Какие свойства мелкого и крупного заполнителя нормируются гостом
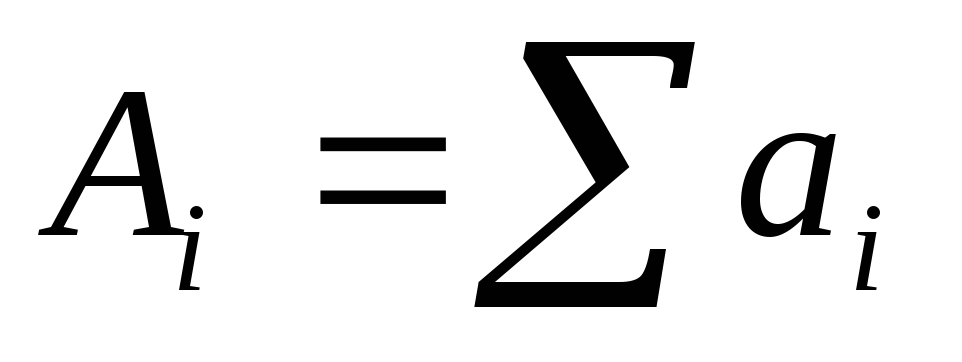
Щебень –
рыхлосыпучий материал, получаемый путем
дробления крупных кусков различных
твердых горных пород с размером частиц
от 5 до 70 мм.
Гравий– рыхлый
материал, образовавшийся в результате
естественного разрушения (выветривания)
твердых горных пород и состоящий из
зерен округлой формы с размером частиц
от 5 до 70 мм.
Крупный заполнитель
выполняет в бетоне роль несущего каркаса.
Оценка качества
крупного заполнителя производится по
следующим основным показателям:
зерновому составу
и наибольшей крупности зерен;содержанию
пылевидных, глинистых частиц и вредных
примесей ;форме зерен;
прочности;
радиационно-гигиенической
характеристике.
Плотность крупного
заполнителя должна быть в пределах
2000-2800 кг/м3, марка по морозостойкости
– не ниже проектной марки бетона по
морозостойкости. В расчетно-графической
работе необходимо дать оценку качества
крупного заполнителя требованиям ГОСТ
26633-91. Требования ГОСТ приведены в
приложении 1.
Мелкий
заполнитель.
В
качестве мелкого заполнителя в плотных
бетонах чаще всего применяют природный
песок.
Песок
– рыхлая смесь зерен крупностью 0,16-5
мм, образовавшаяся в результате
естественного разрушения твердых горных
пород. Природные пески в зависимости
от условий залегания могут быть речные,
морские и горные (овражные).
К
мелкому заполнителю из природных песков
предъявляют требования по следующим
показателям:
зерновому
составу и модулю крупности;содержанию
пылевидных и глинистых частиц, вредных
примесей;петрографическому
составу;радиационно-гигиенической
характеристике.
При подборе состава
бетона учитывают истинную плотность,
которая должна быть 2000-2800 кг/м3.
Зерновой состав
песка имеет большое значение для
получения плотного бетона заданной
марки при минимальном расходе цемента.
В бетоне песок
служит для заполнения пустот между
зернами крупного заполнителя, в то же
время все пустоты между зернами песка
должны быть заполнены цементным тестом.
С целью уменьшения
расхода цементного теста следует
применять пески с малой пустотностью
и наименьшей суммарной поверхностью
частиц. Крупный песок имеет небольшую
поверхность зерен, но значительную
пустотность. Лучшими являются крупные
пески, содержащие оптимальное количество
средних и мелких частиц. Применение
такого песка позволяет получить бетон
плотной структуры. В расчетно-графической
работе необходимо в соответствии с
требованиями ГОСТ 26633-91 дать оценку
качества песка в соответствии с проектным
заданием.
Требования ГОСТ
к песку приведены в приложении 3.
2.3.Цемент.
В
качестве вяжущих материалов в плотном
бетоне на плотных заполнителях следует
применять портландцемент и
шлакопортландцемент, сульфатостойкий
цемент и цемент с активными минеральными
добавками.
В расчетно-графической
работе необходимо указать марку и
активность цемента, к какой группе по
срокам схватывания относится выбранный
цемент.
2.4.Вода.
В расчетно-графической
работе необходимо указать какого
качества вода применяется для приготовления
бетонной смеси.
Материалы для
бетона. Определение их качества.
3.1. Испытание
щебня (гравия).
3.1.1. Определение
зернового состава щебня (гравия).
Теоретическая
часть.
Зерновой
состав щебня в значительной мере влияет
на качество приготовленного на нем
бетона. При выборе зернового состава
крупного заполнителя необходимо исходить
из основного требования: получить
наименьший объем пустот в крупном
заполнителе, а, следовательно, наименьший
расход цемента в бетоне заданной марки.
Для определения
зернового состава используют метод
ситового анализа.
Зерновой состав
щебня (гравия) характеризуется частными
и полными остатками на ситах № 70, 40, 20,
10, 5 и проходом через сито № 5, а также
наибольшим диаметром зерен щебня ДНБ.
Частным остатком
называется количество материала на
каждом сите, выраженное в килограммах
или в процентах:
(3.1)
где
– частный остаток, %;
– частный остаток, кг;
– навеска материала, кг.
Полным остаткомназывается сумма частного остатка на
данном сите и частных остатков на ситах
с большими размерами отверстий.
(3.2)
Проход
(3.3)
где Аi– полный остаток на данном сите, %;
а0+ … + аi– частные остатки на всех ситах с
большими размерами отверстий плюс
остаток на данном сите, %.
Фракцией
называется остаток на данном сите,
прошедший через сито предыдущего номера.
У щебня существуют
фракции 40-70, 20-40, 10-20, 5-10 мм. Зерновой
состав щебня должен соответствовать
требованиям ГОСТ, т.е. кривая полных
остатков должна лежать в зоне оптимального
зернового состава.
По полным остаткам
устанавливают наибольшую и наименьшую
крупность зерен щебня (гравия). За
наибольшую крупность зерен (Д) принимают
размер отверстий того верхнего сита,
на котором полный остаток не превышает
10%, а занаименьшую крупность (d)
– размер отверстия нижнего сита, полный
остаток на котором составляет не менее
90 %. Кроме того, вычисляют 0,5(Д+d)
и 1,25Д.
Приборы и
материалы.
Навеска щебня
(гравия) в соответствии с наибольшей
крупностью.Набор стандартных
сит с размерами отверстий сит 70, 40, 20,
10 и 5 мм.Весы торговые с
разновесами.
Методика
выполнения работы.
1.
Устанавливаем наибольшую крупность
щебня (гравия) Д и выбираем навеску щебня
в зависимости от Д.
Рассеиваем
навеску на стандартной колонке сит.Определяем
частные остатки на ситах путем их
взвешивания.Подсчитываем
полные остатки на ситах.Устанавливаем
наименьшую и наибольшую крупность
зерен щебня, т.е dи Д.Результаты
испытаний записываем в табл. 3.1.
Лабораторный
журнал.
Таблица
3.1.
Зерновой
состав щебня (гравия).
Остаток | Размеры | Сумма | |||||
70 | 40 | 20 | 10 | 5 | поддон | ||
Частный | 10 | ||||||
Частный | 100 | ||||||
Полный | — | — |
Расчетная часть.
Данные
расчета номеров контрольных сит заносим
в таблицу 3.2:
Таблица
3.2
Номера | Пределы | |
формула | Мм | |
D d 0,5(D+d) 1,25D | 0-10 90-100 30-80 0-0,5 |
Примечание:
номера контрольных сит 0,5(D+d) и 1,25 D
принимаются по ближайшим стандартным
размерам сит.
Строим
зону оптимального зернового состава
по пределам ГОСТ (рис.1).Наносим
полученный зерновой состав в полных
остатках на рис. 1.
Рис.1.
Область зернового состава щебня.
Вывод.Делается вывод о соответствии зернового
состава испытываемого щебня требованиям
ГОСТ 8267-93 (прил. 2).
Соседние файлы в предмете [НЕСОРТИРОВАННОЕ]
- #
- #
- #
- #
- #
- #
- #
- #
- #
- #
- #
Главная → Статьи
Крупные заполнители
В качестве крупного заполнителя для бетона используют гравий, имеющий округлые зерна с гладкой поверхностью, и щебень, имеющий угловатые зерна с шероховатой поверхностью. Щебень, как правило, получают дроблением крупных кусков горных пород, в том числе и гравия. Форма зерен и гладкость поверхности влияют на сцепление заполнителя с вяжущим и на удобоукладываемость бетонной смеси.
В зависимости от насыпной плотности и структуры зерен крупного заполнителя различают плотные (тяжелые) заполнители (Рнас > 1200 кг/м3), используемые для тяжелого бетона, и пористые (рнас < 1200 кг/м3), используемые для легкого бетона.
Насыпная плотность крупного заполнителя — один из важных качественных показателей. Она зависит от плотности зерен заполнителя и от его межзерновой пустотности.
Межзерновая пустотность а обычно составляет 0,4…0,5. Это означает, что около половины объема крупного заполнителя занимает воздух. При использовании в бетоне важно, чтобы межзерновая пустотность заполнителя была возможно меньше. В этом случае снижается расход цемента при сохранении требуемых свойств бетона. Уменьшить межзерновую пустотность заполнителя можно правильным подбором зернового состава, так, чтобы мелкие зерна занимали пустоты между крупными.
Зерновой состав. По крупности зерен щебень и гравий разделяют на следующие фракции: 5… 10; 10…20; 20…40; 40…70. Для массивных конструкций допускается использовать фракции и большего размера. Во всяком случае, максимальный размер зерен заполнителя не должен быть больше ‘/5 минимального сечения бетонного элемента.
В строительстве применяют крупный заполнитель в виде смеси фракций, обеспечивающей минимальную межзерновую пустотность, или в виде отдельных фракций при условии последующего их смешения в заданных соотношениях. Чем меньше межзерновая пустотность, тем меньше расход цементно-песчаного раствора. (а в конечном счете цемента), заполняющего в бетоне пустоты между зернами заполнителя.
К плотным заполнителям для тяжелого бетона относятся гравий, получаемый из природных залежей (его обработка заключается в сортировке по фракциям и промывке), и щебень, получаемый дроблением горных пород, крупных фракций гравия или плотных металлургических шлаков.
Содержание различных фракций в крупном заполнителе для бетона нормируется стандартами.
Прочность крупного заполнителя для тяжелых бетонов должна быть в 1,5…2 раза выше прочности бетона. Оценка прочности заполнителя может производиться по прочности той горной породы, из которой получен заполнитель, путем испытания выпиленных из нее кернов (цилиндрических образцов) или путем оценки дробимости самого заполнителя. Дробимость заполнителя оценивается по количеству мелочи, образующейся при сдавливании пробы заполнителя (гравия или щебня) в стальной форме под определенным усилием.
Морозостойкость заполнителя должна также быть выше проектной морозостойкости бетона.
Вредными примесями в крупном заполнителе, как и в песке, являются органические, пылеватые и глинистые. Методы их определения такие же, как и для песка. Особенно вредна глина на поверхности заполнителя, так как в этом случае она препятствует его сцеплению с цементным камнем. Количество пылеватых, глинистых и илистых примесей, определяемых отмучиванием, не должно быть более 1…3% в зависимости от вида заполнителя и класса бетона. Глина в виде комков снижает морозостойкость бетона, поэтому ее присутствие недопустимо.
В крупном заполнителе не должно быть зерен, содержащих активный (аморфный) кремнезем, так как это может со временем вызвать разрушение бетона.
Радиационно-гигиеническая оценка содержания естественных радионуклидов обязательна для всех заполнителей, и в особенности для получаемых из промышленных отходов (металлургических шлаков и т. п.).
Пористые заполнители для легких бетонов получают главным образом искусственным путем (например, керамзит, шлаковую пемзу, аглопорит и перлит). Из природных пористых заполнителей применяют щебень из пемзы, туфа и пористых известняков, которые используют в качестве местного материала.
Марку пористых заполнителей устанавливают по их насыпной плотности (кг/м).
Для пористых заполнителей еще в большей степени, чем для плотных, имеет значение правильный зерновой состав. Пористые заполнители выпускают в виде фракций размерами 5… 10 мм; 10…20 мм и 20…40 мм. При приготовлении бетонной смеси их смешивают в требуемом соотношении.
Керамзит — гранулы округлой формы с пористой сердцевиной и плотной спекшейся оболочкой. Благодаря такому строению прочность керамзита достаточно высокая при небольшой насыпной плотности (250…600 кг/м ). Получают керамзит быстрым обжигом во вращающихся печах легкоплавких глинистых пород с большим содержанием оксидов железа и органических примесей до их вспучивания.
Керамзит выпускают в виде гравия (гранулы 5…40 мм) и песка (зерна менее 5 мм). Марки керамзита от 250 до 600 кг/м. Морозостойкость керамзита не менее F15.
Шлаковая пемза — пористый щебень, получаемый вспучиванием огненно-жидких металлургических шлаков путем их быстрого охлаждения водой или паром. Этот вид пористого заполнителя экономически очень эффективен, так как сырьем служат промышленные отходы, а переработка их крайне проста. Марки шлаковой пемзы от 400 до 1000 кг/м . Прочность ее соответственно от 0,4 до 2 МПа.
Аглопорит — пористый заполнитель в виде гравия или щебня, получаемый спеканием (агломерацией) сырьевой шихты из глинистых пород и топливных отходов. Марки аглопорита от 400 до 900.
Вспученные перлитовый песок и щебень — пористые зерна белого или светло-серого цвета, получаемые путем быстрого (1…2 мин) нагрева до температуры 1000…1200 С вулканических горных пород, содержащих небольшое количество (3…5%) гидратной воды (перлита и др.). При обжиге исходная порода увеличивается в объеме в 5… 15 раз, при этом пористость образующихся зерен достигает 85…90%.
Щебень, выпускаемый двух фракций (5… 10 и 10…20 мм), имеет насыпную плотность от 200 до 500 кг/м . Перлитовый песок — особо легкий вид мелкого заполнителя: его насыпная плотность от 75 до 200 кг/м3.
—
Крупными заполнителями в тяжелом бетоне служат гравий, щебень, щебень из гравия, в легком — пористые заполнители.
Гравий представляет собой осадочную горную породу в виде скопления зерен размерами 5…70 мм округлой формы и с гладкой поверхностью. В гравий входит некоторое количество песка. При содержании песка 25…40% материал называют песчано-гравий-ной смесью.
Щебень получают дроблением массивных плотных горных пород на куски размерами 5…70 мм. Зерна щебня — угловатой формы и с более развитой, чем у гравия, шероховатой поверхностью. Благодаря этому сцепление с цементным камнем у щебня выше, чем у гравия. Для высокопрочного бетона предпочтительно применять щебень, для бетонов средней прочности 15…30 МПа — более дешевый местный гравий.
Щебень из гравия изготовляют дроблением гравия, гальки или валунов. В этом щебне содержится не менее 80% дробленых зерен, т. е. таких, поверхность которых околота более чем наполовину. По свойствам щебень из гравия занимает промежуточное положение между щебнем и гравием.
Зерновой состав крупного заполните-л я характеризуют его наибольшей и наименьшей крупностью. Наибольшая крупность заполнителя D соответствует размеру отверстий стандартного сита, на котором полный остаток еще не превышает 10% по массе. Наименьшая крупность d определяется размером отверстий первого из сит, полный остаток на котором превышает 95%, т.е. через него проходит не более 5% просеиваемой пробы. Наименьшая крупность обычно равна 5 мм.
Наибольшая крупность заполнителя должна соответствовать размерам бетонируемой конструкции и расстоянию между соседними стержнями арматуры. Это позволяет равномерно, без зависаний, распределять бетонную смесь в опалубке или форме.
При изготовлении бетонных плит наибольшая крупность зерен заполнителя должна быть не более половины толщины плиты, для тонкостенных конструкций— не более 1/3—1/2 толщины изделия. В железобетонных конструкциях применяют заполнители с наибольшей крупностью не более ‘/2 наименьшего расстояния в свету между стержнями арматуры.
При транспортировании смесей по бетоноводу наибольшую крупность заполнителей устанавливают в зависимости от его внутреннего диаметра. Для гравия она должна быть не более 0,4 диаметра бетоно-вода, для щебня — не более 1/3. Крупность заполнителей в бетонных смесях, подаваемых по хоботам и виброхоботам, принимают равной не более 1/3 их диаметра. Кроме того, содержание зерен плоской (лещадной) и игловатой формы ограничивают 5% по массе, в противном случае ухудшается удобопере-качиваемость смесей, а детали бетононасоса быстро выходят из строя.
Щебень или гравий применяют, как правило, фракционированным. Зерновой состав каждой фракции заполнителя или смеси фракций назначают таким, чтобы обеспечить минимальный расход цемента в бетоне. Стандартные требования к зерновому составу крупного заполнителя — щебня, гравия и щебня из гравия — представлены на рис. 28. Заполнители признают удовлетворительными по зерновому составу, если кривая их просеивания попадает в область, ограниченную ломаными линиями.
Содержание вредных примесей, а также глинистых, илистых и пылевидных частиц в крупных заполнителях ограничивают так же, как и в песке.
Прочность заполнителей влияет на прочность бетона. Требования по прочности устанавливают только для крупного заполнителя, поскольку чаще всего применяемые в качестве мелкого заполнителя кварцевые пески заведомо прочнее бетона: предел прочности при сжатии кварца свыше 1000 МПа, а максимальная прочность бетона по ГОСТ 26633—85 составляет 80 МПа.
Прочность крупного заполнителя нормируют с учетом прочности бетона. Так, марка щебня из естественного камня должна превышать прочность бетона не менее чем в 1,5…2 раза. Во всех случаях щебень из изверженных горных пород должен быть марки не ниже 80 МПа, из метаморфических пород—не ниже 60, из осадочных пород — не ниже 30 МПа. Содержание в щебне и гравии зерен слабых и выветренных пород—не более 10% по массе.
Морозостойкость щебня и гравия должна обеспечивать получение проектной марки бетона- по морозостойкости. Определяют ее путем попеременного замораживания и оттаивания пробы заполнителя в водонасыщенном состоянии. По морозостойкости крупные заполнители подразделяют на семь марок: 15, 25, 50, 100, 150, 200 и 300. Марка заполнителя по морозостойкости характеризует число циклов замораживания — оттаивания, при котором потеря массы пробы не превышает 5% (исключение составляют марки F15 и F25, для которых установлен предел 10%).
Рис. 28. Кривые зернового состава крупных заполнителй:
а —одной фракции (5…10; 10…20; 20…40; 40…70 мм), 6 —смеси фракций от 5 до 20 мм
Пористые заполнители бывают природные и искусственные. Природные заполнители получают путем дробления горных пород, например, вулканического туфа, пемзы, известкового туфа, известняка-ракушечника. Они относятся к местным материалам и используются для строительства в районах, незначительно удаленных от месторождения. Более распространены искусственные пористые заполнители, которые подразделяют на специально изготовляемые и заполнители из отходов промышленности.
К специально изготовляемым пористым заполнителям относят керамзит, аглопорит, вспученный перлит, вспученный вермикулит, шлаковую пемзу, зольный гравий. Из отходов промышленности используют топливные шлаки и золы.
Керамзит — продукт обжига вспучивающихся глин Его получают в виде гранул округлой формы размером 5…40 мм (керамзитовый гравий). При нагреве до температуры 1100… 1200 °С в легкоплавкой глине начинаются процессы газовыделения. В этом же температурном интервале глина размягчается. Образующиеся газы вспучивают массу. Гранулы керамзита напоминают в изломе структуру застывшей пены. Поры большей частью замкнутые, размером не более 1 мм. Этот легкий и прочный заполнитель с насыпной плотностью не более 600 кг/м3 — основной материал для изготовления легкобетонных конструкций.
Керамзитовый песок получают дроблением некондиционных зерен керамзитового гравия до крупности 0,16…5 мм либо путем обжига сырья во взвешенном состоянии.
Аглопорит выпускают в виде пористого щебня, гравия или песка и получают при обжиге на спека-тельных (агломерационных) решетках глиносодер-жащего сырья, топливных зол или шлаков с добавкой 8… 10% топлива (каменного угля). Высокая температура, развивающаяся при сгорании угля, приводит к спеканию шихты, а образующиеся газы вспучивают массу, что в итоге приводит к получению пористого материала.
Вспученные перлит и вермикулит получают высокотемпературной обработкой сырья, содержащего небольшое количество химически связанной воды. Для изготовления вспученного перлита сырьем служат вулканические стеклообразные породы (перлит, обсидиан), а для вспученного вермикулита — гидрослюды. При температуре около 1000 °С обжигаемая порода размягчается, а образующийся водяной пар вспучивает частицы, увеличивая их в 5…20 раз. Получаются весьма легкие пористые заполнители — щебень и песок, используемые в основном для производства теплоизоляционного бетона.
Шлаковую пемзу изготовляют путем поризации расплава металлургического шлака при быстром охлаждении его водой. Куски шлаковой пемзы дробят и разделяют на фракции. Это один из самых дешевых пористых заполнителей, но не самый лучший: шлаковая пемза слишком тяжела.
Зольный гравий получают обжигом окатанных гранул, состоящих из пылевидной золы ТЭС с небольшой Добавкой топлива. Можно также изготовлять безобжиговый зольный гравий, в котором отдельные частицы золы скреплены в единое целое вяжущим веществом, например портландцементом.
Топливные шлаки образуются в топках при спекании и частичном вспучивании неорганических примесей, содержащихся в угле. Этот материал характеризуется значительной неоднородностью свойств, что ограничивает его применение.
Пылевидная зола теплоэлектростанций (зола-унос) образуется при сжигании размолотого каменного угля. Ее используют как мелкий заполнитель в легких бетонах при условии, что содержание частиц несгоревшего топлива не превышает установленных пределов.
Основная характеристика пористого заполнителя — насыпная плотность в сухом состоянии. Для крупного пористого заполнителя установлены марки по насыпной плотности 250… 1200 кг/м3, а для пористого песка— 100…1400 кг/м3. Крупные пористые заполнители поставляют раздельно по фракциям 5…10; 10…20 и 20…40 мм.
Прочность определяют путем раздавливания пробы крупного пористого заполнителя в цилиндре. Значения прочности для каждого вида заполнителей различны. У керамзитового гравия, например, она составляет 0,6…2,5 МПа.
Морозостойкость пористых заполнителей должна соответствовать марке не ниже F15.
Благодаря развитой системе пор заполнители способны поглощать значительное количество воды за-творения, причем скорость водопоглощения особенно велика в первые 15…20 мин, т.е. в момент приготовления и укладки бетонной смеси (рис. 29). Интенсивное впитывание воды в первоначальные сроки связано с тем, что в заполнителе есть крупные поры. В дальнейшем постепенно насыщаются тонкие поры и капилляры.
Быстрый отсос воды зернами заполнителя и развитая шероховатая поверхность его делают легкобетонные смеси недостаточно удобоукладываемыми. Поэтому при изготовлении легких бетонов особенно эффективно применять гидрофобно-пластифицирующие добавки.
Рис. 29. Кинетика поглощения воды керамзитовым гравием
Читать далее:
Природный песок
Общие сведения о заполнителях для бетона