется свойствами свариваемого металла и составом сварочного пламени. Сваривают восстановительной зоной пламени, состоящей в основном из оксида углерода и водорода. Сварочная ванна характеризуется малым объемом расплавленного металла, высокой температурой в месте сварки и большой скоростью расплавления и кристаллизации металла.
Расплавленный металл ванны вступает во взаимодействие с газами сварочного пламени, в результате чего происходят реакции окисления и восстановления. Взаимодействие газов с различными металлами различно. Наиболее легко окисляются металлы, обладающие большим сродством к кислороду. Окисление расплавленного металла происходит как за счет оксидов, находящихся на поверхности свариваемого металла и присадочной проволоки, так и за счет кислорода окружающего воздуха. С увеличением содержания кислорода в свариваемом металле ухудшаются механические свойства сварного соединения. Поэтому при газовой сварке для большинства металлов и сплавов для устранения окислительных процессов в присадочные материалы и флюсы вводят специальные раскислители.
Раскислители
вещества, которые имеют большее сродство к кислороду, чем металл шва.
При газовой сварке стали раскисляющее действие оказывают углерод, оксид углерода и водорода, образующиеся при горении газовой смеси, подаваемой в сварочную горелку. Поэтому углеродистые стали можно сваривать без флюсов. Таким образом углерод (С), кремний (Si) и марганец (Мn) выполняют функции раскислители. Образующийся в процессе реакции оксид углерода вызывает кипение и разбрызгивание металла. Кипение сварочной ванны до начала кристаллизации способствует удалению посторонних металлических включений. Если металл кипит во время кристаллизации шва, то образующиеся пузыри оксида углерода не успевают выделяться и остаются в шве в виде газовых пор. Для уменьшения образования оксида углерода в сварочную ванну вводят раскислители (Мn и Si). На процесс окисления при сварке металлов большое влияние оказывает состав сварочного пламени. Образующиеся в процессе реакций оксиды кремния и марганца не растворяются в металле, всплывают на поверхность жидкого металла и переходят в шлаки. В жидком металле шва находится много разнородных оксидов, между которыми происходят химические реакции. В результате этих реакций образуются соединения с более низкой температурой плавления, чем сами оксиды, что облегчает удаление оксидов из расплавленного металла в виде шлака.
При газовой сварке алюминия, латуни и других металлов вводят флюсы, в состав которых входят компоненты, способствующие образованию легкоплавких соединений. Раскисление сварочной ванны частично осуществляется углеродом, оксидом углерода и водородом, имеющимися в сварочном пламени. При этом сварочное пламя не только восстанавливает оксиды но и защищает расплавленный металл от кислорода и азота воздуха. Нормальное ацетиленокислородное пламя в средней (восстановительной) зоне содержит 60% оксида углерода, 20% молекулярного и 20% атомарного водорода. Восстановителем железа из закиси железа в основном является атомарный водород. Он растворяется в расплавленном металле, а с понижением температуры стремится выделиться из сварочной ванны. Если затвердевание происходит достаточно быстро, то водород в виде газовых пузырей может остаться в сварном шве. Следовательно, водород, с одной стороны, защищает расплавленный металл от окисления, а также восстанавливает его из оксидов, а с другой стороны, может явиться причиной образования пористости и трещин.
Рисунок 1 — Схема химической неоднородности по слоям кристаллизации в сварных швах
Процесс газовой сварки характеризуется относительно медленным охлаждением металла, поэтому водород и другие газы успевают выделиться из сварочной ванны и металл шва получается без пор. Поступающий в сварочную ванну азот воздуха снижает пластические свойства свариваемого металла, а также вызывает пористость в металле шва.
Кристаллизация металла шва
Процесс образования сварного соединения начинается с нагрева и расплавления основного и присадочного металлов.
Кристаллизация
процесс образования зерен из расплавленного металла при переходе его из жидкого состояния в твердое
Процесс кристаллизации сварных швов отличается от кристаллизации слитков высокими скоростями. Различают первичную и вторичную кристаллизации. Первичная кристаллизация осуществляется при высоких скоростях охлаждения, вторичная начинается с распада первичной в результате структурных превращений и заканчивается при низких температурах. Как и во всех случаях сварки плавлением кристаллизация металла шва осуществляется на зернах основного металла. Более медленный прогрев при газовой сварке основного металла приводит к большему росту зерен нерасплавленных кромок металла, а следовательно, и уменьшению количества центров кристаллизации формирующегося шва. Процесс кристаллизации сварных швов осуществляется прерывисто, этим и объясняется появление кристаллизационных слоев. Чем сильнее тепло-отвод и меньше объем жидкого металла, тем тоньше кристаллизационный слой. Кристаллизационные слои можно рассмотреть на специально изготовленных макрошлифах в любом сечении шва. Первый участок возникает в результате кристаллизации тонкой прослойки жидкого металла, примыкающей к оплавленной поверхности. Второй участок кристаллизуется из жидкого металла исходного материала.
СВАРОЧНЫЕ РАБОТЫ
На качественные показатели сварных соединений накладывают отпечаток множество факторов, к которым относятся свариваемость металлов, их чувствительность к термическим воздействиям, окисляемость и т. д. Поэтому для соответствия сварных соединений тем или иным эксплуатационным условиям следует эти критерии учитывать.
Свариваемость металлов определяет способность отдельных металлов или их сплавов образовывать при соответствующей технологической обработке соединения, отвечающие заданным параметрам. На этот показатель оказывают влияние физические и химические свойства металлов, строение их кристаллической решетки, нали — чиє примесей, степень легирования и т. д. Свариваемость может быть физическая в технологическая.
Под физической свариваемостью понимают свойство материала или его составов создавать монолитное соединение с устойчивой химической связью. Физической свариваемостью обладают практически все чистые металлы, их технические сплавы и ряд сочетаний металлов с неметаллами. К технологической свариваемости материала относят его реакцию на сварочный процесс и способность создать соединение, удовлетворяющее заданные параметры.
При определении критериев свариваемости металлов и их сплавов ориентируются на следующие их свойства:
— Чувствительность металла к тепловому воздействию, которое создается при сварке;
— склонность металла к росту зерна с сохранением пластических и прочностных свойств, структурным и фазовым изменениям в зоне термического воздействия;
— химическая активность металла, влияющая на его окисляемость при термическом воздействия сварочного процесса;
— сопротивляемость металла к образованию пор и трещин в холодном и горячем состоянии.
Большое влияние на качество сталей оказывает так называемая их раскисляемость, которая характеризуется содержанием марганца, кремния и некоторых других элементов и равномерностью их распределения. По этому параметру различают три вида сталей: кипящая — «кп», полуспокойная — «пс» и спокойная — «сп».
Кипящая сталь отличается большой неравномерностью распределения вредных примесей (особенно серы и фосфора) по толщине проката и получается при неполном раскислении металла марганцем. Характерной особенностью этого вида сталей является склонность к старению и образование кристаллизационных трещин в шве и около — шовной зоне, что приводит к переходу в хрупкое состояние при отрицательных температурах.
Спокойная сталь получается при равномерном распределении примесей, поэтому она менее склонна к старению и меньше реагирует на сварочный нагрев.
Полуспокойная сталь занимает промежуточное значение между кипящей и спокойной.’
Все эти свойства учитывают при выборе технологических приемов сварки, способов формирования сварочного шва, параметров теплового воздействия и т. д.
В качестве примера приведем свариваемость сталей, как наиболее распространенных конструктивных материалов.
Для сварных конструкций лучше всего использовать низкоуглеродистые и низколегированные стали, обладающие высокой степенью свариваемости.
Наибольшее влияние на качество сварного соединения оказывает углерод. Увеличение содержания углерода и ряда других легирующих элементов снижает свариваемость сталей, ухудшая качество шва.
Сварные соединения высокоуглеродистых и высоколегированных сталей отличаются повышенным содержанием трещин и выполняются по специальной технологии.
Классификация сталей по свариваемости приведена в табл.1.
Таблица 1
Классификация сталей по свариваемости
Группа по свариваемости | Марки стали | |
Углеродистая | Констру киионная легированная | |
1. Хорошая | Ст. 1; Ст.2; Ст. З; Ст.4; 0,8; сталь І0, 15, 20, 25;12кп, 15кп, 16кл, 20кп | 15Г; 20Г; 15Х; 15ХА; 20Х; 15ХМ; 14ХГ. С, 10ХСМД; 10ХГСМД;15ХСМД |
2. Удовлетворительная | Сг5; сталь 30, 35 | (2ХМ2; 12ХНЗА; [4Х2МП; 10Г2МП; 20ХНЗА; 20ХЙ; 20ХГСА; 25ХГСА; 30Х; 30 М |
3 Ограниченная | Стб; сталь40, 45, 50 | 35Г; 40Г; 45Г; 40Г2; 35Х; 40Х; 45Х; 40ХН;40; 40ХМФА; 30ХГС; 30ХГС; 30ХГСМ; 35ХМ; 20Х2Н4А; 4ХС; 12Х2Н4МА |
4. Плохая | Сталь 65, 70, 75, 80, 85, У7, У8, У9, У10, У11, У12 | 50Г; 50Г2; 50Х; 50ХН; 45ХНЗМФА; бХс; 7X3; 9ХС; 8X3; 5ХНТ; 5ХНВ |
Примечание: Стали, относящиеся к хорошим, имеют содержание углерода менее 0,25%. Они хорошо свариваются без образования закалочных структур и трещин в широком диапазоне режимов сварки.
Стали, относящиеся к удовлетворительным, имеют содержание углерода от 0,25 до 0,35%. Они мало склонны к образованию трещин и при правильно подобранных режимах сварки дают качественный шов.
Для улучшения качества сварки часто применяют подогрев.
Ограниченно свариваемые стали имеют содержание углерода от 0,36 до 0,45% и склонны к образованию трещин. Сварка требует обязательного подогрева.
Плохо свариваемые стали содержат углерод в количестве более 0,45%. При их сварке требуются специальные технологические процессы.
Легирование стали одним или несколькими легирующими элементами придает ей определенные физико-механические свойства. Как правило, повышение уровня легирования и прочности стали приводит к ухудшению ее свариваемости и первостепенная роль в этом принадлежит углероду.
Низколегированные стали хорошо свариваются всеми способами плавления. Получение же при сварке равнопрочного сварного соединения, особенно у термоупрочненных сталей, вызывает определенные трудности. В зонах, удаленных от высокотемпературной области, возникает холодная пластическая деформация. При наложении последующих швов эти зоны становятся участками деформационного старения. Это в конечном итоге приводит к снижению пластических и повышению прочностных свойств металла и соответственно к появлению холодных трещин. В среднелегированных сталях увеличивается склонность к закалке, в связи с чем такие стали имеют высокую чувствительность к термическому циклу сварки. Их около — шовная зона оказывается резко закаленной, а следовательно, и непластичной при всех режимах сварки, обеспечивающих удовлетворительное формирование шва. Поэтому с целью снижения скорости охлаждения околошовной зоны при сварке этих сталей необходим предварительный подогрев свариваемого изделия.
При сварке высоколегированных хромистых 08X13, 08X17Т и некоторых других сталей существуют отличительные особенности:
— -высокий порог хладноломкости стали, находящийся обычно в области положительных температур;
— склонность к значительному охрупчиванию в око — лошовной зоне;
— низкая пластичность и вязкость металла шва, выполненного сварочными материалами аналогичного со сталью химического состава;
— невозможность устранить охрупчивание термообработкой.
Сварку таких сталей необходимо выполнять с минимальным тепловложением, так как с увеличением погонной энергии возрастает склонность зон сварного соединения к росту зерен, появлению микротрещин и падению пластичности. При этом снижается сопротивляемость сварного соединения локальным повреждениям и меж- кристаллической коррозии. В процессе сварки возникает опасность коробления и появляется повышенный уровень остаточных напряжений.
После сварки в ряде случаев требуется термообработка.
Окисляемость металла под термическим действием сварочной дуги определяется его химической активностью. От этого напрямую зависит степень защиты сварочного шва, применяемой при сварке. Чем выше химическая активность металла, тем качественнее должна быть защита. Наибольшей химической активностью отличаются титан, ниобий, цирконий, вольфрам, молибден, тантал и некоторые другие. Поэтому при сварке этих металлов недостаточно применение флюсов и защитных покрытий, так как в защите нуждается не только сварочный шов, но и прилегающая к нему область. Самой эффективной защитой в данном случае, служит сварка в вакууме или в среде инертного газа высокой чистоты.
Сварка остальных цветных металлов (меди, алюминия, магния, никеля и их сплавов) тоже требует высокой защиты, которую обеспечивают инертные газы, флюсы и специальные электродные покрытия.
Для сварки сталей и сплавов на основе железа в качестве защитных средств используют флюсы и электродные покрытия.
Прочность сварных соединений — это свойство, не разрушаясь, воспринимать определенные нагрузки в тех или иных заданных условиях. При этом учитывают как рабочие, так и предельные нагрузки.
Под рабочими нагрузками понимают суммарные напряжения, возникающие от собственного веса, внешних нагрузок, появляющихся в процессе эксплуатации, и собственных напряжений, создающихся при сварке, сборке и т. д.
Предельными считаются нагрузки, когда наступает текучесть в основном сечении, возникшая под действием статических, повторно-переменных и динамических сил.
При этом образуются максимально допустимые повреждения или деформации, за которыми следует потеря эксплуатационной способности конструкции.
При расчете несущей способности сварочного шва ориентируются на допустимое напряжение в наиболее опасном сечении элемента і и допустимое напряжение, составляющее некоторую часть от предела текучести нзэ. При этом обязательно должно выдерживаться соотношение: Н5э і s. При таком соотношении элемент конструкции удовлетворяет требованиям прочности. Для большей уверенности применяют коэффициент запаса прочности л, который гарантирует ненаступление текучести и для низкоуглеродистых сталей лежит в пределах 1,35—1,50, а нзэ “ 160 Мпа.
Допустимое напряжение в наиболее опасном сечении s определяют по формуле:
S= N/F,
где F— площадь поперечного сечения элемента, a N — осевое усилие, прикладываемое к нему. ‘
Говоря о прочности сварочного соединения, не следует забывать о его пористости и трещинах, оказывающих значительное влияние на этот показатель.
Поры в сварочном шве возникают при выделении газов в процессе кристаллизации металла. Как правило, это азот, водород или окись углерода, получаемые в результате химических реакций. Но поры в сварочном шве могут возникать не только от газов. Это явление случается при повышенной тугоплавкости, вязкости и плотности шлаков, которые не покидают пределы сварочного шва.
Поры могут быть внутренними или наружными, располагаться по оси шва или на его границах, форма их может быть округлая, овальная или более сложная, а их размеры могут колебаться от нескольких микрон до не-
Рис. 6. Наличие горячих трещин в сварных соединениях:
1, 2, 3 — поперечные трещины шва и зоны вокруг него в материале; 4, 5— трещины продольные
скольких миллиметров. Уменьшению пористости сварочного шва способствует предсварочная подготовка, которая заключается в тщательной зачистке сварного соединения от грязи, масел, ржавчины и прочих посторонних включений. Борются с пористостью при помощи правильно подобранных режимов сварки, защитными покрытиями и флюсами, вводимыми в сварочную ванну.
Трещины в массиве шва и околошовпой зоны могут быть холодными и горячими. Горячие трещины (рис. 6) возникают в процессе кристаллизации жидкой фазы металла. Этому явлению способствуют линейные сокращения металла, возникающие в результате внутренних напряжений. Размеры и направление горячих трещин могут быть самыми различными и зависят от соответствия материала, электродов и режимов сварки.
Для определения этого соответствия сначала сваривают пробный образец, который подвергают тщательному анализу.
Наличие трещин может определяться визуально под увеличением, а ответственные детали подвергают про — светке или облучению.
Холодные трещины чаще всего имеют микроскопический характер и возникают при температурах не более 200°С. Причинами появления холодных трещин может быть хрупкость металла при быстром его охлаждении, остаточные напряжения в сварных соединениях иди повышенное содержание водорода.
Коррозия сварных соединений снижает прочность шва и его долговечность. В связи с изрядными структурными изменениями сварных соединений они обладают большей коррозийной активностью по сравнению с основным металлом. Коррозия может быть общей и местной.
При общей коррозии поражается вся поверхность металла, что свидетельствует о его низкой коррозийной стойкости.
Местная коррозия проявляется в наличии отдельных ржавых пятен, точек. Она может быть как поверхностная, так и межкристаллитная.
———- j
Wltfr ——*
Наиболее опасна межкристаллитная коррозия, которая проникает вглубь зерен, не разрушая их. Наиболее характерные коррозийные разрушения сварного соединения показаны на рис. 7.
Рис. 7. Коррозионные разрушения при сварке;
А — общая коррозия: 1 — равномерное распределение; 2 — шовная коррозия; 3 — интенсивная коррозия всего металла; 4 — ржавчина в зоне термического влияния; Б— местная1 коррозия: /— коррозия в термической зоне (межкристаллитная); 2— шовная коррозия; 3 — коррозия в зоне сплавления; 4 — точечная коррозия; В — усталость (коррозийное вытрескивание)
2-Сват>очные работы
Избежать этого опасного явления помогает правильный подбор материалов, сварочных электродов, применение защитных покрытий и замедлителей, которые наносят на поверхность металла или в коррозионную среду. Хорошие результаты дает применение сварочной проволоки с высокой коррозийной стойкостью. При сварке такой проволокой получается шов с большей коррозийной стойкостью, чем основной металл. На коррозийную активность сварочного шва Оказывают влияние и выбранные режимы сварки.
Любой сварочный аппарат это электрический прибор, который получая ток из сети, преобразует его до нужных параметров и выдает электрическую дугу постоянного тока с высокой его силой (сто – двести ампер). …
Сварочные работы могут стать причиной пожара, если не выполняются элементарные требования противопожарной защиты. Причиной пожара могут стать искры и капли расплавленного металла, небрежное обращение с огнем сварочной горелки, наличие на …
Суть кислородной резки заключается в сгорании разрезаемого металла под воздействием струи кислорода и удалении из разреза шлаков, образованием которых неизбежно сопровождается этот процесс (рис. 95). Рис. 95. Схема выполнения газовой …