Какие основные характеристики приняты для оценки мех свойств металлов
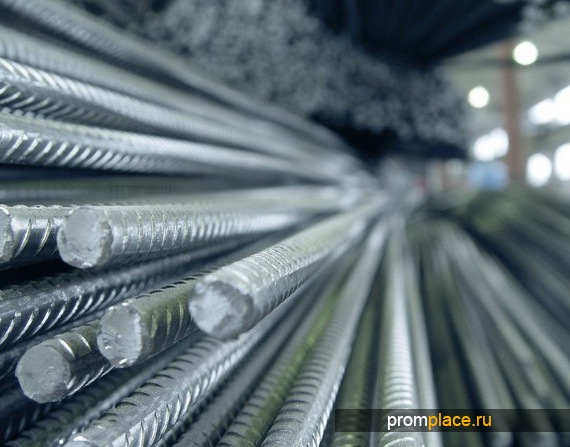
Основные механические свойства
К основным механическим свойствам относят прочность, пластичность, твердость, ударную вязкость и упругость. Большинство показателей механических свойств определяют экспериментально растяжением стандартных образцов на испытательных машинах.
Прочность — способность металла сопротивляться разрушению при действии на него внешних сил.
Пластичность — способность металла необратимо изменять свою форму и размеры под действием внешних и внутренних сил без разрушения.
Твердость — способность металла сопротивляться внедрению в него более твердого тела. Твердость определяют с помощью твердомеров внедрением стального закаленного шарика в металл (на приборе Бринелля) или внедрением алмазной пирамиды в хорошо подготовленную поверхность образца (на приборе Роквелла). Чем меньше размер отпечатка, тем больше твердость испытуемого металла. Например, углеродистая сталь до закалки имеет твердость 100 . . . 150 НВ (по Бринеллю) , а после закалки — 500 . . . 600 НВ.
Ударная вязкость — способность металла сопротивляться действию ударных нагрузок. Эта величина, обозначаемая КС (Дж/см2 или кгс • м/см ), определяется отношением механической работы А, затраченной на разрушение образца при ударном изгибе, к площади поперечного сечения образца.
Упругость — способность металла восстанавливать форму и объем после прекращения действий внешних сил. Эта величина характеризуется модулем упругости Е (МПа или кгс/мм2), который равен отношению напряжения а к вызванной им упругой деформации. Высокой упругостью должны обладать стали и сплавы для изготовления рессор и пружин.
Механические свойства металлов
Под механическими свойствами понимают характеристики, определяющие поведение металла (или другого материала) под действием приложенных внешних механических сил. К механическим свойствам обычно относят сопротивление металла (сплава) деформации (прочность) и сопротивление разрушению (пластичность, вязкость, а также способность металла не разрушаться при наличии трещин).
В результате механических испытаний получают числовые значения механических свойств, т. е. значения напряжений или деформаций, при которых происходят изменения физического и механического состояний материала.
Оценка свойств
При оценке механических свойств металлических материалов различают несколько групп их критериев.
- Критерии, определяемые независимо от конструктивных особенностей и характера службы изделий. Эти критерии находятся путем стандартных испытаний гладких образцов на растяжение, сжатие, изгиб, твердость (статические испытания) или на ударный изгиб образцов с надрезом (динамические испытания).
- Прочностные и пластические свойства, определяемые при статических испытаниях на гладких образцах хотя и имеют важное значение (они входят в расчетные формулы) во многих случаях не характеризуют прочность этих материалов в реальных условиях эксплуатации деталей машин и сооружений. Они могут быть использованы только для ограниченного числа простых по форме изделий, работающих в условиях статической нагрузки при температурах, близких к нормальной.
- Критерии оценки конструктивной прочности материала, которые находятся в наибольшей корреляции со служебными свойствами данного изделия и характеризуют работоспособность материала в условиях эксплуатации.
Конструкторская прочность металлов
Критерии конструктивной прочности металлических материалов можно разделить на две группы:
- критерии, определяющие надежность металлических материалов против внезапных разрушений (вязкость разрушения, работа, поглощаемая при распространении трещин, живучесть и др.). В основе этих методик, использующих основные положения механики разрушения, лежат статические или динамические испытания образцов с острыми трещинами, которые имеют место в реальных деталях машин и конструкциях в условиях эксплуатации (надрезы, сквозные отверстия, неметаллические включения, микропустоты и т. д.). Трещины и микронесплошности сильно меняют поведение металла под нагрузкой, так как являются концентраторами напряжений;
- критерии, которые определяют долговечность изделий (сопротивление усталости, износостойкость, сопротивление коррозии и т. д.).
Критерии оценки
Критерии оценки прочности конструкции в целом (конструкционной прочности), определяемые при стендовых, натурных и эксплуатационных испытаниях. При этих испытаниях выявляется влияние на прочность и долговечность конструкции таких факторов, как распределение и величина остаточных напряжений, дефектов технологии изготовления и конструирования металлоизделий и т. д.
Для решения практических задач металловедения необходимо определять как стандартные механические свойства, так и критерии конструктивной прочности.
Похожие материалы
Любое вещество, будь то газ, жидкость или твердое тело, обладает рядом специфических, только ему присущих свойств. Однако эти свойства позволяют не только индивидуализировать элементы, но и объединять их в группы по принципу схожести.
Посмотрите на металлы: с обывательской точки зрения это блестящие элементы, с высокой электро- и теплопроводностью, не восприимчивые к внешним физическим воздействиям, ковкие и легко свариваемые при высоких температурах. Достаточен ли этот перечень. чтобы объединить металлы в одну группу? Конечно же нет, металлы и их производные (сплавы) гораздо сложнее и обладают целым набором химических, физических, механических и технологических свойств. Сегодня мы поговорим лишь об одной группе: механических свойствах металлов.
Основные механические свойства металлов
Что это за свойства? Под механическими понимают такие свойства субстанции, которые отражают ее умение противостоять действиям извне. Известно девять основных механических свойств металлов:
— Прочность — означает, что приложение статической, динамической или знакопеременной нагрузки не приводит к нарушению внешней и внутренней целостности материала, изменению его строения, формы и размеров.
— Твердость (часто путают с прочностью) — характеризует возможность одного материала противостоять прониканию другого, более твердого предмета.
— Упругость — означает способность к деформированию без нарушения целостности под действием определенных сил и возвращению первоначальной формы после освобождения от нагрузки.
— Пластичность (часто путают с упругостью и наоборот) — также способность к деформации без нарушения целостности, однако в отличие от упругости, пластичность означает, что объект способен сохранить полученную форму.
— Стойкость к трещинам — под воздействием внешних сил (ударов, натяжений и пр.) материал не образует трещин и сохраняет наружную целостность.
— Вязкость или ударная вязкость — антоним ломкости, то есть возможность сохранять целостность материала при возрастающих физических воздействиях.
— Износостойкость — способность к сохранению внутренней и внешней целостности при длительном трении.
— Жаростойкость — длительная возможность противостоять изменению формы, размера и разрушению при воздействии больших температур.
— Усталость — время и количество циклических воздействий, которые материал может выдержать без нарушения целостности.
Часто, говоряо тех или иных свойствах, мы путаем их названия: технологические свойства относим к физическим, физические к механическим и наоборот. И это неудивительно, ведь несмотря на глубинные отличия, лежащие в основе той или иной группы свойств, механические свойства не только крайне тесно связаны с другими характеристиками металлов, но и напрямую зависят от них.
Физические свойства металлов
Наиболее взаимозависимы между собой механические и химические свойства металлов, ведь именно химический состав металла или сплава, его внутреннее строение (особенности кристаллической решетки) диктуют все остальные его параметры. Если говорить о механических и физических свойствах металлов, то их чаще других путают между собой, что обусловлено близостью данных определений.
Физические свойства часто неотделимы от механических. К примеру, тугоплавкие металлы еще и самые прочные. Главное же отличие лежит в природе свойств. Физические свойства — те что проявляется в покое, механические — только под воздействием извне. Не хуже других связаны механические и технологические свойства металлов. Например, механическое свойство металла «прочность» может быть результатом его грамотной технологической обработки (с этой целью нередко используют «закалку» и «старение»). Обратная взаимосвязь не менее важна, к примеру, ковкость проявление хорошей ударной вязкости.
Делая вывод, можно сказать, что зная некоторые химические, физические или технологические свойства можно предугадать, как будет вести себя металл под воздействием нагрузки (т.е. механически), и наоборот.
В чем отличия механических свойств металлов и сплавов?
Различаются ли механические свойства металлов и сплавов? Безусловно. Ведь любой металлический сплав изначально создается с целью получения каких-либо конкретных свойств. Некоторые сочетания легирующих элементов и основного металла в сплаве способны мгновенно преобразить легируемый элемент. Так алюминий ( не самый прочный и твердый металл в мире) в сочетании с цинком и магнием образует сплав по прочности сравнимый со сталью. Все это дает практически неограниченные возможности в получении веществ наиболее близких к требуемым.
Отдельное внимание следует уделить механическим свойствам наплавленных металлов. Наплавленным считается металл, с помощью которого производилась сварка двух или более частей какого-то металлического элемента или конструкции. Этот металл словно нитки соединяет разорванные части. От того, как будет вести себя «шов» под нагрузкой, будет зависеть безопасность и надежность всей конструкции. Исходя из этого, крайне важно, чтобы свойства наплавленного металла были не хуже, чем у главного металла.
Как определить механические свойства?
Экспериментальным путем. Среди основных методов определения механических свойств металлов можно выделить:
— испытания на растяжение;
— метод вдавливания по Бринеллю;
— определение твердости металла по Роквеллу;
— оценка твердости по Виккерсу;
— определение вязкости с помощью маятникового копра;
Механические свойства имеют весьма серьезное значение. Их знание позволяет использовать металлы и их сплавы с наибольшей эффективностью и отдачей.
1. Основные механические свойства металлов и сплавов
Свойство материалов принимать первоначальную форму после прекращения действия внешних сил называется упругостью, а деформация, исчезающая после снятия нагрузки, получила название упругой. Если к детали прикладывать все возрастающую нагрузку, то при достижении ею определенных значений и после прекращении ее действия деталь не примет своей первоначальной формы, а останется деформированной. Такая деформация называется пластической. Способность материала деформироваться под действием внешних нагрузок не разрушаясь и сохранять измененную форму после прекращения действия нагрузок называется пластичностью.
Материалы, не способные к пластическим деформациям, называются хрупкими. Такие материалы при избыточной нагрузке или под действием удара разрушаются внезапно. К хрупким материалам относятся (стекло, камень, чугун, закаленная сталь и др).
Важным свойством материалов, наряду с упругостью и пластичностью, является прочность. Она характеризуется максимальной нагрузкой, которую выдерживает материал детали не разрушаясь.
Детали машин в зависимости от условий работы должны обладать определенными механическими свойствами (прочностью, упругостью и пластичностью).
Прочность, упругость и пластичность металлов определяют при испытании образцов круглой или плоской формы на растяжение. Основными параметрами являются размер диаметра d и расчетная, контролируемая, длина l0 образца (рис. 1).
Рис. 1. Круглый образец до (а) и после (б) испытаний
Испытания выполняют на разрывных машинах.
Для получения сравнимых результатов введено понятие нормальное напряжение. Нормальным напряжением называют нагрузку, приходящуюся на единицу площади поперечного сечения образца. Нормальное напряжение обозначается греческой буквой σ (сигма).
Для нагрузки Р в ньютонах (Н) и площади поперечного сечения F в мм2, σ = Р/ F Па (паскаль).
Отношением наибольшей нагрузки, которую выдержал образец до разрыва, к первоначальной площади его поперечного сечения определяется величина предела прочности. Пределом прочности называется напряжение, отвечающее максимальной нагрузке, которую выдержал образец во время испытания, которое обозначается σв и выражается в Па.
Важная характеристика материалов — удельная прочность, которая определяется отношением предела прочности к удельному весу металла. Эта характеристика имеет большое значение при выборе материала, когда необходимо уменьшить массу машины.
Показатели пластичности, характеризующие способность металла деформироваться не разрушаясь, называют относительное удлинение и относительное сужение. Для получения этих показателей обе половины разорванного образца плотно прижимают друг к другу и измеряют длину рабочей части ( lк), а также диаметр образца в том месте, где произошел paзрыв (dк). Относительное удлинение обозначается греческой буквой δ и измеряется в процентах. Его определяют формуле:
(1)
где l0 – первоначальная расчетная длина; lк – расчетная длина после испытания.
Относительное сужение поперечного сечения образца Ψ, также измеряемое в процентах, находят по формуле:
(2)
где F0 — площадь поперечного сечения образца до испытания; Fk — площадь сечения образца в месте разрыва (в шейке).
Пределом текучести называется наименьшее растягивающее напряжение, при котором деформация продолжает расти без изменения нагрузки, которое обозначается σт и выражается в Па.
Чем больше относительное удлинение и относительное сужение поперечного сечения образца, тем более пластичен металл. Так, например, техническое железо при растяжении до разрыва удлиняется в 1,5 раза, у серого чугуна относительное удлинение и относительное сужение близки к нулю. Для изготовления большинства деталей машин и конструкций используют относительно пластичные материалы, так как они не подвержены опасности внезапного разрушения.
При длительной эксплуатации детали машин подвергаются повторно-переменным нагрузкам (растяжение-сжатие). При напряжениях, меньших предела текучести или предела упругости, они могут внезапно разрушиться. Это явление называется усталостью металлов.
Способность металлов работать в условиях многократных повторноили знакопеременных нагрузок, определяют их предел выносливости (или усталости). Пределом выносливости (усталости) называют максимальное напряжение, которое выдерживает материал, не разрушаясь, при достаточно большом числе повторно-переменных нагружений (циклов).
Для стальных образцов эту характеристику устанавливают при 10 млн. циклов, для цветных металлов — при 100 млн. циклов. Предел выносливости обозначают греческой буквой σ-1 и измеряют в Па.
2. Основные физические свойства материалов
Основные физические характеристики материалов следующие:
В процессе работы многие детали машин нагреваются до высоких температур, достигающих 1000°C и более. Для таких деталей важной характеристикой является жаропрочность — способность материалов сохранять необходимую прочность для сохранения своих параметров при высоких температурах. У металлов и сплавов, работающих длительное время под нагрузкой при высоких температурах, наблюдается явление ползучести, т.е. непрерывная пластическая деформация под действием постоянной нагрузки (металл «ползет»). При работе под нагрузкой в обычных производственных условиях при умеренной температуре (до 25°C ) ползучесть у большинства металлов отсутствует (рис. 2).
Рис. 2. Зависимость предела прочности и текучести от температуры
Твердость – характеристика механических свойств металла, влияющих на прочность и износостойкость поверхностей деталей и, в конечном счете, на габариты, вес и долговечность машины или механизма.
Твердость определяют глубиной проникновения под действием определенной нагрузки в поверхность металла наконечника прибора, имеющего форму шарика, конуса, пирамиды или иглы и изготовленного из малодеформирующегося материала (твердая закаленная сталь, алмаз, сапфир или твердый сплав). Твердость можно оценить методом сравнения. Например, зная твердость напильника или наконечника, пробуют снять стружку или поцарапать испытываемую поверхность, ударом по шарику подшипника получить отпечаток на испытываемой поверхности и др.
В приборах для измерения твердости металлов наибольшее распространение получило измерение твердости вдавливанием. В результате вдавливания с достаточно большой нагрузкой поверхностные слои металла, находящиеся под наконечником и вблизи него, пластически деформируются. После снятия нагрузки остается отпечаток. Особенность происходящей при этом деформации заключается в том, что она протекает в небольшом объеме, окруженном недеформированным металлом. Пластическую деформацию при вдавливании могут испытывать не только пластичные, но и хрупкие металлы (например, чугун), которые при обычных механических испытаниях (на растяжение, сжатие, кручение, изгиб) разрушаются хрупко почти без макроскопически заметной пластической деформации. Таким образом, твердость, характеризующая сопротивление пластической деформации, представляет собой механическое свойство металла, отличающееся способом измерения от других его механических свойств.
При испытании на твердость можно определять количественную зависимость между твердостью пластичных металлов, установленной путем вдавливания, и другими механическими свойствами (главным образом пределом прочности).
Метод Бринелля используют для определения твердости как металлов, так и полимерных материалов. Измерения осуществляют с помощью шарикового твердомера. Образец (деталь) устанавливают на столике 3 в нижней части неподвижной станины пресса (рис. 3), зачищенной поверхностью вверх. Поворотом вручную маховика 5 по часовой стрелке столик поднимают до упора. Нажимают кнопку 4 и включают двигатель 6, который перемещает кривошип 8 и постепенно нагружает шток 1. Под действием нагрузки, сообщаемой подвешенным к рычагу 10 грузом 9, шарик 2 вдавливается в образец. Нагрузка действует в течение определенного времени (10 — 60 с) в зависимости от твердости измеряемого материала (табл. 1), после чего вал двигателя, вращаясь в обратную сторону, перемещает кривошип и снимает нагрузку. После автоматического выключения двигателя поворотом маховика 5 против часовой стрелки опускают столик прибора и снимают образец. Время приложения нагрузки регулируется по шкале 7 реле двигателя. После испытания на образце остается отпечаток (лунка). Диаметр отпечатка измеряют лупой, на окуляре которой имеется шкала с ценой делений от 0,05 до 0,1 мм. Диаметр отпечатка измеряют с точностью до 0,05 мм (при вдавливании шарика диаметром 5 — 10 мм). Измерения выполняют в двух взаимно перпендикулярных направлениях. Показателем твердости будет средняя из полученных величин.
Рис. 3. Схема прибора Бринелля
Таблица 1. Условия для выбора шкалы при испытаниях по Роквеллу
Примерная твердость | Обозначение шкалы прибора для испытания по Роквеллу | Тип наконечника | Нагрузка, кгс | Допускаемые пределы измерения твердости по шкале Роквелла | |
по Бринеллю НВ | по Виккерсу HV | ||||
До 240 | 60 – 240 | В | Стальной шарик | 100 | 25 – 100 |
240 – 670 | 240 – 900 | С | Алмазный конус | 150 | 20 – 67 |
375 – 670 | 390 – 900 | А | Алмазный конус | 60 | 70 – 85 |
При измерении твердости поверхностей крупных деталей (направляющие чугунных станин) используют переносную лупу. Отпечатки на поверхности деталей образуются шариком, по которому в приспособлении производится тарированный удар.
Твердость по Бринеллю (НВ) — отношение нагрузки, действующей на шарик, к поверхности отпечатка:
(5)
где Р – нагрузка, действующая на шарик, кгс; F – поверхность отпечатка, мм2; D – диаметр вдавливаемого шарика, мм; d – диаметр отпечатка, мм.
При прочих равных условиях диаметр отпечатка d зависит от твердости металла. Чем выше твердость испытуемого металла, тем меньше диаметр отпечатка. Твердость измеряют при постоянном соотношении между величиной нагрузки Р и квадратом диаметра шарика D2. Это соотношение должно быть различным для металлов разной твердости.
Испытания вдавливанием шарика проводят с металлами небольшой и средней твердости (например, твердость стали должна быть не более 450 НВ).
Для измерения твердости поверхностей более 350 НВ применяют приборы, которые производят измерение твердости по глубине отпечатка, получаемого при вдавливании алмазного конуса или стального шарика — метод Роквелла.
Твердость по Роквеллу — условная характеристика, значение которой отсчитывается по шкале прибора для измерения твердости.
Этот метод позволяет изменять нагрузку в широких пределах без изменения значений твердости. Прибор (рис. 4) для измерения твердости по Роквеллу имеет столик 4, установленный в нижней части неподвижно станины. В верхней части станины укреплены индикатор 8 и шпиндельный узел 7, в котором имеется наконечник с алмазным конусом 6 (с углом при вершине 120°) или со стальным шариком диаметром 1,59 мм. На индикаторе 8 нанесены две шкалы (черная и красная) и имеются две стрелки — большая (указатель твердости), вращающаяся по шкале, и маленькая, по которой устанавливается величина предварительной нагрузки, сообщаемой вращением маховика 3.
Рис. 4. Схема прибора Роквелла
Плоская поверхность испытуемого образца, в которую вдавливается конус или шарик, должна быть тщательно отшлифована. Противоположная параллельная поверхность также должна быть ровной, зачищенной. Поворотом маховика 3 по часовой стрелке поднимают столик 4 таким образом, чтобы наконечник мог вдавливаться в поверхность установленного образца.
При дальнейшем подъеме столика приходят в движение стрелки на индикаторе. Подъем столика продолжают до тех пор, пока малая стрелка не примет вертикальное положение (красная точка на индикаторе). Это означает, что наконечник вдавился в образец под действием предварительной нагрузки, равной 100 Н (10 кгс). Предварительное нагружение проводят для того, чтобы исключить влияние упругой деформации и шероховатости поверхности образца на результаты измерений. Когда образец получит предварительную нагрузку, равную 100 Н, большая стрелка на индикаторе примет вертикальное или близкое к нему положение. Для обеспечения точности измерения необходимо, чтобы большая стрелка совпала с нулем на черной шкале индикатора. Если большая стрелка не совпадает с нулем, не меняя величину предварительного нагружения и, следовательно, не вращая маховик, поворачивают шкалу (круг) индикатора барабаном 2 через тросик 5 таким образом, чтобы нуль на черной шкале индикатора совпал с большой стрелкой. Отклонение стрелки от вертикали допускается в пределах ±5 единиц шкалы.
Плавным движением нажимают клавишу 1, которая приводит в действие привод механизма нагружения основной нагрузкой, определяемой грузом 9. Один груз на рычаге сообщает образцу дополнительную нагрузку 500 Н (50 кгс), следовательно, общая нагрузка составит 600 Н (60 кгс), два груза — 900 Н (90 кгс) при общей нагрузке 1000 Н (100 кгс), три груза1400 Н (140 кгс) при oбщей нагрузке 1500 Н (150 кгс). На приборе указана общая нагрузка. При нагружении нагрузки большая стрелка перемещается по шкале влево, против часовой стрелки. Время приложения основной нагрузки — 5 – 7 с. Стрелка возвращается в обратную сторону автоматически при снятии основной нагрузки (предварительная нагрузка остается). Цифра, которую указывает на шкале индикатора большая стрелка, является показателем твердости по Роквеллу. Записав эту цифру, поворачивают маховик против часовой стрелки, опускают столик прибора с образцом и снимают тем самым предварительную нагрузку.
Для каждой детали рекомендуется проводить не менее трех испытаний. С помощью прибора измеряют глубину отпечатка от алмазного конуса (стального шарика) или, точнее, разность между глубинами отпечатков, полученных от вдавливания наконечника под действием основной и предварительной нагрузок. Твердость по Роквеллу возрастает с увеличением твердости материала, что позволяет сравнивать показатели твердости по Роквеллу и по Бринеллю. Вместе с тем твердость по Роквеллу не имеет той размерности и того физического смысла, который имеет твердость по Бринеллю.
Однако показатель твердости по Роквеллу можно пересчитать на показатель твердости по Бринеллю с помощью диаграммы (рис. 5) или таблицы, построенных на основании многочисленных экспериментальных работ (табл. 2).
Рис. 5. Диаграммы соотношения твердости по Бринеллю и Роквеллу: а — при вдавливании алмазного конуса; б — при вдавливании стального шарика
Таблица 2. Соотношение чисел твердости по Бринеллю, Роквеллу и Виккерсу
Твердость по Виккерсу | Твердость по Бринеллю Dш=10 мм, Р=3000 кг | Твердость по Роквеллу | |||
шкал | |||||
диаметр отпечатка, мм | число твердости | C | B | A | |
(150 кг) | (100 кг) | (60 кг) | |||
1224 | 2,20 | 780 | 72 | — | 84 |
1116 | 2,25 | 745 | 70 | — | 83 |
1022 | 2,30 | 712 | 68 | — | 82 |
941 | 2,35 | 682 | 66 | — | 81 |
868 | 2,40 | 653 | 64 | — | 80 |
804 | 2,45 | 627 | 62 | — | 79 |
746 | 2,50 | 601 | 60 | — | 78 |
694 | 2,55 | 578 | 58 | — | 78 |
650 | 2,60 | 555 | 56 | — | 77 |
606 | 2,65 | 534 | 54 | — | 76 |
587 | 2,70 | 514 | 52 | — | 75 |
551 | 2,75 | 495 | 50 | — | 74 |
Твердость по Роквеллу можно измерять алмазным конусом с общей нагрузкой 1500 Н (150 кгс); в этом случае значение твердости характеризуется цифрой, на которую указывает стрелка на черной шкале С индикатора; твердость обозначается HRC; например, 65 HRC означает, что твердость материала составляет 65 единиц по Роквеллу по шкале С с нагрузкой 1500 Н (150 кгс). Алмазным конусом с нагрузкой 1500 Н (HRC) измеряют твердость: закаленной или низкоотпущенной стали (твердостью более 450 НВ), т.е. в условиях, когда вдавливание стального шарика (по Бринеллю или Роквеллу) в твердый материал может вызвать деформацию шарика и искажение результатов; материалов средней твердости (более 230 НВ), так как испытание алмазным конусом осуществляется быстро и приводит к меньшему изменению измеряемой поверхности, чем при испытании по Бринеллю; тонких поверхностных слоев, но толщиной более 0,5 мм (например, цементированного слоя).
Твердость по Роквеллу также можно измерять алмазным конусом с общей нагрузкой 600Н (60кгс); в этом случае значение твердости также характеризуется цифрой, на которую указывает стрелка на черной шкале С индикатора, но твердость обозначается HRA; твердость HRA можно перевести в твердость HRC по формуле: HRC = 2 HRA – 104.
Алмазным конусом с нагрузкой 600 Н (60 кгс, HRA) измеряют твердость очень твердых металлов (более 70 HRC), например твердых сплавов, когда вдавливание алмазного конуса с большей нагрузкой может вызвать выкрашивание алмаза, также твердых поверхностных слоев (0,3–0,5 мм) и тонких образцов (пластинок).
Твердость по Роквеллу также можно измерять стальным шариком с общей нагрузкой 1000 (100 кгс); в этом случае значение твердости характеризуется цифрой, на которую указывает стрелка на красной шкале В индикатора; твердость обозначается HRB.
Стальным шариком с нагрузкой 1000 Н (100 кгс, HRB) определяют твердость мягкой (отожженной) стали или отожженных цветных сплавов в деталях или образцах толщиной 0,8–2 мм, т.е. в условиях, когда измерение твердости по Бринеллю, выполняемое шариком большего диаметра, может вызвать смятие образца.
Выбор шкалы (А, В или С) производится по табл. 1. Расстояние от центра отпечатка до края образца или до центра другого отпечатка должно быть не менее 1,5 мм при вдавливании конуса и не менее 4 мм при вдавливании шарика, толщина образца — не менее 10-кратной глубины отпечатка.
Твердость следует измерять не менее чем в трех точках (особенно алмазным конусом), т.е. не менее трех раз на одном образце. Для расчета лучше принимать среднее значение результатов второго и третьего измерений и не учитывать результат первого измерения. Для определения твердости по Роквеллу требуется меньше времени (30 – 60 с), чем по Бринеллю, причем результат измерения виден на шкале (указан стрелкой). При измерении твердости по Роквеллу остается меньший отпечаток на поверхности детали. Твердость очень тонких слоев металла (толщиной менее 0,3 мм) при нагрузках 600 и 1500 Н (60 и 150 кгс) измерять нельзя, так как алмазный конус проникает на глубину, превышающую толщину этих слоев. Вместе с тем с увеличением твердости измеряемого материала глубина отпечатка уменьшается, вследствие чего снижается точность измерения (особенно металлов твердостью более 60 HRC). Для этих целей иногда применяют приборы типа суперроквелл, с помощью которых измеряют твердость при меньшей нагрузке и с меньшей глубиной вдавливания. Предварительная нагрузка при этом составляет 30 Н (3 кгс). Каждое деление шкалы индикатора такого прибора соответствует глубине вдавливания, равной 1 мкм. Поэтому чувствительность данного прибора заметно выше.
Для измерения твердости поверхностей более 350 НВ также применяют приборы, которые производят измерение твердости по глубине пирамидального отпечатка — метод Виккерса. Твердость по Виккерсу — отношение нагрузки на стандартную пирамиду при вдавливании ее вершины в исследуемый материал к площади поверхности пирамидального отпечатка:
(6)
где D — диагональ отпечатка.
Используя таблицу (табл. 2), твердость по Бринеллю можно перевести на твердость по Роквеллу и Виккерсу. Обычно по Бринеллю приводится твердость НВ≤350, по Роквеллу — HRC≤60, твердость свыше 60HRC приводят по шкале Виккерса, например — 1200 HV.
Просмотров: 724