Какие бывают свойства механизмов
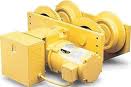
Кулачко́вый механи́зм — механизм, образующий высшую кинематическую пару, имеющий подвижное звено, совершающее вращательное движение, — кулак (кулачок), с поверхностью переменной кривизны или имеющей форму эксцентрика, взаимодействующей с другим подвижным звеном — толкателем, если подвижное звено совершает прямолинейное движение, или коромыслом, если подвижное звено совершает качание. Кулак, совершающий прямолинейное движение, называется копиром.
Классификация[править | править код]
Кулачковые механизмы подразделяют на 4 группы:
- По типу толкателя:
- с плоским толкателем,
- с тарельчатым,
- с роликовым (на рисунке),
- с игольчатым,
- с остроконечным.
- По характеру движения толкателя:
- возвратно-поступательное (на рисунке),
- качающееся.
- По характеру движения кулачка:
- возвратно-поступательное,
- качающееся,
- вращающееся (на рисунке).
- Кулачковые механизмы с роликовым толкателем бывают:
- дезаксиальные (ось кулачка не под толкателем),
- центральные (ось кулачка под толкателем) (на рисунке).
Особенности[править | править код]
Основные характеристики кулачкового механизма — это максимальное перемещение толкателя (угол качания коромысла), максимальная скорость или ускорение исполнительного механизма и закон движения исполнительного механизма.
Закон движения разных типов и размеров толкателя на одном и том же кулачке отличается, поэтому расчёт профиля кулачка ведётся под конкретный толкатель.
Кулачковый механизм имеет сходные черты с механизмом планшайба-стержни
Главным достоинством и исключительным свойством кулачкового механизма является возможность реализации произвольного (в очень широких пределах) закона движения исполнительного механизма.
Вторым достоинством является простота конструкции, благодаря чему кулачковый механизм иногда используют как простейший преобразователь вращательного движения в возвратно-поступательное, например, в приводе бензонасоса карбюраторных ДВС.
Главным недостатком является дороговизна изготовления профилей. Эта задача решается применением литья, либо перемещением обрабатывающего органа по шаблону, то есть, по сути, также использованием кулачкового механизма (в станке).
Вторым недостатком является относительно малая нагрузочная способность, вследствие трения скольжения кулачка и толкателя по линии, а также из-за значительных боковых усилий на толкатель при резких перемещениях. Для повышения ресурса применяют роликовый толкатель (как правило, на игольчатом подшипнике) и замену поступательного толкателя коромыслом, например, в газораспределительном механизме тракторных дизелей.
Применение[править | править код]
Кулачковый механизм применяется:
- в газораспределительном механизме ДВС;
- в топливных насосах высокого давления дизелей;
- в топливных насосах автомобильных карбюраторных двигателей;
- в механическом (пневматическом) приводе колодочных тормозов (грузовики, тракторы);
- в прерывателе контактной системы зажигания бензиновых ДВС;
- в приводе воздушной заслонки карбюраторов (автомобиль ОКА);
- в механизмах переключения коробок передач мотоциклов;
- в швейных машинках (механические переключатели режимов, варианты движения рабочих органов);
- в шарманках и музыкальных шкатулках (вырожденный кулачок — шип — только включает звук в определённый момент);
- в механических (часовых) таймерах и реле времени;
- в металлорежущих станках;
- и многих других машинах для воспроизведения сложной траектории движения рабочих органов и выполнения функций управления, таких, как включение и выключение рабочих органов по определённой схеме.
См. также[править | править код]
- Кулак (техника)
Литература[править | править код]
- Под ред. А. Ю. Ишлинского. Новый политехнический словарь. — М.: Большая Российская энциклопедия, 2003. — С. 671. — ISBN 5-7107-7316-6.
Ïðè ïðîåêòèðîâàíèè ýëåêòðîïðèâîäà ýëåêòðîäâèãàòåëü äîëæåí âûáèðàòüñÿ òàê, ÷òîáû åãî ìåõàíè÷åñêèå õàðàêòåðèñòèêè ñîîòâåòñòâîâàëè ìåõàíè÷åñêèì õàðàêòåðèñòèêàì ïðîèçâîäñòâåííîãî ìåõàíèçìà. Ìåõàíè÷åñêèå õàðàêòåðèñòèêè äàþò âçàèìîñâÿçü ïåðåìåííûõ â óñòàíîâèâøèõñÿ ðåæèìàõ.
Ìåõàíè÷åñêîé õàðàêòåðèñòèêîé ìåõàíèçìà íàçûâàþò çàâèñèìîñòü ìåæäó óãëîâîé ñêîðîñòüþ è ìîìåíòîì ñîïðîòèâëåíèÿ ìåõàíèçìà, ïðèâåäåííûìè ê âàëó äâèãàòåëÿ) ω = f(Mñ).
Ðèñ. 1. Ìåõàíè÷åñêèå õàðàêòåðèñòèêè ìåõàíèçìîâ
Ñðåäè âñåãî ìíîãîîáðàçèÿ âûäåëÿþò íåñêîëüêî õàðàêòåðíûõ òèïîâ ìåõàíè÷åñêèõ õàðàêòåðèñòèê ìåõàíèçìîâ:
1. Õàðàêòåðèñòèêà ñ ìîìåíòîì ñîïðîòèâëåíèÿ, íå çàâèñÿùèì îò ñêîðîñòè (ïðÿìàÿ 1 íà ðèñ. 1). Íåçàâèñèìàÿ îò ñêîðîñòè ìåõàíè÷åñêàÿ õàðàêòåðèñòèêà ãðàôè÷åñêè èçîáðàæàåòñÿ ïðÿìîé, ïàðàëëåëüíîé îñè âðàùåíèÿ, â äàííîì ñëó÷àå âåðòèêàëüþ. Òàêîé õàðàêòåðèñòèêîé îáëàäàþò, íàïðèìåð, ïîäúåìíûå êðàíû, ëåáåäêè, ïîðøíåâûå íàñîñû ïðè íåèçìåííîé âûñîòå ïîäà÷è è äð.
2. Õàðàêòåðèñòèêà ñ ìîìåíòîì ñîïðîòèâëåíèÿ ëèíåéíî çàâèñÿùèì îò ñêîðîñòè (ïðÿìàÿ 2 íà ðèñ. 1). Òàêàÿ çàâèñèìîñòü ïðèñóùà, íàïðèìåð, ïðèâîäó ãåíåðàòîðà ïîñòîÿííîãî òîêà ñ íåçàâèñèìûì âîçáóæäåíèåì, ðàáîòàþùåìó íà ïîñòîÿííóþ íàãðóçêó.
3. Õàðàêòåðèñòèêà ñ íåëèíåéíûì âîçðàñòàíèåì ìîìåíòà (êðèâàÿ 3 íà ðèñ. 1). Òèïè÷íûìè ïðèìåðàìè åìîãóò ñëóæèòü õàðàêòåðèñòèêè âåíòèëÿòîðîâ, öåíòðîáåæíûõ íàñîñîâ, ãðåáíûõ âèíòîâ. Äëÿ ýòèõ ìåõàíèçìîâ ìîìåíò Ìñ çàâèñèò îò êâàäðàòà óãëîâîé ñêîðîñòè ω. Ýòî ò.í. ïàðàáîëè÷ñêàÿ (âåíòèëÿòîðíàÿ) ìåõàíè÷åñêàÿ õàðàêòåðèñòèêà.
4. Õàðàêòåðèñòèêà ñ íåëèíåéíî ñïàäàþùèì ìîìåíòîì ñîïðîòèâëåíèÿ (êðèâàÿ 4 íà ðèñ. 1). Çäåñü ìîìåíò ñîïðîòèâëåíèÿ îáðàòíî ïðîïîðöèîíàëåí ñêîðîñòè âðàùåíèÿ. Ìîùíîñòü â ýòîì ñëó÷àå îñòàåòñÿ ïîñòîÿííîé íà âñåì äèàïàçîíå ðàáî÷åé ñêîðîñòè ìåõàíèçìà. Íàïðèìåð, ó ìåõàíèçìîâ ãëàâíîãî äâèæåíèÿ íåêîòîðûõ ìåòàëëîðåæóùèõ ñòàíêîâ (òîêàðíûõ, ôðåçåðíûõ, ðàñòî÷íûõ) ìîìåíò Ìñ èçìåíÿåòñÿ îáðàòíî ïðîïîðöèîíàëüíî ω, à ìîùíîñòü ïîòðåáëÿåìàÿ ìåõàíèçìîì, îñòàåòñÿ ïîñòîÿííîé.
Ìåõàíè÷åñêîé õàðàêòåðèñòèêîé ýëåêòðîäâèãàòåëÿ íàçûâàåòñÿ çàâèñèìîñòü åãî óãëîâîé ñêîðîñòè îò âðàùàþùåãî ìîìåíòà ωä = f(M).Çäåñü ñëåäóåò èìåòü ââèäó, ÷òî ìîìåíò Ì íà âàëó äâèãàòåëÿ íåçàâèñèìî îò íàïðàâëåíèÿ âðàùåíèÿ èìååò ïîëîæèòåëüíûé çíàê — ìîìåíò äâèæóùèé. Âìåñòå ñ òåì ìîìåíò ñîïðîòèâëåíèÿ Ìñ èìååò çíàê îòðèöàòåëüíûé.
 êà÷åñòâå ïðèìåðîâ íà ðèñ. 2 ïðèâåäåíû ìåõàíè÷åñêèå õàðàêòåðèñòèêè: 1 — ñèíõðîííîãî äâèãàòåëÿ; 2 äâèãàòåëÿ ïîñòîÿííîãî òîêà íåçàâèñèìîãî âîçáóæäåíèÿ; 3 äâèãàòåëÿ ïîñòîÿííîãî òîêà ïîñëåäîâàòåëüíîãî âîçáóæäåíèÿ.
Ðèñ. 2. Ìåõàíè÷åñêèå õàðàêòåðèñòèêè ýëåêòðîäâèãàòåëåé
Äëÿ îöåíêè ñâîéñòâ ìåõàíè÷åñêèõ õàðàêòåðèñòèê ýëåêòðîïðèâîäà èñïîëüçóþò ïîíÿòèå æåñòêîñòè õàðàêòåðèñòèêè. Æåñòêîñòü ìåõàíè÷åñêîé õàðàêòåðèñòèêè îïðåäåëÿåòñÿ ïî âûðàæåíèþ
β = dÌ /dω
ãäå dÌ èçìåíåíèå ìîìåíòà äâèãàòåëÿ; dωä ñîîòâåòñòâóþùåå èçìåíåíèå óãëîâîé ñêîðîñòè.
Äëÿ ëèíåéíûõ õàðàêòåðèñòèê çíà÷åíèå β îñòàåòñÿ ïîñòîÿííûì, äëÿ íåëèíåéíûõ çàâèñèò îò ðàáî÷åé òî÷êè.
Èñïîëüçóÿ ýòî ïîíÿòèå, õàðàêòåðèñòèêè, ïðèâåäåííûå íà ðèñ. 2, ìîæíî êà÷åñòâåííî îöåíèòü òàê: 1 àáñîëþòíî æåñòêàÿ (β = ∞); 2 æåñòêàÿ; 3 ìÿãêàÿ.
Àáñîëþòíî æåñòêàÿ õàðàêòåðèñòèêà — ñêîðîñòü âðàùåíèÿ äâèãàòåëÿ îñòàåòñÿ íåèçìåííîé ïðè èçìåíåíèè íàãðóçêè äâèãàòåëÿ â ïðåäåëàõ îò íóëÿ äëÿ íîìèíàëüíîé. Òàêîé õàðàêòåðèñòèêîé îáëàäàþò ñèíõðîííûå äâèãàòåëè.
Æåñòêàÿ õàðàêòåðèñòèêà — ñêîðîñòü âðàùåíèÿ ìåíÿåòñÿ íåçíà÷èòåëüíî ïðè èçìåíåíèè íàãðóçêè îò íóëÿ äî íîìèíàëüíîé. Òàêîé õàðàêòåðèñòèêîé îáëàäàåò äâèãàòåëü ïîñòîÿííîãî òîêà ñ ïàðàëëåëüíûì âîçáóæäåíèåì, à òàêæå àñèíõðîííûé äâèãàòåëü â îáëàñòè ëèíåéíîé ÷àñòè õàðàêòåðèñòèêè.
Æåñòêîé õàðàêòåðèñòèêîé ïðèíÿòî ñ÷èòàòü òàêóþ, ó êîòîðîé èçìåíåíèå ñêîðîñòè íå ïðåâûøàåò ïðèáëèçèòåëüíî 10% íîìèíàëüíîé ñêîðîñòè ïðè èçìåíåíèè íàãðóçêè îò íóëÿ äî íîìèíàëüíîé.
Ìÿãêàÿ õàðàêòåðèñòèêà — ñêîðîñòü âðàùåíèÿ äâèãàòåëÿ ìåíÿåòñÿ çíà÷èòåëüíî ïðè ñðàâíèòåëüíî íåáîëüøèõ èçìåíåíèÿõ íàãðóçêè. Òàêîé õàðàêòåðèñòèêîé îáëàäàåò äâèãàòåëü ïîñòîÿííîãî òîêà ñ ïîñëåäîâàòåëüíûì, ñìåøàííûì èëè ñ ïàðàëëåëüíûì âîçáóæäåíèåì, íî ñ äîáàâî÷íûì ñîïðîòèâëåíèåì â öåïè ÿêîðÿ, à òàêæå àñèíõðîííûé ñ ñîïðîòèâëåíèåì â öåïè ðîòîðà.
Äëÿ áîëüøèíñòâà ïðîèçâîäñòâåííûõ ìåõàíèçìîâ èñïîëüçóþò àñèíõðîííûå äâèãàòåëè ñ êîðîòêîçàìêíóòûì ðîòîðîì, èìåþùèå æåñòêóþ ìåõàíè÷åñêóþ õàðàêòåðèñòèêó.
Âñå ìåõàíè÷åñêèå õàðàêòåðèñòèêè ýëåêòðîäâèãàòåëåé äåëÿòñÿ íà åñòåñòâåííûå è èñêóññòâåííûå.
Åñòåñòâåííàÿ ìåõàíè÷åñêàÿ õàðàêòåðèñòèêà îòíîñèòñÿ ê óñëîâèÿì ðàáîòû äâèãàòåëÿ ñ íîìèíàëüíûìè çíà÷åíèÿìè ïàðàìåòðîâ.
Íàïðèìåð, äëÿ äâèãàòåëÿ ñ ïàðàëëåëüíûì âîçáóæäåíèåì åñòåñòâåííàÿ õàðàêòåðèñòèêà ìîæåò áûòü ïîñòðîåíà äëÿ ñëó÷àÿ, êîãäà íàïðÿæåíèå íà ÿêîðå è òîê âîçáóæäåíèÿ èìåþò íîìèíàëüíûå çíà÷åíèÿ, à â öåïè ÿêîðÿ îòñóòñòâóåò äîáàâî÷íîå ñîïðîòèâëåíèå.
Åñòåñòâåííàÿ õàðàêòåðèñòèêà àñèíõðîííîãî äâèãàòåëÿ ñîîòâåòñòâóåò íîìèíàëüíîìó íàïðÿæåíèþ è íîìèíàëüíîé ÷àñòîòå ïåðåìåííîãî òîêà, ïîäâîäèìîãî ê ñòàòîðó äâèãàòåëÿ ïðè óñëîâèÿ îòñóòñòâèÿ äîáàâî÷íîãî ñîïðîòèâëåíèÿ â öåïè ðîòîðà.
Òàêèì îáðàçîì, äëÿ êàæäîãî äâèãàòåëÿ åñòåñòâåííàÿ õàðàêòåðèñòèêà ìîæåò áûòü ïîñòðîåíà òîëüêî îäíà, à èñêóññòâåííûõ — íåîãðàíè÷åííîå êîëè÷åñòâî. Íàïðèìåð, êàæäîìó íîâîìó çíà÷åíèþ ñîïðîòèâëåíèÿ ÿêîðÿ äâèãàòåëÿ ïîñòîÿííîãî òîêà èëè â öåïè ðîòîðà àñèíõðîííîãî äâèãàòåëÿ îòâå÷àåò ñâîÿ ìåõàíè÷åñêàÿ õàðàêòåðèñòèêà.
Текущая версия страницы пока не проверялась опытными участниками и может значительно отличаться от версии, проверенной 26 мая 2017;
проверки требуют 7 правок.
Лыжная мазь «Висти» советского производства в фирменной упаковке
Сма́зочные материа́лы — твёрдые, пластичные, жидкие и газообразные вещества, используемые в узлах трения автомобильной техники, промышленных машин и механизмов, а также в быту для снижения износа, вызванного трением.
Назначение и роль смазочных материалов (смазок и масел) в технике[править | править код]
Смазочные материалы широко применяются в современной технике, с целью уменьшения трения в движущихся механизмах (двигатели, подшипники, редукторы, и.т д), и с целью уменьшения трения при механической обработке конструкционных и других материалов на станках (точение, фрезерование, шлифование и т. д.). В зависимости от назначения и условий работы смазочных материалов (смазок), они бывают твёрдыми (графит, дисульфид молибдена, иодид кадмия, диселенид вольфрама, нитрид бора гексагональный и т. д.), полутвёрдыми, полужидкими (расплавленные металлы, солидолы, консталины и др), жидкими (автомобильные и другие машинные масла), газообразными (углекислый газ, азот, инертные газы).
Виды и типы смазочных материалов[править | править код]
В зависимости от характеристик материалов кинематической пары, для смазки могут быть использованы жидкие (например, минеральные, синтетические и полусинтетические масла) и твёрдые (фторопласт, графит, дисульфид молибдена) вещества.
По материалу основы смазки делятся на:
- минеральные — в их основе лежат углеводороды, продукты переработки нефти
- синтетические — получаются путём синтеза из органического и неорганического (например, силиконовые смазки) сырья
- органические — имеют растительное происхождение (например: касторовое масло, пальмовое масло)
Смазки могут иметь комбинированную основу.
Классификация[править | править код]
Все жидкие смазочные материалы делятся на классы по вязкости (классификация SAE для моторных и трансмиссионных масел, классификация ISO VG (viscosity grade) для промышленных масел), и на группы по уровню эксплуатационных свойств (классификации API, ACEA для моторных и трансмиссионных масел, классификация ISO для промышленных масел).
По агрегатному состоянию делятся на:
- твёрдые,
- полутвёрдые,
- полужидкие,
- жидкие,
- газообразные.
По назначению:
- Моторные масла — применяемые в двигателях внутреннего сгорания.
- Трансмиссионные и редукторные масла — применяемые в различных зубчатых передачах и коробках передач.
- Гидравлические масла — применяемые в качестве рабочей жидкости в гидравлических системах.
- Пищевые масла и жидкости — применяемые в оборудовании для производства пищи и упаковки, где возможен риск загрязнения продуктов смазывающим веществом.
- Промышленные масла (текстильные, для прокатных станов, закалочные, электроизоляционные, теплоносители и многие другие) — применяемые в самых разнообразных машинах и механизмах с целью смазывания, консервации, уплотнения, охлаждения, выноса отходов обработки и др.
- Электропроводящие смазки (пасты) — применяемые для защиты электрических контактов от коррозии и снижения переходного сопротивления контактов. Электропроводящие смазки изготавливаются консистентными.
- Консистентные (пластичные) смазки — применяемые в тех узлах, в которых конструктивно невозможно применение жидких смазочных материалов.
См. также[править | править код]
- Смазочно-охлаждающие жидкости
- Трибология
- Лубрикант
- Eurol B.V.
- Фторопласты
- Нефтяные масла
- Твердые технологические смазки
Ссылки[править | править код]
- Ильченко Андрей. Смазывание подшипников качения. 2008
- API 1509, Engine Oil Licensing and Certification System, 15th Edition, 2002. Appendix E, API Base Oil Interchangeability Guidelines for Passenger Car Motor Oils and Diesel Engine Oils (revised) (англ.)
- Справочник по смазочным материалам (рус.)
- Boughton and Horvath, 2003, Environmental Assessment of Used Oil Management Methods, Environmental Science and Technology, V38 (англ.)
- I.A. Inman. Compacted Oxide Layer Formation under Conditions of Limited Debris Retention at the Wear Interface during High Temperature Sliding Wear of Superalloys, Ph.D. Thesis (2003), Northumbria University ISBN 1-58112-321-3
- Mercedes-Benz oil recommendations, extracted from factory manuals and personal research (англ.)
- Lubricant Additives: Chemistry and Applications, Leslie R. Rudnick, CRC Press (англ.)
Прочность деревянного кузова DKW F8, 1939. На едущем автомобиле стоят не менее 28 человек
Про́чность (в физике и материаловедении) — свойство материала сопротивляться разрушению под действием напряжений, возникающих под воздействием внешних сил.
Свойство конструкции выполнять назначение, не разрушаясь в течение заданного времени.
Классификация[править | править код]
Прочность подразделяют на статическую, под действием постоянных нагрузок, динамическую и усталостную (выносливость), имеющую место при действии циклических переменных нагрузок.
Для конструкций различают общую прочность — способность всей конструкции выдерживать нагрузки без разрушения, и местную — та же способность отдельных узлов, деталей, соединений.
Количественное рассмотрение[править | править код]
В настоящее время при расчёте на прочность используют как расчёт по допускаемым напряжениям, так и расчёт по допускаемому числу циклов нагружения. Основные неравенства расчёта по допускаемым напряжениям:
где
Прикладное применение[править | править код]
Обеспечение прочности машин, аппаратов и конструкций осуществляется следующим образом. На стадии их проектирования производится расчётная или экспериментальная оценка возможности развития в несущих элементах проектируемых конструкций процессов разрушений различных типов: усталостного, хрупкого, квазистатического, разрушения вследствие ползучести материала, коррозии, износа в процессе эксплуатации и т. п. При этом должны быть рассмотрены все возможные в условиях эксплуатации конструкции, известные на данный момент механизмы разрушения материала, из которого выполнены её несущие элементы. Для вновь создаваемого класса машин или аппаратов указанные механизмы разрушения выявляются на стадии научно-исследовательского цикла проектирования. С каждым из таких механизмов разрушения связывается определённый критерий прочности — та или иная характеристика физического состояния материала элементов машин и аппаратов, определяемая расчётным или экспериментальным путём. Для каждого из критериев прочности материала конструкции экспериментально устанавливаются его предельные значения. По предельным значениям далее определяются допускаемые значения этих критериев. Последние определяются, как правило, путём деления предельных значений критерия прочности на соответствующий коэффициент запаса прочности. Значения коэффициентов запаса прочности назначаются на основе опыта эксплуатации с учётом степени ответственности проектируемой конструкции, расчётного срока её эксплуатации и возможных последствий её разрушения.
Значения коэффициентов запаса прочности для различных механизмов разрушения различны. При расчёте по допускаемым напряжениям они изменяются, как правило, в диапазоне значений от 1,05 (при обеспечении прочности элементов летательных аппаратов, имеющих краткий жизненный цикл и не предназначенных для транспортировки людей) до 6 (при обеспечении прочности тросов, используемых в конструкциях пассажирских лифтов). При расчёте по допускаемому числу циклов нагружения могут использоваться существенно большие значения этих коэффициентов. Расчёт наиболее ответственных и энергонасыщенных конструкций машин и аппаратов регламентируется отраслевыми нормами и стандартами. По мере накопления опыта эксплуатации, развития методов исследования физического состояния конструкций и совершенствования методов обеспечения прочности эти нормы и стандарты периодически пересматриваются.
Разрушения[править | править код]
Хрупкое и вязкое разрушение имеют разные виды разрушенной поверхности. Характер дефектов дает понятие, какого рода разрушение имеет место. При хрупком разрушении поверхность надломлена. При вязком разрушении поверхность натянута (вяжет разрушение).
Вязкость разрушения — это относительное повышение растягивающих напряжений в устье трещины при переходе её от стабильной к нестабильной стадии роста.[1]
Вязкость разрушения тесно связана с показателями прочности материала. Увеличение прочности сопровождается снижением пластичности и вязкости разрушения. Это объясняется тем, что у высокопрочных материалов мала энергия, поглощаемая при разрушении, уровень которой определяется величиной пластической деформации у вершины трещины. Для высокопрочных материалов эффект увеличения прочности существенно перекрывается снижением пластичности, в результате чего вязкость разрушения уменьшается. Материалы средней и низкой прочности при комнатной температуре обычно имеют более высокие значения, чем высокопрочные. С понижением температуры прочность растет и при определённых условиях поведение материала средней и низкой прочности становится таким же, как у высокопрочного материала при комнатной температуре. При низких температурах испытание вязкости разрушения можно проводить на образцах меньших размеров.
Современные методы расчета[править | править код]
Для расчёта напряженно-деформируемого состояния конструкции и определения её прочности применяются современные наукоемкие технологии — системы компьютерного инженерного анализа, основанные на применении сеточных методов решения задач математической физики. В настоящее время одним из наиболее эффективных и универсальных методов этого класса является метод конечных элементов (МКЭ).
Наиболее распространённые системы КЭ анализа:
ANSYS — универсальная система КЭ анализа с встроенным пре-/постпроцессором;
MSC.Nastran — универсальная система КЭ анализа с пре-/постпроцессором;
ABAQUS — универсальная система КЭ анализа с встроенным пре-/постпроцессором;
NEiNastran — универсальная система КЭ анализа с пре-/постпроцессором FEMAP;
NX Nastran — универсальная система КЭ анализа с пре-/постпроцессором FEMAP.
ПК ЛИРА-САПР — система КЭ анализа строительных и машиностроительных конструкций.
Примечания[править | править код]
Ссылки[править | править код]
- Джеймс Гордон «Конструкции, или почему не ломаются вещи