Что такое коксование какие продукты получают при коксовании
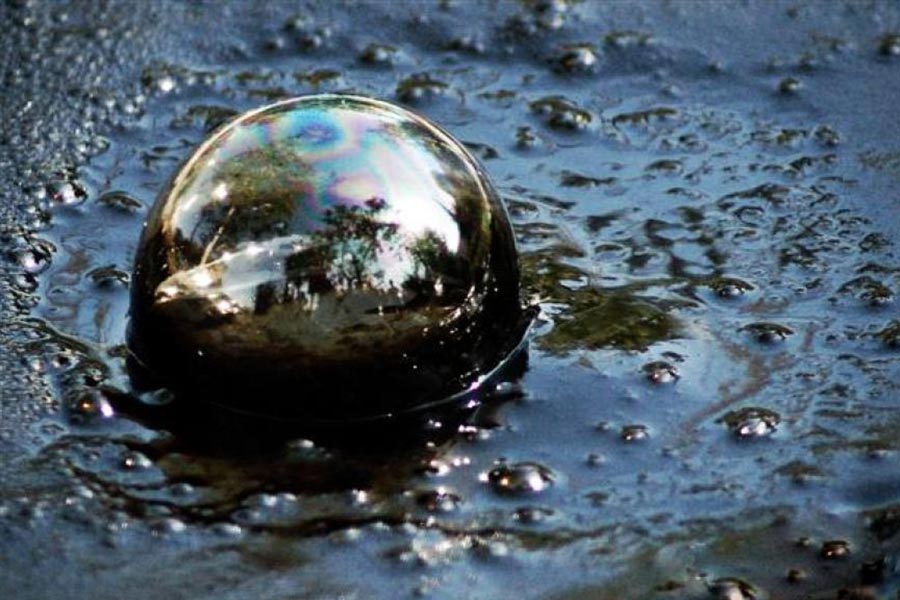
Кокс представляет собой твердый матово-черный, пористый продукт. Из тонны сухой шихты получают 650-750 кг кокса. Он используется главным образом в металлургии, а также для газификации, производства карбида кальция, электродов, как реагент и топливо в ряде отраслей химической промышленности. Широкое применение кокса в металлургии определяет основные предъявляемые к нему требования:
1. Кокс должен обладать достаточной механической прочностью, так как в противном случае он будет разрушаться в металлургических печах под давлением столба шихты, что увеличит сопротивление движению газов, приведет к расстройству работы доменной печи, снижению ее производительности и т.п.
2. Кокс должен иметь теплотворную способность 31400-33500 кДж/кг.
3. Иметь высокую реакционную способность и горючесть. Первый показатель характеризует скорость восстановления коксом диоксида углерода, второй – скорость горения кокса.
4. Качество кокса также характеризуется содержанием в нем золы, серы, влаги и выходом летучих веществ. Сера, содержащаяся в коксе, при доменной плавке переходит в чугун, ухудшая его качество. Допустимое содержание серы в коксе 1.2-1.7 %. Зола в коксе – это балласт, и содержание ее равно примерно 10.0-11.0 %. Выход летучих веществ из кокса составляет около 1.0 %. Увеличение влажности кокса понижает его теплотворную способность, в коксе допустимо до 5 % влаги.
Коксовый газ получается в количестве 310-340 м3 на 1 т сухого угля. Состав и выход коксового газа определяется главным образом температурой коксования. Из камеры, в которой происходит коксование, выходит так называемый прямой коксовый газ, содержащий газообразные продукты, пары каменноугольной смолы, сырого бензола и воды. После удаления из него смолы, сырого бензола, воды и аммиака получается так называемый обратный коксовый газ, который используется как сырье для химических синтезов. Помимо этого, коксовый газ применяется как промышленное топливо для обогрева коксовых, сталеплавильных и других печей.
Каменноугольная смола – вязкая черно-бурая, со специфическим запахом жидкость, содержащая около 300 различных веществ. Наиболее ценными компонентами смолы являются ароматические и гетероциклические соединения: бензол, толуол, ксилолы, фенол, крезол, нафталин, антрацен, фенантрен, пиридин, карбазол, кумарон и др. Плотность смолы 1.17-1.20 г/см3. Выход смолы составляет от 3 до 4 % от массы коксуемого сухого угля. Состав смолы зависит главным образом от температуры коксования, а выход – от температуры и природы исходных углей. С повышением температуры углубляется пиролиз углеводородов, что снижает выход смолы и увеличивает выход газа.
В настоящее время из каменноугольной смолы выделяют около двухсот продуктов различных наименований, куда входят смеси и индивидуальные вещества, служащие сырьем для синтеза красителей, фармацевтических препаратов, инсектофунгицидов, пластических масс, химических волокон и т.п.
Сырой бензол – это смесь, состоящая из сероуглерода, бензола, толуола, ксилолов, кумарона и других веществ. Выход сырого бензола составляет в среднем 1.1 % от количества угля. Выход зависит от состава и свойств исходного угля и температурных условий процесса. При разгонке из сырого бензола получают индивидуальные ароматические углеводороды и смеси углеводородов, служащие сырьем для химической промышленности. Сырой бензол и смола, получаемые при коксовании углей, несмотря на развитие нефтехимического синтеза служат главнейшими источниками ароматических углеводородов для химической промышленности.
Надсмольная вода представляет собой слабый водный раствор аммиака и аммонийных солей с примесью фенола, пиридиновых оснований и некоторых других продуктов. Из надсмольной воды при ее переработке выделяется аммиак, который совместно с аммиаком коксового газа используется для получения сульфата аммония и концентрированной аммиачной воды.
Разделение продуктов коксования
Сначала производят разделение прямого коксового газа. Из него конденсируют смолу и воду, улавливают аммиак, сырой бензол и сероводород. Затем подвергают разделению надсмольную воду, каменноугольную смолу и сырой бензол с получением индивидуальных веществ или их смесей (рис. 1.6).
Рис. 1.2.3.1.1. Технологическая схема переработки прямого коксового газа
Прямой коксовый газ представляет сложную смесь газообразных и парообразных веществ. Помимо водорода, метана, этилена и других углеводородов, оксида и диоксида углерода, азота, в 1 м3 газа (при 0 оС и 105 Па) содержится 80-130 г смолы, 8-13 г аммиака, 30-40 г бензольных углеводородов, 6-25 г сероводорода и других сернистых соединений, 0.5-1.5 г цианистого водорода, 250-450 г паров воды и твердых частиц. Газ выходит из коксовой печи при 700 оС. Процесс разделения прямого коксового газа начинается в газосборнике 2, в который интенсивно впрыскивается холодная вода. Из газа удаляются твердые частицы (уголь, коксовая пыль, зола) и каменноугольная смола. Смола и надсмольная вода после охлаждения в холодильнике 3 стекают в в сборник 4, где разделяются по плотности. Надсмольная вода, обогащенная хлоридом, сульфатом, роданидом, тиоцианом аммония, поступает в аппарат 5, в который сверху также подается 20 %-ный раствор гидроксида кальция, а снизу «острый» пар. Здесь идут реакции отделения аммиака:
2 NH4Cl + Ca(OH)2 = CaCl2 + 2 NH3 + 2 H2O
Аналогичным образом отделяют сероводород, циановодород, родановодород. Образовавшийся аммиак и аммиак, оставшийся в газе после холодильников, поступает в нейтрализатор колокольного типа 6, заполненный 10 %-ным раствором серной кислоты, которая при взаимодействии с аммиаком дает кристаллы сульфата аммония. Вместе с аммиаком в колонне 6 улавливаются пиридиновые основания с образованием сульфата пиридина. Кристаллы сульфата аммония вместе с маточным раствором выводят из колонны, отделяют от него центрифугированием в центрифуге 7 и используют как азотное удобрение.
Коксовый газ, очищенный от аммиака, направляется на улавливание сырого бензола. Наиболее распространенным методом улавливания сырого бензола является абсорбция его поглотительными маслами при 20-25 оС в скрубберах 9,10. В качестве поглотителей применяется каменноугольное или соляровое масло. Предварительно газ охлаждают водой в башне 8. При этом из газа вымываются нафталин и мельчайшие брызги серной кислоты, увлеченные из башни 6. Освобожденный от сырого бензола коксовый газ, так называемый обратный коксовый газ, в большинстве случаев очищается от сероводорода и других серосодержащих соединений и поступает потребителю. Раствор сырого бензола в поглотительном масле направляют в отпарочную колонну 12, где из него отгоняется сырой бензол, а масло после охлаждения возвращается на орошение скрубберов.
Надсмольная вода содержит растворенный аммиак, а также аммонийные соли (NH4)2CO3, (NH4)2S, NH4CN, NH4Cl, NH4SCN, (NH4)2SO4, образующиеся в результате взаимодействия аммиака с другими компонентами коксового газа при его охлаждении. Переработка надсмольной воды заключается в выделении из нее аммиака при нагревании ее паром и обработке известковым молоком. Аммиак отгоняется из надсмольной воды острым паром и используются для получения сульфата аммония. Фенолы, содержащиеся в надсмольной воде, также отгоняются острым паром, а затем поглощаются раствором едкого натра с образованием фенолятов.
Сырой бензол представляет собой сложную смесь, основная масса которой испаряется до 180 оС. Среднее содержание основных компонентов в сыром бензоле (%): сероуглерода и легкокипящих углеводородов 1.6-3.4; бензола 59.5-78.3; гомологов бензола 12-21; сольвентов (смесь триметилбензола, этилметилбензола и др.) 3-10. Получение отдельных компонентов из сырого бензола основано на различии их температур кипения и осуществляется ректификацией.
Каменноугольная смола содержит около 300 веществ. Содержание особо важных веществ в смоле (%): нафталина 5-10; фенантрена 4-6; карбазола 1-2; антрацена 0.5-1.5; фенола 0.2-0.5; крезола 0.6-1.2; пиридиновых оснований 0.5-1.5. Помимо этого, в смоле в небольших количествах содержатся бензольные углеводороды: бензол, толуол, ксилолы; около 50-60 % от массы смолы составляют высококипящие продукты с большой молекулярной массой. Смола подвергается разгонке, а затем из фракций ректификацией выделяются бензол и его гомологи, кристаллизацией – нафталин и антрацен. Фенол получается при обработке фракций раствором едкого натра с образованием фенолята натрия С6Н5ОNa, который при дальнейшем взаимодействии с диоксидом углерода дает фенол. Пиридиновые основания удаляются из фракций промывкой разбавленной серной кислотой. Остаток после перегонки смолы – каменноугольный пек используется для изготовления электродов для электролизеров и электрических печей, в дорожном строительстве как материал для изоляции электросетей и подземных трубопроводов.
Обратный коксовых газ имеет примерно следующий состав (об. %): водорода 54-59; метана 23-28; оксида углерода 5.0-7.0; тяжелых углеводородов 2-3; азота 3.0-5.0; диоксида углерода 1.5-2.5; кислорода 0.3-0.8. Теплотворная способность газа 16700-17200 кДж/м3.
Сырой бензол подвергают ректификации в колонне 14. При этом получают фракции: сероуглерод, бензол, толуол, о-ксилол, м-ксилол, п-ксилол, в кубе колонны остается сольвент-фракция. Фракции моют водой, обезвоживают и подвергают дальнейшей ректификации с целью получения сырья для органического и нефтехимического синтеза.
Метод очистки и использования коксового газа первым запатентовал немец Штилль в 1768 г. И все равно «вредный дух», выделяющийся при коксовании угля, считался отбросом производства. Более того, считалось, что он уменьшал выход столь нужного металлургам «хлеба» – кокса. Однако в XIX в. отношение к химическим продуктам коксования заметно изменилось.
В одной из сказок Андерсена некий школьный учитель мечтал о средневековых временах, когда, как ему казалось, многое было лучше, чем в меркантильном XIX в. Волей случая ему удалось надеть чудесные калоши, исполнявшие любые желания владельца. Они и перенесли нашего героя в средние века – в грязь, реки нечистот, текущих по темным, неосвещенным улицам. А жители крупных европейских городов уже в начале XIX в. привыкли к освещению на улицах, и этот свет дал газ, вырабатываемый из угля.
Вот, как описывает появление газового освещения известный наш популяризатор И. Ильин в книге «Солнце на столе».
«… Невесело было проводить вечера при тусклом свете сальных свечей или масляных ламп… Нашелся человек, которому пришло в голову, что горючий газ можно получать не в самой лампе, а на газовом заводе, откуда его можно в готовом виде проводить по трубам в горелку. А для приготовления газа он взял дешевый уголь. Звали этого человека Вильям Мердок. Это тот самый Мердок, который еще в конце XVIII века построил первый в Англии паровоз. Мердок был сначала рабочим, а потом инженером на первой фабрике паровых машин – фабрике Бультона и Уатта. При этой самой фабрике и построил Мердок первый в мире газовый завод.
Задача нелегкая – Мердок понимал, что для получения горючего газа надо уголь накалить. Но, если уголь накалить, он сгорит и никакого газа не получится. И тогда Мердок пошел по пути, который уже использовался при выжиге кокса из каменного угля – он стал греть уголь без доступа воздуха, но уже не в куче, а в закрытом котле – реторте, куда не мог проникнуть воздух. В кучах, в стойловых печах часть угля или древесины сгорала, а дымовые газы грели будущий кокс и вместе с химическими продуктами уходили в атмосферу. А у Мердока газ стал необходимым продуктом.
Газовый свет появился во многих городах. В 1811 г. французский журнал «Магазин всех новых изобретений, открытий и исправлений» писал: «Господин Лебен в Париже доказал, что рачительно собранным дымом можно произвести приятную теплоту и весьма ясный свет. Делая опыты над своим изобретением, сверх семи комнат осветил он целый сад».
В те времена газ произвел не меньшее впечатление, чем полупроводниковые приборы и запуски ракет в наши дни. В газетах можно было прочитать: «День и ночь может гореть огонь в комнате, не требуя для присмотра ни одного человека. Его можно провести с потолка, где он будет распространять по всей комнате свет свой, не оттеняемый подсвечником и омрачаемый копотью».
Газовый свет пришел в города и на заводы. В 1823 г. уже 55 городов и заводов в Англии были освещены газом. Резко увеличилась производительность в вечерние и ночные часы. А вскоре сотни газовых заводов стали давать свет городам Западной Европы и Америки.
Таким образом, в промышленно развитых странах уже в середине XIX в. на одних заводах термическое разложение – пиролиз угля – производили для изготовления кокса, а на других – для получения светильного газа. Первые не интересовались светильным газом, а для вторых кокс представлял второстепенный интерес.
Однако там, где преимущественно готовили кокс, газ просто сгорал. На газовых заводах положение оказалось более сложным. Газ, прежде чем передать потребителям, надо было очистить, охладить. Поэтому около реторт для светильного газа пришлось строить холодильники, которые охлаждались водой. В них из газа выделялись вязкая, черная каменноугольная смола и небольшое количество воды. Это вещество создало немалые трудности владельцам заводов. Даже на маленьком газовом заводе за год получали несколько сот тонн вязкой каменноугольной смолы. Ее приходилось сжигать, сливать в старые шахты. Некуда было девать и воду. Сначала ее пытались сливать в водоемы, но она загрязняла реки и озера, вода которых становилась непригодной для питья.
Постепенно из каменноугольной смолы научились извлекать полезные вещества. В 1815 г. было установлено, что из смолы при нагревании можно было отогнать смесь, заменяющую дорогой и дефицитный скипидар; из воды и смолы, образующихся при коксовании, стали получать карболовую кислоту (химики называют ее фенолом), которую применяли как дезинфицирующее вещество. При перегонке смолы получали темно-зеленое вязкое масло, которым начиная с 1830 – 1840 гг. пропитывали столбы, шпалы, тем самым увеличивая срок их эксплуатации. А из самой тяжелой и высококипящей части смолы стали изготовлять черный, густой лак, которым покрывали днище кораблей и металлические конструкции для надежной защиты от ржавчины.
Удивительным оказалось и другое свойство этого лака. Обычно днище корабля, приплывшего с южных морей, покрыто серо-зеленой бородой из водорослей, различных морских организмов, прижившихся на поверхности корабля. Внешний вид этой «бороды» создает определенный эстетический дискомфорт. Эти непрошенные гости ухудшают гидродинамические характеристики днища. При движении корабль встречает увеличивающееся сопротивление воды, скорость уменьшается, увеличивается расход топлива. Приходится тратить немало времени на очистку днища после каждого длительного плавания. А вот на днище, покрытом каменноугольным лаком, водоросли росли значительно медленней.
В XIX в. в каменноугольной смоле химики нашли сотни веществ, которые до сих пор удавалось получить либо из растений или животных, либо какими-то другими путями.
В 1825 г. великий Фарадей открыл в коксовом газе бензол. В 1830 г. Андерсен выделил из каменноугольной смолы нафталин, а в 1832 г. Дюма и Лоран – антрацен. Закладывались основы той синтетической органической химии, которая во многом определяет пути развития современной техники.
Однако долгое время изыскания химиков, казалось бы, реально ничего не давали. А практический интерес к органическим веществам рос с каждым годом. Научно-техническая революция XIX в. дала жизнь крупному машинному производству. Всего за несколько десятилетий кустарное производство тканей было полностью механизировано начиная от подгонки прядильных волокон и кончая нанесением разноцветных узоров на ситец. Но выпуск тканей тормозили красители, потому что еще до середины прошлого века пользовались красителями растительного и животного происхождения.
Из далекой Индии, Африки, Южной Америки и с Антильских островов привозили в дубовых бочках коричневое катеху, синее индиго, оранжевый орлеан – продукты грубой переработки тропических растений. Из трюмов выгружали тяжелые, громоздкие поленья тропических красильных деревьев – фернамбукового, сандалового, кампешевого. Красную краску – кармин получали из тлей, которых собирали на плантациях Мексики. Орсейль и кутбир готовили из лишайников, растущих на морских побережьях.
Приготовление красок – настоящее искусство, и поэтому оно долгое время оставалось тайной и нередко передавалось от отца к сыну и даже охранялось принесенными из средневековых цехов правилами и законами
Вот, как пишет об этом П. Н. Ершов в интереснейшей книжке «Химическая радуга» … «Весной 1856 года мастер Пуллар, владелец красильни в небольшом шотландском городе Перте (прославленном великолепным романом Вальтера Скотта «Пертская красавица»), получил письмо, к которому было приложено несколько кусков фиолетового шелка. Некий мистер Уильям Г. Перкин из Лондона сообщал, что им открыт способ получения нового красящего вещества. Он просил испытать образцы и сообщить свое мнение о них. Наметанный глаз сразу же обнаружил в окраске ткани нечто незнакомое. Нужные испытания Пуллар провел, не откладывая в долгий ящик.
В июне 1856 г. Уильям Г. Перкин получил ответ: «Если Ваше открытие не слишком удорожит товар, то это самое ценное открытие за многие годы. Такой цвет весьма нужен для товаров всех видов. Он никак не получается прочным на шелке, а для окраски хлопчатобумажной пряжи применяют очень дорогой способ. Я посылаю Вам образчик самого лучшего лилового цвета, какой можно получить на хлопке. Окрашивать хлопок в такой цвет умеют только в одной красильне во всем Соединенном Королевстве, но даже он недостаточно прочен и не выдержал испытаний, которые выдержали Ваши образцы. На шелке такая окраска еще менее прочна. Мы получаем этот цвет при помощи кудбира или орсейля».
По-видимому, 18-летний Перкин был обрадован такой высокой оценкой его первой самостоятельной работы. Именно он является создателем первого синтетического красителя и первого в мире завода для приготовления красителей из каменноугольной смолы, создания анилинокрасочной промышленности.
Этому открытию предшествовали исследования двух других ученых – русского и немецкого.
В 1842 г. в Бюллетене Санкт-Петербургской Академии наук было помещено сообщение профессора Казанского университета Николая Николаевича Зинина о новом способе получения анилина. Ранее Бутлеров обработал бензол (вещество, извлекаемое из коксового газа и каменноугольной смолы) азотной кислотой и приготовил желтоватую жидкость с характерным миндальным запахом – нитробензол. При нагревании нитробензола с раствором соляной кислоты, в который были брошены чугунные стружки, Н.Н. Зинин приготовил анилин – внешне ничем не примечательную маслянистую жидкость со своеобразным запахом. Анилин уже был известен, но получали его путем разложения индиго (дорогой синий краситель, который привозили из Индии). Таким же способом анилин получил в свое время русский академик Ю.В. Фритцше (по-испански индиго – анил).
Удивительным свойством анилина является его способность вступать в огромное число химических реакций, давая при этом вещества самой разнообразной структуры. Анилин оказался идеальным сырьем для разнообразнейших химических синтезов. И, пожалуй, больше всего интересовался анилином немецкий химик А.Ф. Гофман, обосновавшийся с 1845 г. в Англии. Его-то учеником и был Уильям Г. Перкин. Именно ему посчастливилось приготовить из анилина первый синтетический краситель. Однако эта работа осталась бы пылиться на полке, если бы к тому времени не появился простой метод приготовления анилина из бензола – продукта переработки угля. И не случайно А.В.Гофман в речи, посвященной памяти Зинина, сказал: «Если бы Зинин не сделал ничего больше, кроме превращения нитробензола в анилин, то имя его и тогда осталось бы вписанным золотыми буквами в историю химии».
Да, в руках химиков оказался простой и дешевый способ приготовления анилина из продуктов коксования угля – газа и каменноугольной смолы, и это стимулировало бурное развитие анилинокрасочной промышленности.
Появление этой отрасли послужило толчком в развитии химической промышленности. Так как для изготовления красителей потребовались чистые вещества, пришлось осваивать и развивать методы очистки и получения индивидуальных материалов. Потребовалась и тщательная очистка кислот и щелочей, идущих на производство красителей, а текстильная промышленность получила возможность выпускать яркие ткани разных расцветок.
Все это изменило отношение и к переработке угля. Стало просто невыгодным готовить только кокс или только светильный газ. Правда, к концу XIX в. на смену газового освещения пришло электричество, а газ тем временем стали использовать для отопления квартир: нет копоти, золы и сажи.
Теперь ценными продуктами одного завода стали и кокс, и газ, и смола, и некоторые другие вещества, содержащиеся в газе. Так появились заводы, чем-то напоминающие современные. На этих заводах стали готовить не только кокс и газ для металлургии, но извлекали и перерабатывали смолу, делили ее на составные части. Газ стали промывать маслом, чтобы извлечь из него бензол, и, промывая газ водой или кислотой, извлекали из него аммиак, который неожиданно приобрел особую ценность как удобрение.
Фосфорные и калийные удобрения научились изготовлять из природных фосфоритов и калийных солей, но где было взять азот? Взоры людей обратились к далекому тихоокеанскому побережью Южной Америки.
В далеком Чили миллиарды птиц многие тысячелетия питались рыбой у скалистых берегов и оставляли продукты ее переработки на скалах. Так возникли месторождения солей азотной кислоты, названные «месторождениями чилийской селитры». Сотни кораблей везли чилийскую селитру на поля Западной Европы и Северной Америки. Однако запасы ее были ограниченны. И выдающийся немецкий химик Юстус Либих – создатель науки об удобрениях – предупреждал об опасности азотного голода.
И, пожалуй, только коксохимическая промышленность в течение нескольких десятилетий серьезно подрывала монополию чилийских чаек, извлекая из коксового газа аммиак (3 – 4 кг на тонну угля). Аммиак, извлеченный из коксового газа, использовали для изготовления азотной кислоты, в содовом производстве и, в особенности, для изготовления сульфата аммония. В XIX в. это удобрение ценилось достаточно высоко.
Только в 1913 г. проблема связанного азота была решена: в Германии начал работать первый завод по синтезу аммиака из азота и водорода. Правда, водород для этого синтеза долгое время приготовляли либо из газов, получаемых газификацией кокса, либо разделением коксового газа. Ведь на сто кубометров коксового газа приходится 58 – 60 кубометров содержащегося в нем водорода.
В конце XIX в. коксохимическая промышленность в США и Западной Европе превратилась в отрасль, осуществляющую комплексную переработку угля и изготовлявшую из него самые разнообразные вещества.
С ростом мировой промышленности увеличивались масштабы коксохимической промышленности. Уже в начале двадцатых годов ХХ в. количество коксуемого в мире за год угля превышало сто миллионов тонн. Химические продукты коксования стали единственным сырьем для большинства отраслей химической промышленности. Один на персонажей книги «Гиперболоид инженера Гарина» мультимиллионер Роллинг высказывает предположение о том, что мир был создан Богом из каменноугольной смолы и небольшого количества поваренной соли.