Какие механические свойства чугуна наиболее сильно ослабляет графит
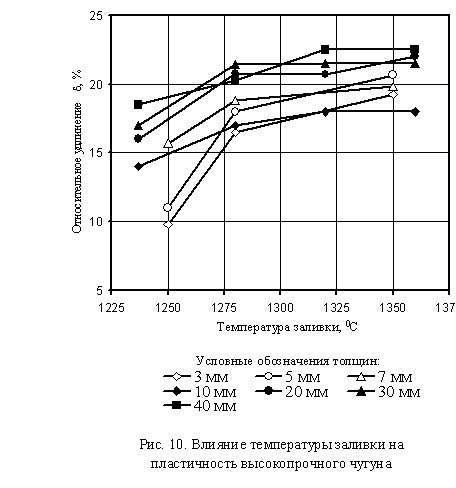
Графит имеет гексагональную слоистую решетку с небольшой энергией связи между атомами в разных слоях (силы Ван-дер-Ваальса), вследствие чего он обладает очень низкими твердостью, прочностью и пластичностью, значительно более низкими, чем у металлической основы. Графитные включения фактически представляют собой своеобразные трещины или пустоты, заполненные графитом. Чугун в связи с этим можно рассматривать как сталь, испещренную большим количеством таких трещин и пустот (графитных включений), ослабляющих металлическую основу. Чем больше графитных включений, чем они грубее, тем больше они разобщают металлическую основу и тем ниже механические свойства чугуна.
Графитные включения в чугунах имеют пластинчатую, вермикулярную, шаровидную или хлопьевидную форму (рис. 7.2).
Пластинчатый графит, играющий роль острых трещин и надрезов, является резким концентратором напряжений. Под действием нормальных напряжений по концам таких графитных включений легко формируются очаги разруше-
Рис. 7.2. Структуры чугунов с разной металлической основой и формой графитовых включений
ния. По этой причине чугуны с пластинчатым графитом имеют самую низкую прочность при растяжении и изгибе.
Вермикулярный графит отличается от пластинчатого значительно меньшими размерами частиц – это очень мелкие и тонкие прожилки со скругленными концами. Скругленные графитные включения выполняют роль уже не трещин, а пустот и являются менее резкими концентраторами напряжений.
Наименьшая концентрация напряжений отмечается в чугунах с шаровидным графитом. Такие чугуны имеют самую высокую прочность при растяжении и изгибе.
Чугуны с хлопьевидным графитом уступают им по своим прочностным характеристикам, но превосходят чугуны с пластинчатым графитом.
Таким образом, прочность чугунов с графитом определяется строением металлической основы и формой графитных включений. При меньшей степени графитизации (например, в ферритно-перлитном и особенно в перлитном чугунах по сравнению с ферритным) количество (объем) и размеры графитных включений будут меньше.
Уровень пластичности чугунов определяется формой графита (табл. 7.2). Самую низкую пластичность имеет чугун с пластинчатым графитом.
Таблица 7.2
Влияние формы графитных включений на пластичность чугунов
Графит | Пластинчатый | Вермикулярный | Хлопьевидный | Шаровидный |
Относительное удлинение δ, % | <0,5 | 1…3 | 3…12 | 2…17 |
Чугуны с графитом широко применяются в промышленности. Наличие графита в структуре, определяющее низкую прочность чугунов, придает им ряд высоких технологических и эксплуатационных свойств:
- – графит улучшает литейные свойства, уменьшая усадку чугунов при кристаллизации (см. 11.2.1);
- – мягкий и хрупкий графит улучшает обрабатываемость чугунов резанием, способствуя образованию стружки надлома (стружка ломается на графитовых включениях);
- – графит обеспечивает чугунам хорошие антифрикционные свойства, он играет роль смазки в парах трения;
- – графит гасит вибрации и резонансные колебания;
- – чугуны с графитом мало чувствительны к надрезам и другим дефектам поверхности деталей, поскольку подобные дефекты в виде графитных включений уже имеются в самом чугуне.
Графитовые включения можно рассматривать как соответствующией формы пустоты в структуре чугуна. Около таких дефектов при нагружении концентрируются напряжения, значение которых тем больше, чем острее дефект. Отсюда следует, что графитовые включения пластинчатой формы в максимальной мере разупрочняют металл. Более благоприятна хлопьевидная форма, а оптимальной является шаровидная форма графита. Пластичность зависит от формы таким же образом. Относительное удлинение для серых чугунов составляет 0,5 %, для ковких – до 10 %, для высокопрочных – до 15%.
Наличие графита наиболее резко снижает сопротивление при жестких способах нагружения: удар; разрыв. Сопротивление сжатию снижается мало.
Положительные стороны наличия графита:
— графит улучшает обрабатываемость резанием, так как образуется ломкая стружка;
— чугун имеет лучшие антифрикционные свойства, по сравнению со сталью, так как наличие графита обеспечивает дополнительную смазку поверхностей трения;
— из-за микропустот, заполненных графитом, чугун хорошо гасит вибрации и имеет повышенную циклическую вязкость;
— детали из чугуна не чувствительны к внешним концентраторам напряжений (выточки, отверстия, переходы в сечениях);
— чугун значительно дешевле стали;
— производство изделий из чугуна литьем дешевле изготовления изделий из стальных заготовок обработкой резанием, а также литьем и обработкой давлением с последующей механической обработкой.
Серый чугун
Структура не оказывает влияние на пластичность, она остается чрезвычайно низкой. Но оказывает влияние на твердость. Механическая прочность в основном определяется количеством, формой и размерами включений графита. Мелкие, завихренной формы чешуйки графита меньше снижают прочность. Такая форма достигается путем модифицирования. В качестве модификаторов применяют алюминий, силикокальций, ферросилиций.
Серый чугун широко применяется в машиностроении, так как легко обрабатывается и обладает хорошими свойствами. В зависимости от прочности серый чугун подразделяют на 10 марок (ГОСТ 1412).
Серые чугуны при малом сопротивлении растяжению имеют достаточно высокое сопротивление сжатию.
Серые чугуны содержат углерода – 3,2…3,5 %; кремния – 1,9…2,5 %; марганца – 0,5…0,8 %; фосфора – 0,1…0,3 %; серы – < 0,12 %.
Структура металлической основы зависит от количества углерода и кремния. С увеличением содержания углерода и кремния увеличивается степень графитизации и склонность к образованию ферритовой структуры металлической основы. Это ведет к разупрочнению чугуна без повышения пластичности. Лучшими прочностными свойствами и износостойкостью обладают перлитные серые чугуны.
Учитывая малое сопротивление отливок из серого чугуна растягивающим и ударным нагрузкам, следует использовать этот материал для деталей, которые подвергаются сжимающим или изгибающим нагрузкам. В станкостроении это – базовые, корпусные детали, кронштейны, зубчатые колеса, направляющие; в автостроении — блоки цилиндров, поршневые кольца, распределительные валы, диски сцепления. Отливки из серого чугуна также используются в электромашиностроении, для изготовления товаров народного потребления.
Обозначаются индексом СЧ (серый чугун) и числом, которое показывает значение предела прочности, умноженное на 15.
Высокопрочный чугун с шаровидным графитом
Высокопрочные чугуны (ГОСТ 7293) могут иметь ферритную (ВЧ 35), феррито — перлитную (ВЧ45) и перлитную (ВЧ 80) металлическую основу. Получают эти чугуны из серых, в результате модифицирования магнием или цезием (добавляется 0,03…0,07 % от массы отливки). По сравнению с серыми чугунами, механические свойства повышаются, это вызвано отсутствием неравномерности в распределении напряжений из-за шаровидной формы графита.
Чугуны с перлитной металлической основой имеют высокие показатели прочности при меньшем значении пластичности. Соотношение пластичности и прочности ферритных чугунов — обратное.
Высокопрочные чугуны обладают высоким пределом текучести, что выше предела текучести стальных отливок. Также характерна достаточно высокая ударная вязкость и усталостная прочность, при перлитной основе.
Высокопрочные чугуны содержат: углерода – 3,2…3,8 %, кремния – 1,9…2,6 %, марганца – 0,6…0,8 %, фосфора – до 0,12 %, серы – до 0,3 %.
Эти чугуны обладают высокой жидкотекучестью, линейная усадка – около 1%. Литейные напряжения в отливках несколько выше, чем для серого чугуна. Из-за высокого модуля упругости достаточно высокая обрабатываемость резанием. Обладают удовлетворительной свариваемостью.
Из высокопрочного чугуна изготовляют тонкостенные отливки (поршневые кольца), шаботы ковочных молотов, станины и рамы прессов и прокатных станов, изложницы, резцедержатели, планшайбы.
Отливки коленчатых валов массой до 2..3 т, взамен кованых валов из стали, обладают более высокой циклической вязкостью, малочувствительны к внешним концентраторам напряжения, обладают лучшими антифрикционными свойствами и значительно дешевле.
Обозначаются индексом ВЧ (высокопрочный чугун) и числом, которое показывает значение предела прочности, умноженное на 100.
Ковкий чугун
Получают отжигом белого доэвтектического чугуна.
Хорошие свойства у отливок обеспечиваются, если в процессе кристаллизации и охлаждения отливок в форме не происходит процесс графитизации. Чтобы предотвратить графитизацию, чугуны должны иметь пониженное содержание углерода и кремния.
Ковкие чугуны содержат: углерода – 2,4…3,0 %, кремния – 0,8…1,4 %, марганца – 0,3…1,0 %, фосфора – до 0,2 %, серы – до 0,1 %.
Формирование окончательной структуры и свойств отливок происходит в процессе отжига. Отливки выдерживаются в печи при температуре 950…1000 оС в течении 15…20 часов. Происходит разложение цементита.
Структура после выдержки состоит из аустенита и графита (углерод отжига). При медленном охлаждении в интервале 760…720 оС, происходит разложение цементита, входящего в состав перлита, и структура после отжига состоит из феррита и углерода отжига (получается ферритный ковкий чугун).
При относительно быстром охлаждении вторая стадия полностью устраняется, и получается перлитный ковкий чугун.
Структура отожженного чугуна состоит из перлита, феррита и графита отжига (получается феррито-перлитный ковкий чугун)
Отжиг является длительной 70…80 часов и дорогостоящей операцией. В последнее время, в результате усовершенствований, длительность сократилась до 40 часов.
Различают 7 марок ковкого чугуна: три с ферритной (КЧ 30 – 6) и четыре с перлитной (КЧ 65 – 3) основой (ГОСТ 1215).
По механическим и технологическим свойствам ковкий чугун занимает промежуточное положение между серым чугуном и сталью. Недостатком ковкого чугуна по сравнению с высокопрочным является ограничение толщины стенок для отливки и необходимость отжига.
Отливки из ковкого чугуна применяют для деталей, работающих при ударных и вибрационных нагрузках.
Из ферритных чугунов изготавливают картеры редукторов, ступицы, крюки, скобы, хомутики, муфты, фланцы.
Из перлитных чугунов, характеризующихся высокой прочностью, достаточной пластичностью, изготавливают вилки карданных валов, звенья и ролики цепей конвейера, тормозные колодки.
Обозначаются индексом КЧ (высокопрочный чугун) и двумя числами, первое из которых показывает значение предела прочности, умноженное на 100, а второе – относительное удлинение — КЧ 30 — 6.
Отбеленные и другие чугуны
Отбеленные – отливки, поверхность которых состоит из белого чугуна, а внутри серый или высокопрочный чугун.
В составе чугуна 2,8…3,6 % углерода, и пониженное содержание кремния – 0,5…0,8 %.
Имеют высокую поверхностную твердость (950…1000 НВ) и очень высокую износостойкость. Используются для изготовления прокатных валов, вагонных колес с отбеленным ободом, шаров для шаровых мельниц.
Для изготовления деталей, работающих в условиях абразивного износа, используются белые чугуны, легированные хромом, хромом и марганцем, хромом и никелем. Отливки из такого чугуна отличаются высокой твердостью и износостойкостью.
Для деталей, работающих в условиях износа при высоких температурах, используют высокохромистые и хромоникелевые чугуны. Жаростойкость достигается легированием чугунов кремнием (5…6 %) и алюминием (1…2 %). Коррозионная стойкость увеличивается легированием хромом, никелем, кремнием.
Для чугунов также можно применять термическую обработку.
Тесты для самоконтроля
Методы изучения, оценки и Графит классифицируют по количеству и размерам включений, Графит оказывает сильное влияние на основные свойства Графитовые включения оказывают также надрезывающее влияние В общем случае графит уменьшает временное сопротивление и В то же время, в отличие от стали, чугун менее Наиболее прочной структурной составляющей чугуна является Таким образом, для повышения прочности чугуна его уменьшение количества феррита, исключение выделения уменьшение количества графита и размеров его включений; |
Чугун обладает
более низкими механическими свойствами, чем сталь
цементита распадается на мягкое пластичное железо и графит по реакции
Fe3C~>—»-3Fe-[-C. В зависимости от преобладающей структуры различают
серый чугун на перлитной…
Структура
отливок определяется химическим составом чугуна и технологическими
особенностями его термообработки. Механические свойства серого чугуна
зависят от свойств металлической матрицы
Графит улучшает обрабатываемость резанием.
Фосфор понижает механические свойства чугуна
и вызывает хладноломкость (образование трещин в холодных отливках). В
зависимости от состояния, в котором углерод находится в чугуне, чугун
подразделяется на белый…
Структура
металлической основы определяет твердость чугуна.
роль как надрезов металлической основы снижается и механические свойства
чугуна растут.Например, серый чугун (пластинчатая форма графита)
имеет низкие характеристики…
В.А. Изосимов, Р.Г. Усманов, М.Н. Канафин
(ООО «НПП «Технология», г. Челябинск)
Значительным достижением в развитии машиностроения является разработка способа получения высокопрочного чугуна с шаровидным графитом. В этом материале хорошо сочетаются высокие физико-механические и технологические свойства. В результате многочисленных исследований и большого производственного опыта установлено, что высокопрочный чугун (ВЧ) во многих случаях может успешно применяться взамен серого и ковкого чугуна, углеродистой и легированной стали.
Замена обычного серого чугуна высокопрочным позволяет значительно снизить вес отливок за счет уменьшения толщины их сечений, при сохранении и даже повышении эксплуатационной надежности.
Наиболее целесообразным в технико-экономическом соотношении является применение высокопрочного чугуна взамен стали для тонкостенных литых деталей сложной конфигурации. Этот чугун по сравнению со сталью обладает в 1,5-2,0 раза большей жидкотекучестью, не склонен к образованию горячих трещин и обеспечивает получение плотного металла в малых сечениях без применения «напусков». Вместе с тем стоимость литья из высокопрочного чугуна на 25-30% ниже стоимости стального литья.
Применение высокопрочного чугуна во многих случаях позволяет значительно снизить вес деталей и повысить коэффициент использования металла. Однако следует отметить что, несмотря на указанные преимущества высокопрочного чугуна по сравнению с другими литейными сплавами, область его применения и масштабы производства в России до последнего времени весьма ограничены. Это объясняется тем, что при организации массового производства отливок из этого чугуна встречаются значительные затруднения.
Наиболее трудной задачей является получение отливок из чугуна марок ВЧ40 и ВЧ60 по ГОСТ 7293-85. Вместе с тем применение чугуна этих марок позволяет в наибольшей степени использовать его высокие физико-механические свойства.
Основное затруднение заключается в том, что полученный металл не всегда соответствует требованию по механическим свойствам, особенно по характеристикам пластичности и вязкости.
В отливках часто образуются дефекты в виде «черных пятен», значительно снижающих прочность деталей. Характерными для отливок из ВЧ являются также усадочные дефекты и мелкие поверхностные газовые раковины.
Значительную трудность представляет получение перлитной структуры для марки ВЧ60, в которой феррита должно быть не более 20%.
В целях преодоления указанных затруднений авторами в сотрудничестве с работниками ряда заводов выполнялись работы, по результатам которых разработан и внедрен технологический процесс изготовления отливок из ВЧ, предусмотренных ГОСТ 7293-85. Активное участие в этих работах принимали специалисты кафедры «Литейное производство» ЮУрГУ.
Химический состав, выплавка и разливка чугуна.
Многочисленные наблюдения показали, что при производстве ВЧ встречается несколько характерных типов микроструктуры графита. Условно они названы: шаровидный, вермикулярный и смешанный.
В результате исследований установлено, что чугун со смешанной формой графита получается при содержании магния менее 0,035% и содержании углерода в жидком чугуне менее 3,0-3,2% перед вводом магния.
Для получения чугуна с полностью шаровидным графитом необходимо обеспечить содержание магния в пределах 0,04-0,1%, а также достаточное содержание углерода, причем шаровидный графит получается тем более устойчиво, чем выше содержание углерода в металле перед вводом магния.
Указанная закономерность не всегда согласуется с литературными данными /1,2/, в которых указывается, что для обеспечения получения шаровидного графита в чугуне с увеличением в нем содержания углерода, нужно увеличивать дозировку магния.
Для устойчивого получения шаровидного графита необходимо также, чтобы содержание серы в металле до ввода магния было не более 0,02%. /3, 4/
Форма графита в ВЧ оказывает решающее влияние на его пластичность и вязкость и мало сказывается на характеристиках прочности, что видно на рис. 1,2, где показаны результаты испытания механических свойств этого чугуна множеством плавок.
Рис. 1. Влияние формы графита на механические свойства высокопрочного чугуна
Рис. 2. Влияние формы графита на механические свойства высокопрочного чугуна
Влияние микроструктуры металлической основы на механические свойства ВЧ общеизвестно. Однако возникла необходимость в уточнении количества допустимого перлита в ферритном чугуне, учитывая, что в результате отжига некоторое его количество во многих случаях сохраняется. В связи с этим производилось изучение микроструктуры и механических свойств чугуна в лабораторных и производственных условиях. Форма графита в этих чугунах была полностью шаровидной. Химический состав колебался в сравнительно небольших пределах.
Полученные результаты (рис.3) показывают, что в ферритном чугуне марки ВЧ40 допустимо 10-15% перлита, а в марке ВЧ60 феррита может быть не более 10%.
Рис. 3. Влияние количества перлита в металлической основе на механические
свойства высокопрочного чугуна
В перлитном и ферритном ВЧ совершенно недопустим цементит, т.к. даже весьма незначительное его количество понижает ударную вязкость до значения менее 1кгм/см2.
Исследования влияния химического состава ВЧ на его механические свойства проводились на чугуне, выплавленном в лабораторных условиях в индукционной печи, а также в различных производственных агрегатах (вагранки, дуговые электропечи) на ряде заводов Урала. Во всех случаях использовали данные только тех плавок, чугун которых имел полностью шаровидный графит и ферритную металлическую основу в литом состоянии или после отжига (не более 10% перлита). Обобщенные результаты представлены на рис. 4,5,6,7.
Рис. 4. Влияние углерода на механические свойства высокопрочного чугуна.
Рис. 5. Влияние кремния на механические свойства высокопрочного чугуна.
Рис. 6. Влияние марганца на механические свойства высокопрочного чугуна.
Рис. 7. Влияние фосфора на механические свойства высокопрочного чугуна.
Как видно из данных рис.4 изменение содержания углерода от 2,4 до 3,9% не оказывает заметного влияния на все характеристики механических свойств ВЧ. Оно может выражаться лишь в том, что с понижением содержания углерода возрастает количество перлита, сохраняющегося после отжига. При этом вероятно также наличие структурного свободного цементита и графита нешаровидной формы.
С повышением содержания кремния от 2 до 3% механические свойства ВЧ также практически не изменяются (рис.5). Однако при дальнейшем повышении содержания кремния наступает заметное понижение относительного удлинения и повышение предела прочности при растяжении. Показатели ударной вязкости при этом резко падают в связи с наличием структурно свободных силицидов магния, происходит охрупчивание феррита, в особенности для чугуна ВЧ40.
Влияние марганца аналогично влиянию кремния. Резкое падение ударной вязкости и значительное снижение относительного удлинения наступает при содержании марганца более 0,6% (рис.6).
Влияние фосфора на понижение пластичности и вязкости ВЧ заметно проявляется при содержании его выше 0,08% (рис.7).
Получение чугунов марок ВЧ40, ВЧ45, ВЧ50, ВЧ60 вполне осуществимо в вагранках при правильном подборе модификаторов.
Многие сомневались в возможности получения ВЧ40 из вагранки на холодном дутье, обеспечивающей нагрев чугуна лишь до 1360-кС. Подтверждением стали сравнительные опыты получения ВЧ в индукционных и дуговых электропечах, а также в вагранке производительностью 3т/ч. Во всех плавках использовались одни и те же шихтовые материалы, поэтому полученный металл был практически одинакового химического состава. Отличие состояло лишь в том, что чугун в индукционной и дуговой электропечах нагревался до 1450-1500-кС, а в вагранке до 1360-кС. В связи с этим температура ваграночного чугуна при заливке в формы была 1280-1300-кС, а электропечного чугуна — 1340-1380-кС. Результаты механических испытаний полученного ВЧ (после отжига), приведенные в таблице 1, показывают, что чугун выплавленный в индукционной и дуговой электропечи имеет более высокие показатели относительного удлинения и ударной вязкости, что связано с повышенной температурой заливки и низким содержанием серы. Остальные характеристики механических свойств вполне удовлетворяют требованиям ГОСТа и для ваграночного чугуна.
При выплавке чугуна марок ВЧ40, ФЧ45, ВЧ50, ВЧ60 использовались обычные передельные чугуны ПЛ1 и ПЛ2, с пониженным содержанием фосфора и марганца.
Таблица 1
вфЖ п/п | Плавильный агрегат | Механические свойства | |||
σв , МПа | -д, % | KCU , кДж/м2 | HB , ГПа | ||
1 | Индукционная печь | 470 | 18 | 990 | 170 |
2 | Индукционная печь | 510 | 16 | 980 | 170 |
3 | Индукционная печь | 55 | 22,2 | 124 | 18 |
Среднее | 51 | 18,7 | 1070 | 175,7 | |
4 | Дуговая печь | 535 | 18,1 | 1150 | 174 |
5 | Дуговая печь | 523 | 24,8 | 1050 | 174 |
6 | Дуговая печь | 544 | 18,4 | 860 | 174 |
7 | Дуговая печь | 531 | 19 | 950 | 174 |
Среднее | 533,3 | 20,7 | 1002,5 | 174 | |
8 | Вагранка | 553 | 6,9 | 450 | 187 |
9 | Вагранка | 540 | 15,4 | 550 | 170 |
10 | Вагранка | 540 | 18,5 | 430 | 175 |
11 | Вагранка | 507 | 13,8 | 710 | 192 |
12 | Вагранка | 487 | 20,6 | 670 | 160 |
Среднее | 525,4 | 15 | 562 | 174 |
Опытами установлено, что при производстве отливок из ВЧ40 содержание хрома в шихте не должно быть более 0,1%; для всех других марок — содержание остаточного хрома допустимо до 0,2%.
Весь кремний, вводимый с кремнистыми модификаторами, практически полностью переходит в чугун, что следует учитывать при расчете шихты.
Для обеспечения повышенного содержания углерода в чугуне до его модифицирования, стальной лом в шихте следует применять не более 15-20%. Чугунный лом может использоваться в любом количестве, но при условии обеспечения требуемого химического состава чугуна.
При разливке металла в формы должны быть приняты меры предупреждающие образование «черных пятен», являющихся наиболее распространенным видом дефектов в отливках из ВЧ. В результате введения магниевой лигатуры значительная часть углерода (от 0,2 до 0,8%) переходит в шлак. Установлено, что «черные пятна» являются преимущественно скоплениями сульфидов магния и графита. На серных отпечатках они представляются в виде резко затемненных пятен — следов разложившихся при изготовлении шлифа сульфидов магния (рис.8 и 9).
При химическом анализе в местах «черных пятен» обнаруживается повышенное содержание углерода и серы (таблица 2).
Таблица 2
вфЖ п/п | «черное пятно» | чистый металл | ||
содержание, % | ||||
C | S | C | S | |
1 | 3 ,78 | 0,16 | 2,83 | 0,009 |
2 | 3,68 | 0,188 | 2,48 | 0,01 |
3 | 4,88 | 0,041 | 3,0 | 0,01 |
В качестве мер борьбы с дефектами отливок в виде «черных пятен» можно рекомендовать различные способы: повышение температуры заливки, обработка жидкого металла флюсами (карбонат натрия, «рефлой» и т.д.).Все эти способы уменьшают, но не устраняют полностью возможность образования «черных пятен» в отливках. Кроме того, каждый из них имеет отрицательные стороны, которые могут привести к неудовлетворительным результатам в отношении формы графита и механических свойств чугуна.
Для борьбы с «черными пятнами» можно использовать заливку ковшами с сифонной подачей металла в формы. Опыт показал, что для разливки металла больше одной тонны с успехом можно применять обычные стопорные ковши.
Снятием серных отпечатков с темплетов, залитых с применением сифонных или стопорных ковшей, было установлено полное отсутствие «черных пятен».
Весьма важным фактором, определяющим качество отливок из ВЧ, является установление оптимальной температуры заливки.
Были проведены опыты по изготовлению отливок различной толщины стенок, залитых при температурах 1250, 1280 и 1370-кС. Температура заливки оказывает значительное влияние на показатели относительного удлинения. Характеристики прочности при этом не изменяются. Данные рис.10 показывают, что влияние температуры заливки с уменьшением толщины стенки отливки возрастает. Оптимальной температурой заливки ВЧ следует считать 1320-1340-кС. Применение более высокой температуры заливки нецелесообразно, потому что это приводит к понижению усвоения магния, вследствие чего механические свойства чугуна получаются менее стабильными.
Список литературы:
1. Шапранов И.А. О кристаллизации и механических свойствах высокопрочного чугуна с шаровидным графитом. В сб. Новое в теории и практике литейного производства. — М-Л., Машгиз, 1956. — С. 312-319.
2. Гиршович Н.Г. Кристаллизация и свойства чугуна в отливках. — Л., Машиностроение, 1966.
3. Кривошеев А.Е., Маринченко Б.В., Фетисов Н.М. Механические свойства чугуна с шаровидным графитом в отливках // Литейное производство. 1972, вфЖ5. — С. 34-35.
4. Захарченко Э.В., Левченко Ю.Н., Горенко В.Г., Вареник П.А. Отливки из чугуна с шаровидным и вермикулярным графитом. — Киев, Наукова думка, 1986.